- صفحه اصلی
- خدمات ریخته گری
- قالب گیری و مونتاژ در ریخته گری
تیم قالبگیری و مونتاژ قطعات ریخته گری شرکت آوانگارد مفتخر است با تکیه بر بیش از دو دهه تجربه ریخته گری بالغ بر ده هزار قطعه اعم از قطعات صنایع ماشین سازی-خودرو سازی-قالب سازی-نفت و گاز و پتروشیمی-صنایع نیروگاهی- صنایع سیمان و فراوری مواد معدنی در خدمت شما صنعتگران محترم باشد که با بهترین و بالاترین کیفیت و مناسب ترین قیمت خدمات خود را تقدیم شما عزیزان نماید.
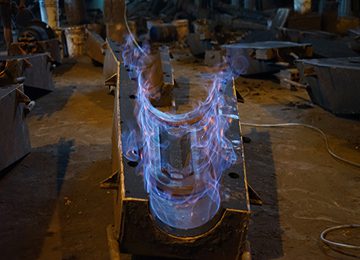
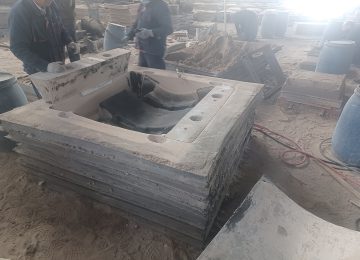
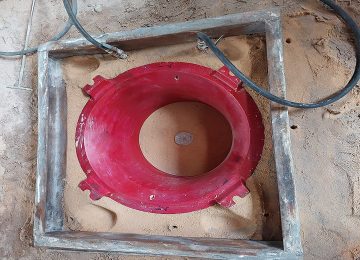
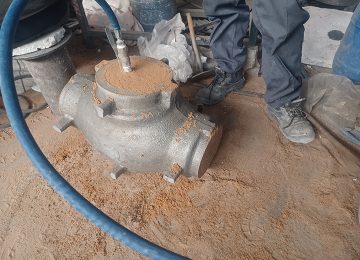
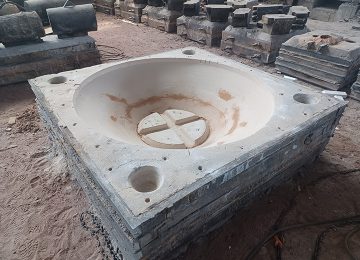
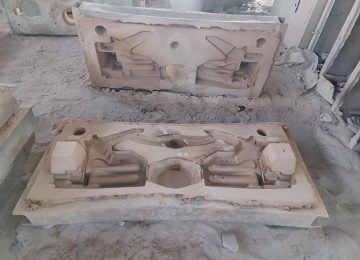
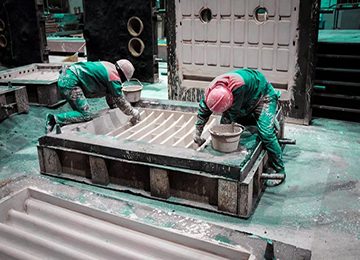
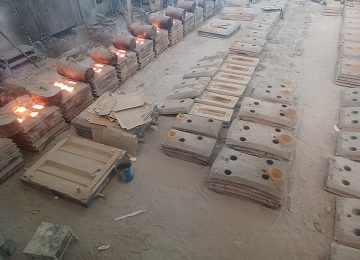

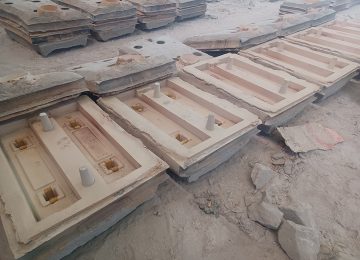
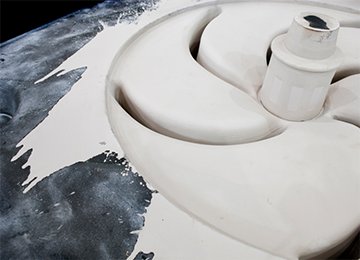
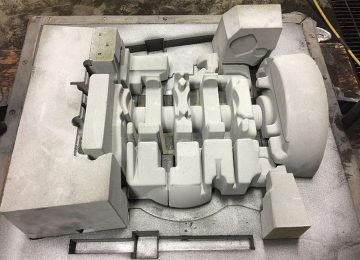
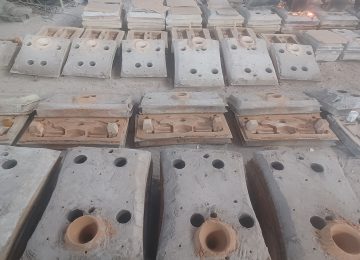
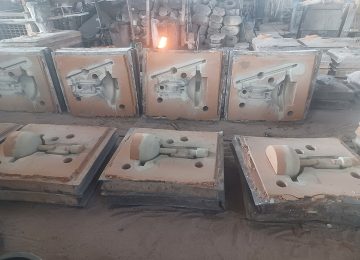
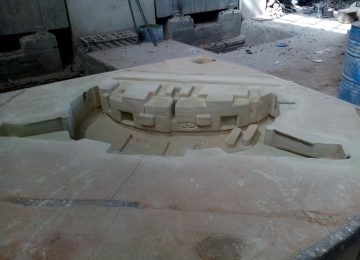
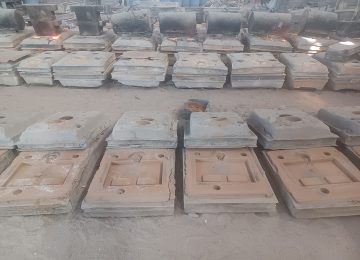
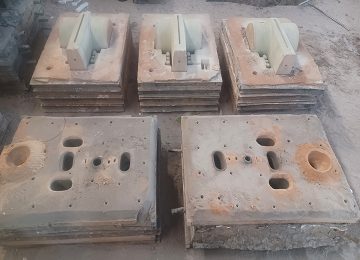
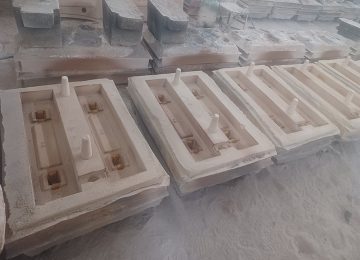
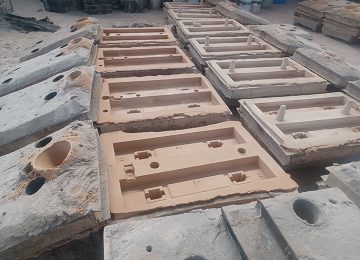
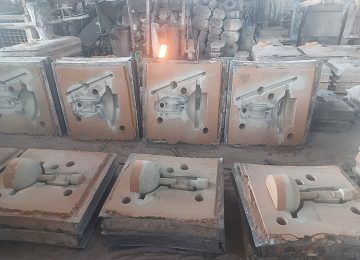
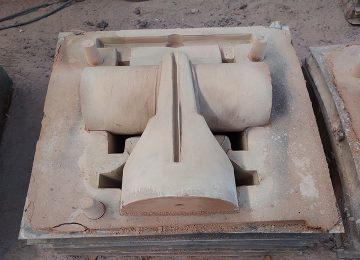
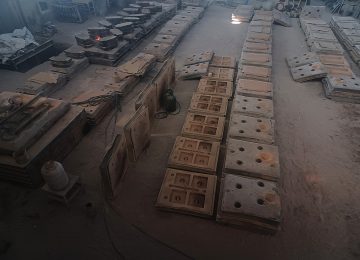
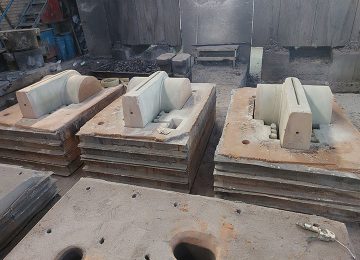
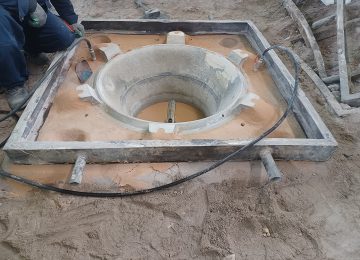
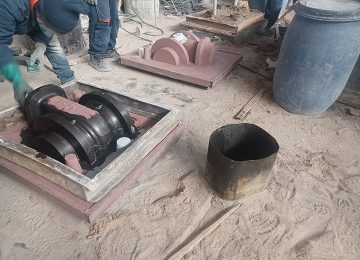
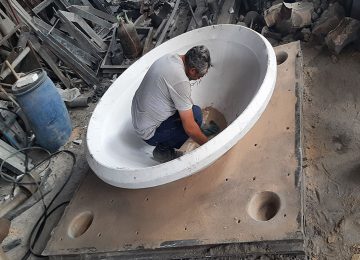
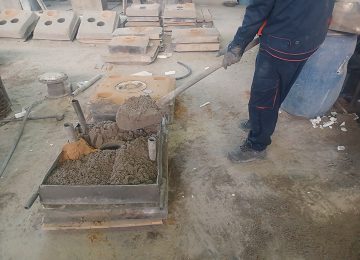
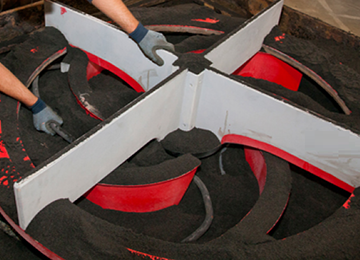
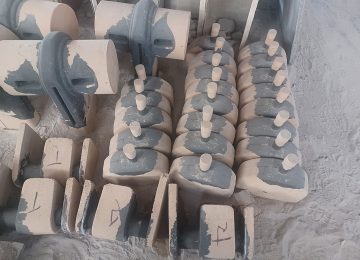
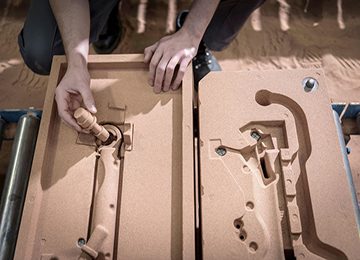
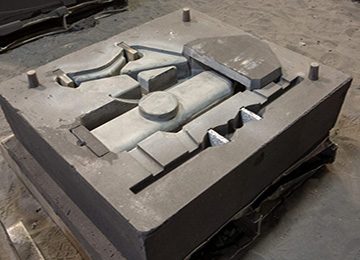
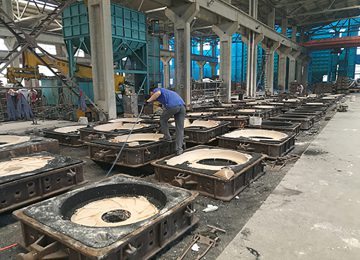
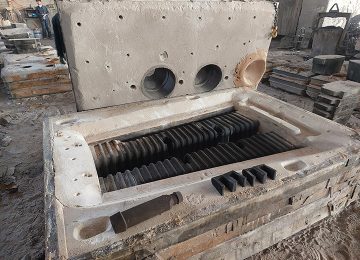
برای انتخاب مناسب ترین روش ریخته گری باید موارد ذیل را با درخواست های خود مطابقت دهیم:
1-کیفیت سطحی
2- دقت ابعادی
3- تعداد قطعات ریختگی
4-نوع مدل و ماهیچه
5- هزینه ساخت قالب
6- محدودیتهای موجود بواسطه نوع ماده انتخابی
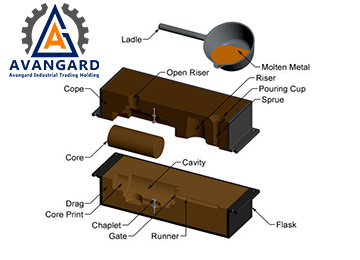
یکی از روش های رایج قالبگیری در صنایع ریخته گری، ریخته گری در قالب های ماسه ای است که در شرکت آوانگارد نیز از این روش استفاده می شود که در ادامه به بررسی این موضوع خواهیم پرداخت.
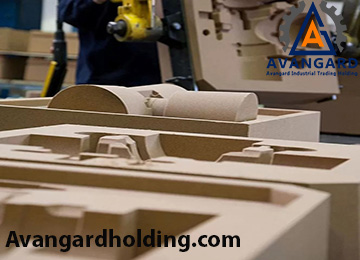
در روش ریخته گری ماده جامد قابل ذوب حرارت داده می شود و سپس در یک چاله تو خالی یا قالب ریخته شده تا پس از انجماد به شکل مدنظر درآید. در نتیجه در یک مرحله، تهیه هرشکل متنوع یا پیچیده از هر فلز قابل ذوب امکان پذیر می باشد. محدوده وزن و اندازه قطعات قابل تولید به روش ریخته گری بسیار گسترده است و از یک قطعه یک میلیمتری با وزن کمتر از یک گرم تا قطعات بزرگ چند تنی با ابعاد چند متری را شامل می شود.
فرآیند ریخته گری دارای مزیت های قابل توجهی در ساخت قطعات با قسمتهای توخالی، اشکال پیچیده، قطعات با حفره های داخلی، قطعات خیلی بزرگ، قطعاتی با سطوح منحنی شکل نامنظم و قطعات ساخته شده از فلزاتی که ماشینکاری آنها دشوار است، می باشد.
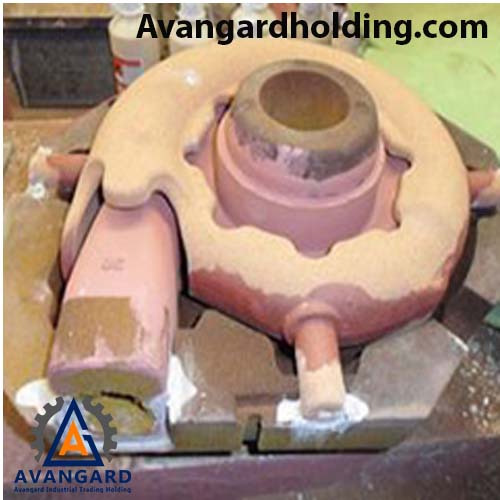
ریخته گری در ماسه Sand Casting
در این روش دانه های ماده دیرگداز (مانند سیلیکا) با مقادیر کمی مواد دیگر مانند خاک رس، چسب و آب مخلوط شده و در اطراف مدل که شکل قطعه مورد نظر را دارد، فشرده می شوند.
امروز فرایند طراحی در بسیاری از صنایع مثل ریخته گری و مدل سازی، خودروسازی، هوافضا، الکترونیک و غیره از طریق کامپیوتر انجام می شود. این روش طراحی به شرکت های طراحی این امکان را می دهد که در آغاز کار، طرح مورد نظر خود را ابتدا طراحی و سپس مدل سازی و مورد بررسی قرار دهند و در صورت تایید شدن مدل نمونه، آن را تولید و بهره برداری نمایند.

خصوصیات ریخته گری در ماسه
تقریبا هیچ محدودیتی در شکل، اندازه، وزن و پیچیدگی وجود ندارد و هر نوع فلزی را می توان ریخته گری کرد.
تلرانس و پرداخت سطح به خوبی روش های دیگر ریخته گری نیست و معمولا مقداری ماشینکاری لازم است.

ویژگی های اصلی ماسه مورد استفاده برای ریخته گری ماسه ای
1- استحکام در حالت خشک (Dry Strength)
2- استحکام در حالت تر (Green Strength): استحکام برشی و فشاری در کنج ها
3-استحکام در حالت حرارتی (Hot Strength): قالب سریع به دمای بالا می رسد، وقتی رطوبت خود را از دست می دهد نباید شکل خود را از دست بدهد زیرا باعث ایجاد ترک و خرد شدن یا زائده و پلیسه و رگه می شود.
4-قابلیت عبور گاز (Permeability): گاز متصاعد شده از پوشان و چسب و هوای داخل قالب باید خارج شود که به دانه بندی و شکل ماسه قالب و میزان رطوبت، چسب و کوبش بستگی دارد.
5-پایداری حرارتی (Thermal Stability): ضریب انبساط حرارت پایین داشته و ابعاد خود را حفظ کند.
6-دیرگدازی(Refractoriness): مواد قالب مقاوم به حرارت باشد و تغییر حالت نداده و سوخته و ذوب نشود.
7-قابلیت شکل گیری (Flowability): به اندازه دانه و مش آن بستگی دارد.
8-کیفیت سطحی (Produces Good Casting Finish): به خواص فیزیکی دانه ماسه بستگی دارد.
9-قابلیت فروپاشی (Collapsibility): تابع نوع و میزان چسب مصرفی است.
10-قابلیت بازیافت (Reusable)
11-تهیه و کنترل ساده
12-قدرت خنک کنندگی (Remove Heat)
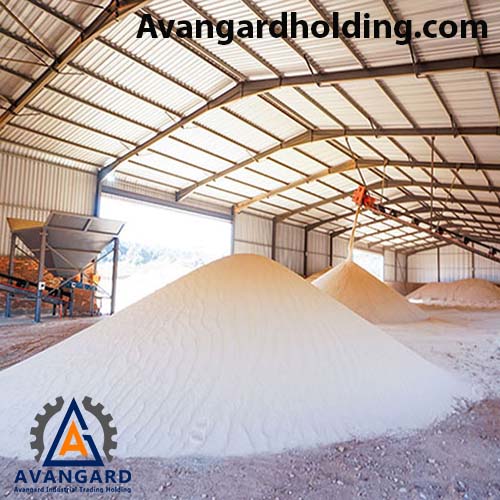
- ماسه سیلیسی
- ماسه کرومیتی
- ماسه اولوین
- ماسه زیرکون
- ماسه شاموتی
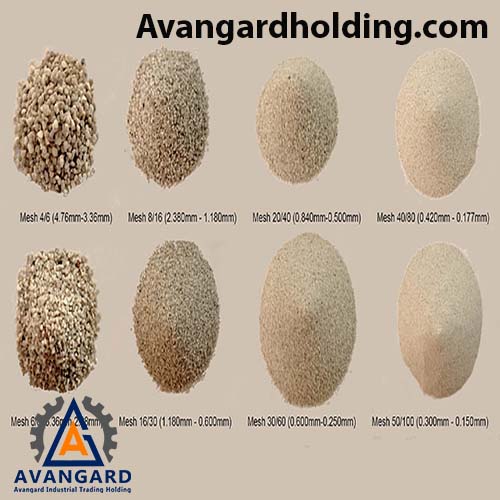
ترکیب شیمیایی ماسه سیلیسی SiO2 است و یکی پرکاربرد ترین و در دسترس ترین نوع ماسه از انواع ماسه های مورد مصرف در صنعت ریخته گري می باشد. معمولا جهت تولید قطعات با سایز های کوچک از ماسه های ریز دانه استفاده می شود و با افزایش سایز قالب از ماسه با دانه بندی بزرگتر جهت استحکام کششی و تحمل فشار بالا و افزایش استحکام قالب ها استفاده می شود. به طور معمول در اکثر ریخته گری های ماسه ای، ماسه سیلیسی مورد استفاده قرار میگیرد چون در طبیعت به طور فراوانی وجود دارد و دسترسی به آن نیز ارزان و ساده است. جهت حذف رطوبت در قالبهای حساس، برخی ریخته گرها، قالب های ماسه ای را ساعاتی قبل از ذوب ریزی داخل کوره خشک کن قالب، قرار می دهند و قالب را کاملا خشک می نمایند. قالب های ماسه ای از قالب های تر محکم تر بوده و دقت ابعادی بالاتری را نیز دارا می باشند. لازم بذکر است درجه نسوزندگی ماسه های سیلیسی نهایت تا دمای 1730 درجه سانتیگراد می باشد.
نوع ماسه | ترکیب شیمیایی | ||||||
SiO2 | Al2O3 | Fe2O3 | CaO | MgO | K2O | Na2O | |
ماسه سیلیسی مرغوب | 98 | 1.1 | 0.05 | 0.11 | 0.02 | 0.65 | 0.07 |
ماسه سیلیسی معمولی | 85 | 10 | 2 | 1 | 0.5 | 0.75 | 0.5 |
ماسه سیلیسی قرمز نامرغوب | 78 | 10 | – | 2.4 | 1.8 | 3.1 | 0.2 |
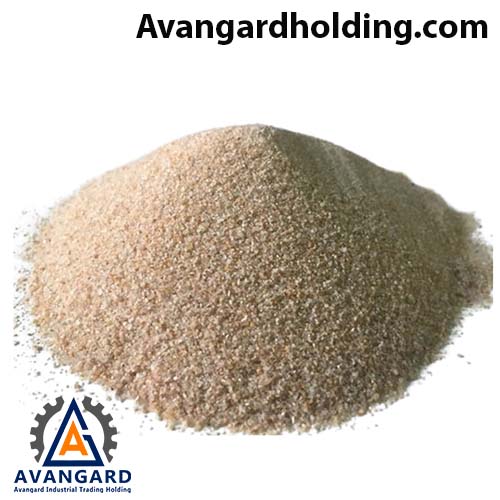
کرومیت به انگلیسی: (Chromite)، اکسید کروم منیزیم آهن با فرمول کلی (Fe,Mg)Cr2O4 و تنها سنگ معدن کروم کانی کرومیت در طبیعت می باشد. مهمترین مصارف کرومیت در تهیه عنصر کروم برای استفاده در ساخت آلیاژهای ویژه صنایع فولاد سازی می باشد. از دیگر کاربرد های کرومیت در صنایع ریخته گری استفاده از آن به صورت ماسه کرومیتی میباشد که اغلب در ریخته گری قطعات فولادی از آن استفاده می شود. ماسه کرومیتی به گونه ای است که می توان از آن در ساخت ماهیچه و قالب های ریخته گری استفاده نمود. رسانایی گرمایی بالا، خنک شوندگی سریع و دیرگدازی عالی و ضریب انبساط کم (تغییر اندازه ناچیز در برابر تغییر دما) باعث می شود تا شکل خود را حفظ کند و به دلیل عدم واکنش شیمیایی و خنثی بودن این ماده، این امکان را فراهم کرده تا بتوان از رنج وسیعی از رزین های پیوند دهنده به همراه آن استفاده کرد از این رو به دلیل مزایای اشاره شده و همچنین در دسترس بودن و کاهش مشکلات هنگام ریخته گری و قطعه سازی جایگاه خاصی را در بین ریخته گران دارا می باشد.
دانه بندی ماسهکرومیتی
دانه بندی ماسهکرومیت برای استفاده در صنایع برابر 0.7-0.2میلیمتر (ریزدانه) ، 3-0.7 میلیمتر (دانه متوسط) و بالای 3 میلیمتر (دانه درشت) است که با توجه به کاربرد و زبری سطح، مورد استفاده قرار میگیرد. شکل دانههای ماسه کرومیتی باید به شکل کروی باشد تا در حین استفاده اجازه خروج گاز از قالب فراهم شود. اگر شکل دانهها به صورت تیز و غیر کروی باشد میزان چسبندگی ماسه کاهش مییابد و موجب بروز عیوب مختلف در قطعه ریخته گری شده می شود.
گرید بندی ماسه کرومیت
ماسه کرومیت عموما در سه گرید B ، A و C موجود است:
- گريد A متشكل از كروميت با کروم بالا و با نسبت کروم به آهن 2.5 و کروم دارای عيار بالاي 64 درصد است
- گريد B متشکل از كروميت با نسبت کروم به آهن 2.5 – 1.8 و کروم دارای عيار 64-56 درصد است
- گرید C متشکل كروميت با آهن بالا (High Fe) با نسبت کروم به آهن 1.8 و کروم دارای عيار 55 – 50 درصد است
مهمترین خواص ماسههای کرومیتی عبارتند از:
- پایداری حرارتی بالا
- خواص دیرگدازی بسیار عالی
- عدم تر شوندگی توسط مذاب فلزات
- مقاومت بالا در برابر نفوذ مذاب
- پایداری شیمیایی مطلوب
- دمای ذوب 2150 درجه سانتیگراد
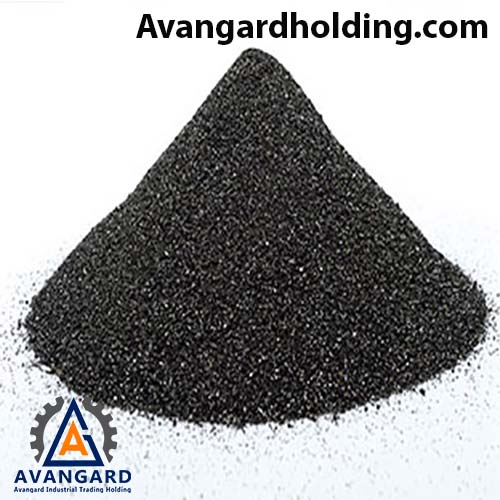
ماسه اولوینی به دلیل دارا بودن نقطه ی ذوب و زینتر بالا، اتلاف حرارتی کم و مقاوم در برابر شوک های حرارتی در فولاد سازی و صنایع نسوز کاربرد دارد. بخش اصلی و عمده این ماسه از Mg2SiO4 ( فورستریت) و جزء کمتری از Fe2SiO4(فایالیت) تشکیل شده است. ماسه اولوین EBT به عنوان ماسه کف ریز مجرای کوره قوس الکتریکی استفاده می شود. ماسه اولوین ریخته گری برای ساخت انواع فولادها از جمله چدن چکش خوار و چدن خاکستری مناسب بوده و همچنین برای ریخته گری ترکیبات غیر فلزی مزیت های فراوانی دارد. این نوع ماسه به خصوص بابت داشتن سطحی بسیار صاف در تولید قطعات ریخته گری فولادهای منگنزی، در جایگاه بالایی قرار دارد.
اوليوين
نام اولوين از رنگ سبز زيتوني آن گرفته شده است. پريدوت نام قديمي گونه هاي اوليوين مي باشد. ترکيب شيميايي کلي اوليوينها به صورت Mg2SiO4است. اوليوينهایی که سرشار از منيزيم هستند رنگ سبز متمایل به زرد و سبز و زيتوني و اوليوين هاي پر از آهن سبز متمایل به قهوه اي دارند. سختي آنها بين 7-6.5مي باشد.
محيط پيدايش اولیوينها
اوليوين کاني نسبتاً رايج در داخل سنگ هاي آذرين دروني و خروجي بازيک و اولترابازيک نظير گابرو، بازالت، پريدوتيت و دونيت است. دونيت یک نوع سنگ است که 95 درصد ساختار آن از اوليوين تشکيل شده است. سنگ دونیت که مهمترینن و باارزشترين سنگ از لحاظ اقتصادي براي تولید اوليوين می باشد همراه با کمپلکسهاي اولترابازيک مثل کمپلکس بوشفلد، اسکارگارد و دايک بزرگ زيمبابوه و يا همراه با مجموعه هاي افيوليتي مشاهده میگردد. اوليوين به صورت دانه هاي شيشه اي در شهاب سنگها نيز مشاهده مي شود. اوليوين ها در صورت دگرساني به کانيهاي گروه سرپانتين مثل کريزوتيل، منيزيت و اکسيد آهن تبديل مي شوند.
کاربرد اولوينها
از اوليوين به طور وسیعی در صنايع ديرگداز استفاده مي شود. اولوين به دليل نقطه ذوب بالا (1890 درجه سانتي گراد)، رسانايي گرمايي خوب، ظرفيت گرمايي بالا (که به آن مقاومت در برابر شوک گرمايي مي دهد ) و ضريب انبساط گرمايي کم، به عنوان رکن اصلی ماسه ريخته گري استفاده مي شود. مزیت ديگر اوليوين آن است که مانند ماسه هاي سيليسي براي سلامتي ضرر نداشته و خطر ابتلاء به بيماري سيليسکوسيس براي کارگران وجود ندارد. يکي ديگر از کاربردهاي اوليوين، بدليل سختي 7-6.5 استفاده از آن در صنايع شستشوي ماسه اي است.
کاربرد ديگر اوليوين، توليد سرباره در تهيه فولاد از آهن به جاي آهک و دولوميت است. از ميان کاربردهاي اوليوين مي توان به تولید آجر ديرگداز اشاره کرد. چگالي بالاي اوليوين دلیل استفاده از آن به عنوان بالاست در سکوهاي نفتي درياي شمال و نيز پوشاندن لوله هاي زيردريايي می باشد. بالاست شامل خرده سنگهاي زاويه داري است که خطوط راه آهن بر روي آنها قرار داده می شوند. ا
توليد کننده هاي اوليوين در دنيا
اسپانیا و نروژ اصلی ترین توليدکننده اوليوين در جهان هستند. معادن ذخایر اصلی و مهم سنگ دونیت و ماسه الوین در کشورهاي سوئد، روسيه، استراليا، ژاپن، نيوزلند، زيمبابوه، آفريقاي جنوبي، آمريکا، کالدونياي جديد، ايتاليا، يونان، هند، برزيل و کانادا می باشد.
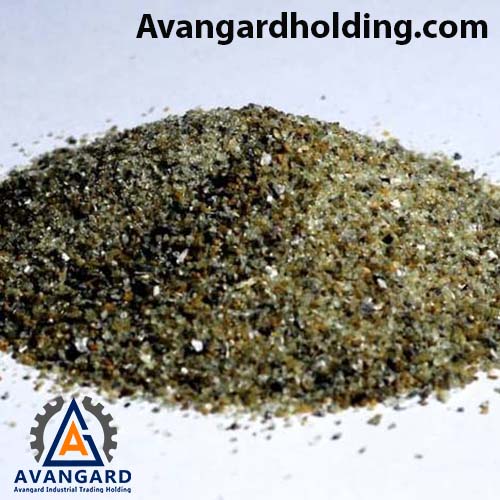
ماسه زیرکون با ترکيب شیمیایی (ZrO2.SiO2) مشخص می شود و به عنوان یک ماسه با نقطه گداز بسیار بالا در برخی قالبها مصرف می گردد. زیرکون در طبیعت همراه با سیلیس است. ماسه زیرکون دارای غلظت بین 40 الی 50 درصد می باشد.
ماسه زیرکون دارای ویژگی انبساط حرارتی می باشد و ضریب انبساط حرارتی ماسه زیرکونی از ماسه سیلیسی کمتر است و برای مواد قالب و آجر و بدنه کوره مناسب است. تحمل دمایی ماسه زیرکونی بالاست که سبب خاصیت دیرگدازی بالای آن می شود، درنتیجه برای فلزات با دمای ذوب بالا کاربرد دارد (نقطه ذوب بالای 2400 درجه و دمای زینتر شدن آن حدود 2000 درجه سانتیگراد است). هدایت حرارتی ماسه زیرکونی حدودا 4 برابر ماسه سیلیسی است که سبب سریع تر خنک شدن آن می شود. دارای دانسیته 4.75 گرم بر سانتیمتر مکعب است که حدودا 2 برابر ماسه سیلیسی است که این یک مزیت است زیرا در واقع وزن مخصوص قالب را زیاد می کند و یک بخش از نیروی مذاب را خنثی می کند. از خصوصیات دیگر ماسه زیرکونی، دانه های منظم و کروی و عدم خیس شدن توسط مذاب (عدم ماسه سوزی) و نداشتن تمایل به واکنش شیمیایی با بیشتر فلزات است و اگر سرباره یا مذاب، دارای متریالی باشند که باعث خوردگی بدنه کوره شود، این ماسه مقاوم و مناسب است.
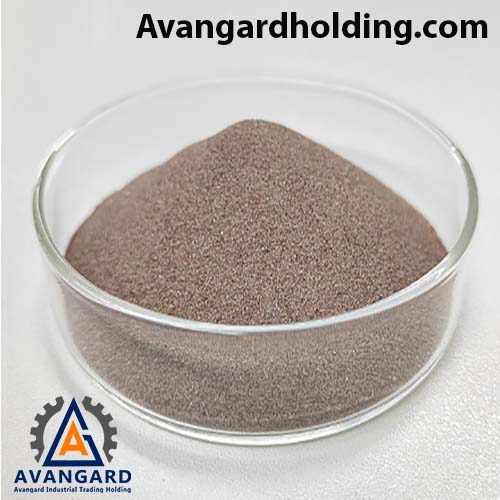
ماسه شاموتی با ترکیب شیمیایی (3Al2O3.SiO2) برای قطعات ضخیم و بزرگ مناسب است و از زینتر کردن خاک رس بدست می آید. مزیت این ماسه نسبت به سیلیس یکنواختی و کم بودن تغییر حجم آن در اثر تغییرات درجه حرارت می باشد و به علت اینکه دیرتر وارد فعل و انفعالات شیمیایی شده و به صورت ناچیز به سطح قطعه می چسبد در فولاد ریزی بکار می رود. این ماسه دارای دیرگدازی 1750-1670درجه سانتیگراد است که هر چه Al2O3 بیشتر باشد، بهتر است. ماسه شاموتی در ریختگری برای آجر و بدنه کوره کاربرد دارد.
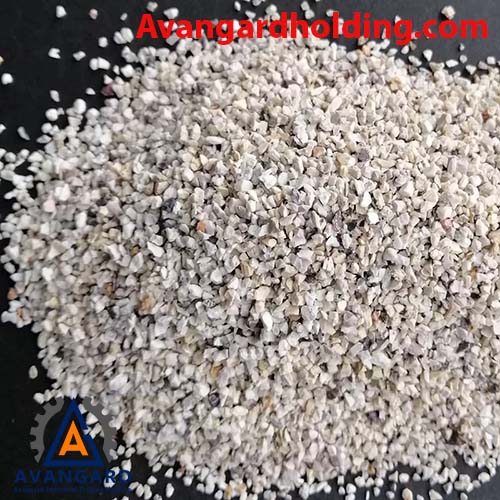
در بین ماسه هایی که در مورد آنها سخن گفته ایم، ماسه سیلیس با خلوص بالا برای عملیات قالبگیری ماسه ای بیشترین کاربرد را دارد. برخی از کشورها مانند آلمان، بلژیک، هلند و فرانسه، ماسه با کیفیت بسیار مناسبی دارند SiO2=99.8% ، ولی کشورهای دیگر همانند ایتالیا یا ژاپن برای ریختهگری آهن و فولاد، با کیفیت بالا، باید ماسه وارد کنند.
بدیهی است که هنگام استفاده از ماسههایی با مقادیر بیشتر اکسیدهای قلیایی (K2O، CaO ،Na2O و MgO )، عامل پختهای اسیدی به میزان بیشتری نیاز است.
از مزایای ماسههای سیلیسی مورد استفاده در این صنعت، ارزان بودن، فراهم بودن در گریدهای مختلف، سازگاری با انواع چسبهای شیمیایی، مقاومت حرارتی و شیمیایی کافی در تماس با فلزات مذاب و امکان ساخت قالب و ماهیچه با ابعاد مختلف است.
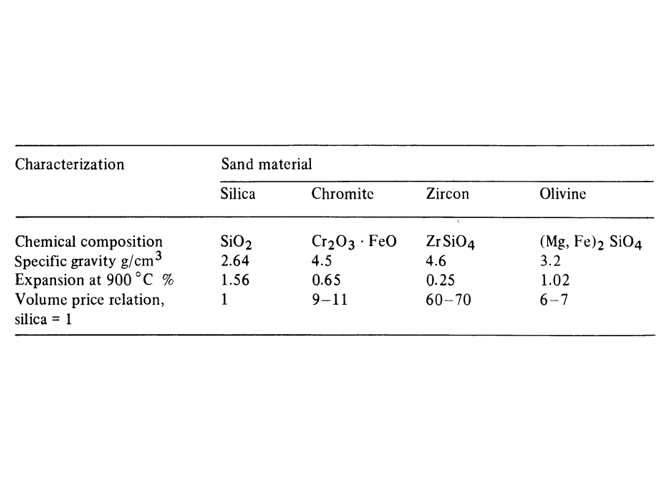
تمامی رزین های فنولیک، فنولیک-یورتان، فورانی و سدیم سیلیکات در صنایع ریختگری به اسم چسب مورد استفاده قرار می گیرند. رزینهای مناسب به عنوان چسب و عامل اتصالدهنده ماسهها در این صنعت، میبایست ویژگی های زیر را دارا باشند:
–زمان پخت کوتاه
– قیمت مناسب
– پایداری ابعادی بالا
– سختی و خواص مکانیکی مناسب ماهیچه
– کیفیت سطح ریختهگری بالا
– فروپاشی مطلوب قالب یا ماهیچه
رزین فنولیک با توجه به نسبت مولی فرمالدهید به فنول و با توجه به نوع کاتالیزور واکنش دهنده به کار رفته برای واکنش این دو مونومر، که ممکن است بازی یا اسیدی باشد، به دو صورت رزول و نوالاک تهیه میشود. رزین رزول بدون وجود عامل پخت، فقط با دما پخت میشود (گرچه وجود کاتالیزور سبب سرعت گرفتن در زمان پخت میشود.) اما نوالاک، رزینی گرمانرم بوده و برای شبکهای شدن نیاز به عامل پخت هگزامین دارد.
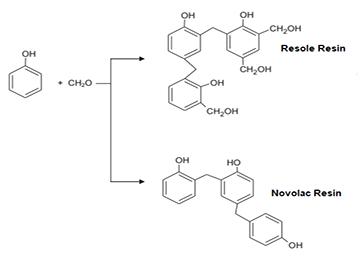
ساختار شیمیایی رزین های فنولیک یورتان، سدیم سیلیکات به طور مختصر در شکل زیر آورده شده است.
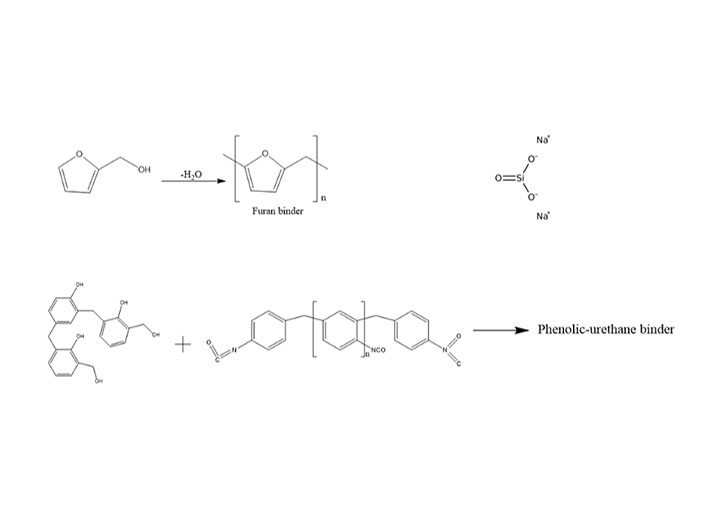
انواع چسب های مورد استفاده بر اساس ماهیت:
1- چسب های آلی
2- چسب های معدنی
انواع چسب های مورد استفاده براساس سفت شدن و خودگیری :
1- قابلیت حل شدن در آب يا آبدار
2- نداشتن قابلیت حل در آب يا غير آبدار
يك چسب بهینه و خوب دانه های ماسه را به يكديگر متصل کرده و استحكام نهایی قالب و ماهيچه را در حالت خشك و تر زیاد می کند و باید شرايط زير را بوجود آورد:
1- در طی تهيه مخلوط هاي ماهيچه یا قالبگيري بطور يكنواخت بر روي سطوح ماسه پايه گسترده شود.
2- دادن استحکام مناسب به مخلوط ماسه در حالت خشک و تر.
3- دادن شكل پذيري بهینه و کافی به مخلوط به گونه ای که مخلوط قابلیت پر کردن همه بخشهاي قالب را داشته باشد.
4- حداقل چسبندگي لازم به سطح مدل و جعبه ماهيچه
5- قابلیت خشك كردن سريع قالب و ماهيچه و عدم جذب رطوبت توسط مخلوط
6- تولید حداقل گاز ممکن به هنگام ذوب ریزی
7- عدم کاهش قابلیت دیرگدازی ماسه.
8- امکان تخریب راحت ماهیچه بعد از ذوب ریزی.
9- براي افرادي كه عمليات تهيه مخلوط قالب و ماهيچه را انجام مي دهند مضر نباشد و گازهاي سمي ايجاد نكند.
10- ارزان و در دسترس باشد.
چسب های ماهیچه خیلی گسترده و متنوع بوده و انواع زیادی دارند و هر کدام از این چسب ها به منظور ویژه و ارائه خواص به خصوصی به ماسه ماهیچه اضافه می شوند. بیشتر چسب های ماهیچه (که در در ساخت قالب نیز در بسیاری از موارد به کار می روند) بعد از اولین استفاده به دلیل تغییرات ساختاری قابلیت استفاده دوباره را ندارند. چسب های مورد استفاده در ساخت ماهیچه را به چهار گروه می توان تقسیم کرد:
1- چسب هایی که هنگام منجمد شدن سفت و محکم می شوند:
آب تنها ماده چسبناک است که در دسته بالا در عملیات ریخته گری مورد استفاده قرار می گیرد. در قطعاتی که در کشور روسیه به کمک این نوع چسب ساخته شده اند ،ادعا شده که حفره های داخلی در پوسته های قطعات با استفاده از ماهیچه های یخ زده حذف می شود.
2- چسب هایی که در دمای اتاق سخت و محکم می شوند:
از این نوع می توان سیلیکات سدیم و سیلیکات های مضاعف کلسیم و آلومینیوم یا سیمان را نام برد که توضیحاتی درباره چسب سیلیکات سدیم بصورت جداگانه، در ادامه به طور کامل داده می شود.
از چسب های سیمان می توان سیمان کائوچوئی، سیمان پرتلند و سیمان شیمیایی را نام برد که بهترین و مهم ترین این نوع سیمان ها ( به عنوان چسب)، سیمان پرتلند است.
عیوب ماهیچه های تولید شده از این چسب های سیمانی این است که مزیت از هم پاشیدگی آن قالب ساخته شده کم است.
3- چسب هایی که پس از پخت سخت و محکم می شوند:
این چسب ها به سه دسته فرعی زیر تقسیم می شوند:
1-3- چسب هایی که با دما و حرارت خشک می شوند(روغن ماهیچه):
در روغن ها سخت کردن از روش پلاریزاسیون و تشکیل مولکول های درشت تر به کمک جذب اکسیژن هوا در دماهای 200 تا 240 درجه سانتیگراد انجام می گیرد. این چسب ها تشکیل شده از سه نوع از چسب های روغنی، به نام های روغن های جانوران دریایی ،روغن های گیاهی و روغن های معدنی می باشد.
2-3- چسب هایی که بعد از گرم شدن و در موقع سرد شدن سخت می شوند:
انواع رزین ها یا به عبارتی صمغ ها در این دسته وجود دارند. صمغ به دو نوع مصنوعی و طبیعی دسته بندی می شوند.که از صمغ های طبیعی می توان به شیره درختان اشاره کرد.
رزین ها از نوع اوره فرمالدئید بیشترین کاربرد و بهترین مشخصات را در تهیه ماهیچه های نازک و کوچک و آن هایی که پس از ریختن مذاب قابلیت از هم پاشیدگی زیادی لازم دارند، را ارائه می دهند. فنل فرمالدئید قابلیت از هم پاشیدگی کمتری دارد و در تهیه قطعات فولادی بزرگ به کار می رود. این صمغ به صورت مایع و جامد در بازار وجود دارند و برای زمان زیادی نباید انبار شوند.
3-3- چسب هایی که ویژگی چسبندگی را در حرارت به دست می آورند:
این گروه از چسب ها شامل چسب های نشاسته ای (دکسترین)، چسب های سولفیدی، چسب های پروتئینی، ملاس چغندر قند هستند. دکسترین ها یا چسب های نشاسته ای جزو چسب های ماهیچه ای می باشند و معمولا جهت افزایش استحکام تر در مخلوط ماسه ماهیچه مصرف می شوند. مقدار 0.5 تا 2 درصد وزنی آن ها استحکام فشاری تر ماسه را به اندازه 1 تا 2.5 پوند بر اینچ مربع افزایش می دهد.
ملاس چغندر قند محصول فرعی کارخانه های قند می باشد که اصولا همراه با چسب های دیگر (به جز چسب های روغنی) به ماهیچه اضافه می شوند. چسب های پروتئینی نیز از انواع خالص تجاری آن کازئین، ژلاتین و سریشم می باشد.
4- چسب های خاک رس:
این گروه از چسب ها اصولا به خاطر بالا بردن استحکام تر ماسه ماهیچه به ترکیب ماسه ماهیچه افزوده می شوند و مهم ترین آن ها خاک رسی نسوز (کائولین) و بنتونیت می باشند که در چسب های قالب گیری نیز به آنها اشاره شد.
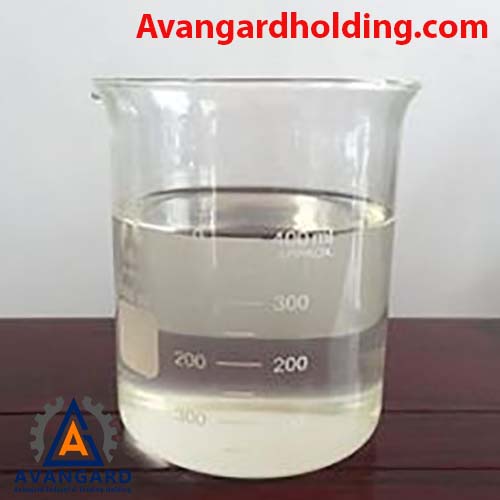
اضافه بر سه جزء اصلی ماسه قالبگیری (ماسه، آب و چسب) مواد دیگری جهت افزایش کیفیت و برطرف کردن بعضی از نقص های خاص به مخلوط افزوده می گردند، چنین موادی خیلی زیاد هستند بنابراین در اینجا به برخی از آنها که کاربرد استفاده زیادتری دارند اشاره می شود:
1-گرد ذغال:
Fe2O3 تولید شده در مذاب تولیدات آهنی (چدن و فولاد و…) در اثر تماس با دیواره های قالب که اغلب از جنس سیلیس (نوع ماسه) است واکنش داده و سبب تولید ترکیب فایالیت می شود که باعث سوختن ماسه ایجاد ماسه سوزی در سطح قطعه می شود.
بخاطر اضافه کردن پودر ذغال سنگ یک محیط احیائی به وجود می آید که ناشی از سوختن زغال و خروج گاز Co2 و هیدروژن و هیدروکاربیدهای سبک است، . در نتیجه این عمل، از اکسیداسیون سطح مذاب و ایجاد گاز زود گداز فایالیت جلوگیری می شود. لذا در نهایت باعث عدم چسبیدن ماسه به قطعه و افزایش صافی سطوح قطعات ریختگی میگردد.
همچنین با اضافه کردن این ماده از عیوبی مانند انبساط حرارتی میتوان جلوگیری نمود. زیرا به وسیله انقباض پودر ذغال در اثر حرارت می توان انبساط ماسه را در اثر افزایش دما جبران نمود. همچنین قابلیت خرد شدن ماسه را بهبود می بخشد زیرا ماسه کمتر کلوخه می شود و سریعتر روی shake out خرد می شود.
ویژگی و خاصیت های یک پودر زغال بهینه به شرح ذیل می باشد:
الف) مواد فرار موجود در آن بالا باشد (حدودا 30-26 درصد).
ب) میزان خاکستر باقی مانده در ذغال نباید بیشتر از 10 درصد شود.
ج) پارامتر مهم دیگر گوگرد موجود در ذغال است، زیرا گوگرد در چدنهای خاکستری تمایل به ایجاد chilled دارد و مقدار گوگرد باید از %1 بیشتر نشود.
مقدار استفاده از خاک ذغال برای قطعات با وزن تا 1000 کیلو گرم، 2 تا 4 درصد و برای قطعات سنگین که گرمای حاصل از ذوب ریزی و انجماد بالاتر بوده و مقدار عمق ماسهسوزی بیشتر است میزان مصرف ذغال تا 8 درصد نیز میرسد.
2-حبوبات، غلات(Cereals)
چسب غلهای مصرفی در ریختهگری عبارت است از نشاسته ژلاتینی و یا پودر ذرات ریز که از غلات گرفته شده است. نشاسته را میتوان در ماسههای قالبگیری به منظور افزایش استحکام تر یا خشک یا بالا بردن قابلیت فروپاشی (Collapsibility) تا حد 2 درصد به کار گرفت. از آنجایی که نشاسته فرار است، استفاده نادرست از آن میتواند باعث ایجاد عیوب گازی (Gas Defect) در قطعات شود.
3-گرد چوب(Wood Flour):
گرد چوب یا دیگر مواد سلولزی مثل گرد ذرت یا غله، پوسته حبوبات و سلولز را میتوان به مقدار 0.5 تا 2 درصد به ماسههای قالبگیری افزود. این قابلیت کنترل انبساط ماسه را دارد. مواد سلولزی پس از افزایش دما مشتعل میشوند و بعد از سوختن فضای خالی ایجاد می کنند و از این روش انبساط مخلوط ماسه قالب گیری کنترل می شود. مواد سلولزی و گرد چوب قابلیت پاشش و مزیت جاری شدن (Flowability) را نیز اصلاح می کنند و به همین دلیل خارج سازی قطعه از قالب با سهولت بیشتری انجام می گیرد.
4-پودر سیلیس:
سیلیس سائیده شده و نرم که مش آن کمتر از 200 باشد پودر سیلیس (Silica Flour) نامیده می شود. پودر سیلیس را تا 35 درصد به منظور افزایش استحکام گرم می توان به ماسه اضافه کرد. پودر سیلیس چگالی (bulk-density) ماسه را افزایش می دهد و به همین دلیل ماسه قالبگیری به دلیل فشردگی بالا مقاومت زیادتری در برابر نفوذ فلز مذاب دارد.
5-اکسید آهن:
اکسید آهن به مقدار ناچیز در بعضی ماسه های قالبگیری به برای بالا بردن استحکام گرم به کار می رود.
6-ملاس(Molasses) ،دکسترین(Dextrin):
ملاس چغندر یا ملاس ساقه نیشکر که تصفیه نشده و حاوی 60 تا 70 درصد شکر باشد را می توان برای بالا بردن استحکام خشک ماسه و افزایش سختی لبه قالب ها به کار گرفت. دکسترین یا صمغ نشاسته را می توان برای همان اهداف مورد استفاده قرار داد.
7-پرلیت:
پرلیت (perlite) یک سیلکات آلومینیم معدنی می باشد که منبسط شده است. این ماده به مقدار کم و در حد 1.5-0.5 درصد به منظور پایداری حرارتی (thermal stability) بهتر ماسه به کار می رود، این ماده می تواند برای عایق کننده های اسلیو تغذیه نیز مورد استفاده قرار گیرد.
8-آسفالت(Asphilt)
یک محصول جانبی حاصل از تجزیه نفت خام است. آسفالت نیز همانند قیر به منظور افزایش استحکام گرم، بهبود سطح تمام شده قطعات ریختگی آهنی مورد استفاده قرار می گیرد.
9-قیر زمینی
قیر یک محصول از کک سازی است. طی عملیات کک سازی،قیر در دمای 3.5 درجه سانتیگراد از ذغال جدا می شود. قیر تا مقدار 3 درصد و برای اصلاح استحکام گرم و بهبافزایش کیفیت سطح نهایی قطعات در مخلوط های ماسه برای ریختگری قطعات آهنی به کار می رود.
10-گیلسونیت
گیلسونیت یک ماده آسفالتی جامد است که در برخی از معادن دنیا استخراج می شود. این ماده فرار است و عملکرد آن شبیه تاثیر زغال در افزایش بهینه سازی تمام شده قطعات است.
11-روغن سوخت
روغن سوخت برخی اوقات به میزان بسیار کم و در حد 0.01-0.1 درصد در مخلوط قالبگیری به کار می رود و به نظر می رسد که این ماده قابلیت قالب گیری ماسه را بهبود می بخشد.
12-اکسید آهن قرمز
اکسید آهن قرمز با مقدار ظرفیت 1500تن تولید سالیانه برای استفاده در صنایع رنگ، پرایمر فلزی، لعاب، کاشی و سرامیک با مش 2500 در حال تولید است که با نمونه واردات شده آن بطور کامل قابل رقابت است که مشخصات آن به شرح ذیل می باشد:
اکسید آهن مخصوص ماهیچه ریخته گری :
اکسید آهن مخصوص ماهیچه ریخته گری در نوع سیاه رنگ و با قابلیت دانه بندی خاص طبق نظر مشتریان و به صورت ترکیبی از Feo,Fe2o3,Fe3o4 جهت افزونه به ماهیچه ریخته گری و ایجاد خاصیت مطلوب در ماهیچه ریخته گری تولید می گردد.
استفاده از اکسید آهن در انواع مختلف سیاه و قرمز از نظر متخصصین ادتیو ماسه Enginered Sand Additive_ESA بعنوان یک ماده افزودنی فعال و مناسب توصیه گردیده است و در عمل نیز با شرایط کارگاهی مورد تست قرار گرفته و تاثیرات آن عیناٌ دیده شده است. اکسید آهن افزوده شده در انواع مختلف مخلوط ماسه از نظر اثر آن برخواص ماسه و بررسی افزایش مقاومت در برابر رگه یا چروک های ایجاد شده بر روی سطح قطعات ریختگی تست شده است.
اکسید آهن قرمز در پیشگیری از ایجاد چروک یا رگه بر روی سطح قطعات ریخته گری موثر می باشد ولیکن بدلیل پودر بودن و فاقد دانه بندی بودن و مقدار اکسیژن عوارض جانبی یا تاثیرات مغایری بر سطح تمام شده قطعـه ریختگـی دارد. اکسیـد آهن سیاه افزوده شده به میزان 3 درصد در سیستم هات باکس و 2 درصد در سیستم کلد باکس برای حذف رگه یا چروک کارآمد بوده و تاثیر مخرب کمتری بر کیفیت سطح خواهد داشت از دلایل دیگر استفاده از اکسید آهن کاهش چسبیدن کربن به قطعه و نیز جلوگیری از ایجاد مک سوزنی و ایجاد فرورفتگی یا برجستگی نیم کره ای شکل در قطعه کار و نیز ایجاد مقاومت در برابر نفوذ آهن در قالب می باشد.
بطور کلی تاثیر اکسید آهن در ماهیچه گیری و هدف از مصرف به شرح ذیل می باشد:
الف) هدف از مصرف :
باعث افزایش پلاستیسیته گرم و کاهش یا از بین رفتن عیوب رگه رگه شدن و نفوذ مذاب و کم شدن عیوب گازی می باشد .
ب) تاثیرات مصرف اکسید آهن در ماهیچه گیری :
1-افزایش استحکام خشک ماهیچه های تولیدی .
2- کاهش تاثیرات مک سوزنی ریز سطحی نیتروژنی و هیدروژنی
3- کنترل مطلوب انبساط حرارتی ماهیچه .
4- بالا بردن استحکام گرم ماهیچه .
5- جلوگیری از نفوذ ذوب در ماهیچه و ایجاد فایالیت مناسب و سخت در سطح ماهیچه که از نفوذ گاز نیتروژن موجود در رزین Hot box به داخل مذاب جلوگیری می نماید.
6- کنترل اتمسفر قالب با آزاد سازی اکسیژن که اتمسفر قالب را از حالت احیاءکنندگی زیاد محافظت می نماید، نقش مهمی در بهبود کیفیت سطح دارد.
13-پودر قلع و پودر قلع – آنتیموان
بخاطر تاثیر بر ساختار سطحی چدن هایی که با ماهیچه های رزینی در تماسند در مواد پوششی قالبشان به کار برده می شوند. قلع و ترکیب بین فلزی قلع – آنتیموان موجب پایداری فاز پرلیت شده و لایه های سطحی فریتی را حذف می کنند.
14-دکسترین
دکسترین یکی از انواع هیدروکربور صمغی است و از تجزیه نشاسته به وسیله اسیدها و یا با حرارت و یا مخمر بدست می آید و از آن برای بالا بردن استحکام ماسه قالب یا ماهیچه و رنگهای پوششی استفاده می کنند.
مطلب مرتبط:برشکاری و تمیزکاری در ریخته گری
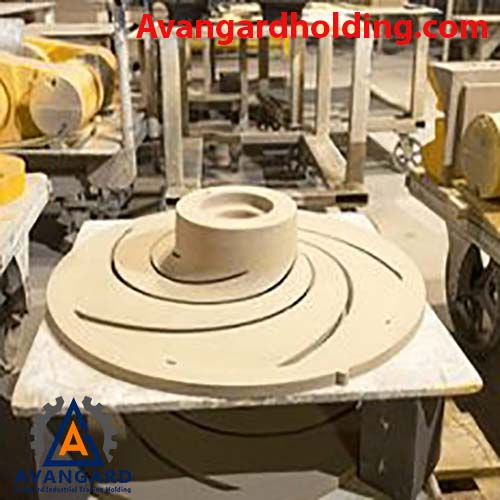
از روش های پر مصرف ساخت ماسه جهت قالبگیری ریخته گری، استفاده از چسب سیلیکاتی و گاز کربنیک یا دی اکسید کربن (CO2) در مخلوط ماسه است. جهت این روش برای سخت شدن ذرات ماسه، در آن از چسب سیلیکات سدیم و گاز CO2 استفاده می شود، که در صنعت ریخته گری به ماسه CO2 نیز معروف است. این روش از روش های پر استفاده در صنعت ریخته گری ایران برای ساخت قالب ریختگری و ماهیچه گیری است. روش کار اینگونه است که در مرحله ی آماده سازی مخلوط ماسه برای قالب گیری، چسب سیلیکات سدیم به مقدار معینی به ماسه اضافه می شود و توسط میکسر کاملا میکس می شود و سرانجام ماسه ترکیب شده با چسب به داخل قالب منتقل می شود و فرایند کوبش ماسه انجام می گردد.
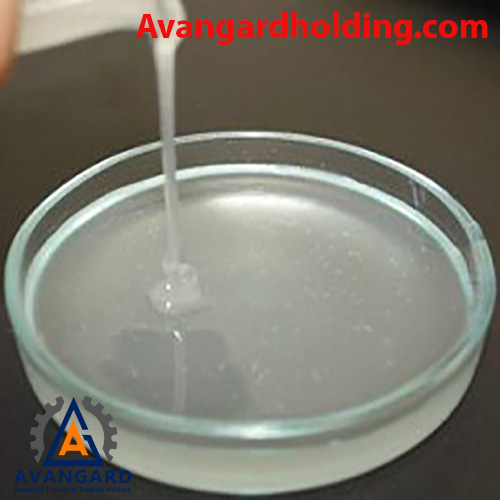
استفاده از چسب سيليكات سديم به عنوان چسب مورد استفاده در صنعت ريخته گری به حدود سال 1930 ميلادی باز مي گردد. در سال 1960 ميلادی، استفاده از گاز CO2 مرسوم گرديد. ابداع اين روش، انقلابی در صنعت ريخته گری بوجود آورد. از اين روش ميتوان جهت ريخته گری قطعات چدنی، فولادی و همچنين ريخته گری قطعات فلزات غير آهنی استفاده کرد.
چسب سیلیکات سدیم به مقدار 3 تا 5 درصد وزنی ماسه سیلیسی به مخلوط اضافه می شود. مقدار افزودن چسب سیلیکات سدیم به عواملی چون اندازه ماسه، نوع، شکل، نوع آلیاژ ریختگی، استحکام، دمای ذوب ریزی و خرد شوندگی قالب یا ماهیچه و مقاومت مورد نیاز قالب به ساییدگی و شکستگی دارد. هر چه دانه بندی ماسه ریزتر باشد مقدار مصرف چسب افزایش می یابد. پس از اضافه شدن چسب به ماسه، آن ها را تا هنگامی مخلوط می کنند که چسب کاملاً به صورت همگن در داخل ماسه توزیع شود و به صورت گلوله باقی نماند. استفاده از چسب زیاد موجب مصرف زیاد گاز کربنیک و کاهش استحکام قالب به ویژه با گذشت زمان، پوک و پودر شدن مخلوط ماسه می شود.
آنالیز چسب سیلیکات سدیم
brand | Ratio | Na20% | SiO2% | Solid content,% | Density,250cba | Specific | Viscosity(Cps) | Grade | Appearance | addition |
A.I.T.H 25 | 2.5 | 13.52 | 32.85 | 46.37 | 52 | 1.551 | 886 | ceramic | hazy | 2 % malas |
ترکیب شدن و آماده کردن ماسه و چسب سیلیکات سدیم در هم زن های مداوم یا تکباری (غیر مداوم) انجام می گیرد. در نوع تکباری، مقدار معینی چسب و ماسه در مخلوط کن ریخته می شود و عمل مخلوط شدن انجام و ماسه آماده استفاده قرار می گیرد. در هم زن مداوم، دستگاه به طور پیوسته کار می کند. چسب و ماسه از مخازن جداگانه ای از یک طرف وارد محفظه می شود و پس از مخلوط شدن از طرف دیگر خارج می شود.
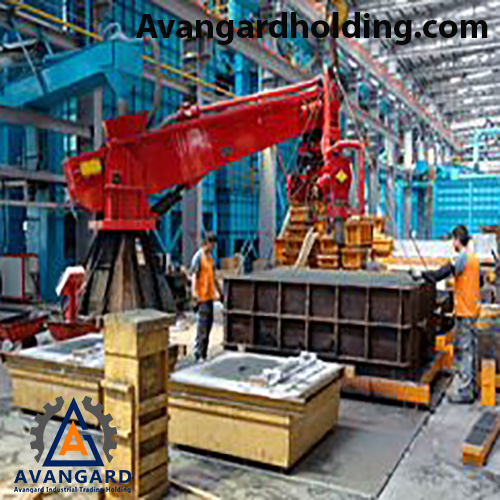
پس از آماده شدن ماسه، ساخت قالب ریخته گری یا ماهیچه گیری با این مخلوط ماسه و چسب انجام می شود و سپس بایستی در سریعترین زمان ماسه مصرف شود و به طور معمول گاز CO2 با فشار حدود 3-1 بار به مدت 5 الی 60 ثانیه به درون ماسه تزریق می شود. برای اینکه گاز به تمام قسمت های قالب نفوذ کند قالب با سیخ زدن، سوراخ شده و نازل شلنگ گاز در آن سوراخ فرو برده می شود تا گازدهی کاملا صورت بگیرد. با دمش گاز CO2 به قالب، بلافاصله واکنشی بین گاز کربنیک و سیلیکات سدیم انجام می گیرد. در اثر این واکنش، سیلیس به صورت سیلیکا ژل (سیلیس ژلاتینی) دانه های ماسه را به یکدیگر پیوند می دهد.
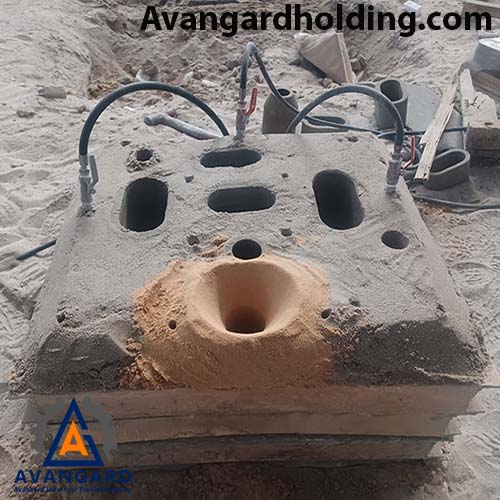
استحکام اولیه ماهیچه و قالب های گاز داده شده به مدت 5 ثانیه 310-255 کیلو پاسکال است. ولی استحکام با گذشت زمان و پس از 24 ساعت به 1380-670 کیلو پاسکال می رسد. علت افزایش استحکام بعد از گذشت زمان، دهیدراته شدن سیلیکات واکنش نداده و ادامه ی فرآیند ژل شدن سیلیس است. گاز کربنیک در داخل ماسه می تواند منطقه ای به شعاع 70 میلیمتر در اطراف سوراخ دمش را سخت کند. به همین دلیل بهتر است فاصله بین دو سوراخ گازدهی در قالب ماسه ای حداکثر 140 میلیمتر در نظر گرفته شود.
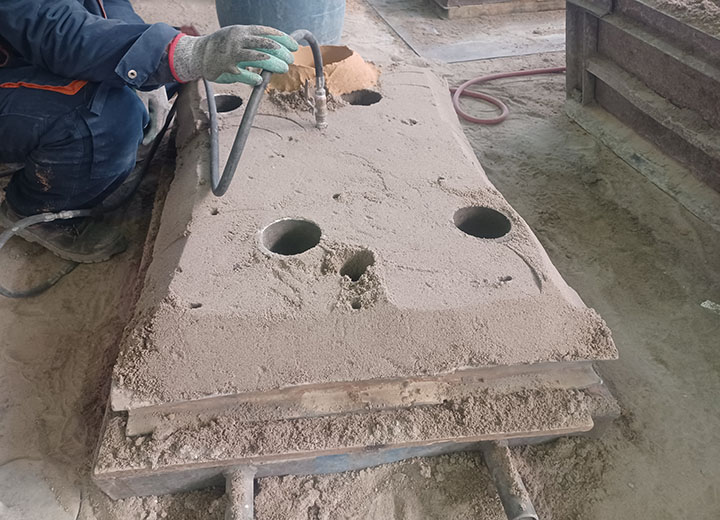
ابتدا نصف مدل در درجه پایین قرار داده می شود، سپس روی مدل با ماسه پر می شود و با ابزار های مخصوص فشرده می شود تا شکل مدل را به خود بگیرد.
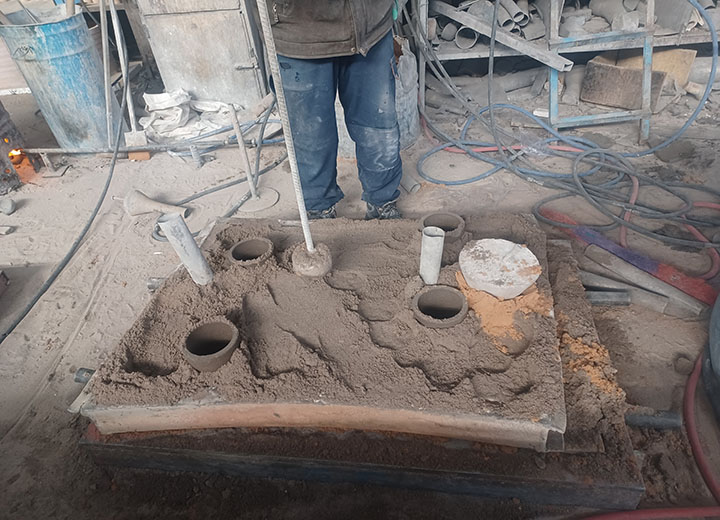
بعد از دمش گاز برای استحکام گرفتن قالب، درجه پایین برگردانده می شود و درجه بالا روی آن قرار می گیرد. نصف دیگر مدل بر روی آن مونتاژ شده و بعد از قرار دادن تغذیه و سیستم راهگاهی، درجه بالا نیز با ماسه پرشده و فشرده می شود و دمش گاز تکرار می شود. سرانجام دو درجه از هم جدا شده و مدلهای چوبی یا فلزی و مدل های راهگاه و تغذیه از ماسه خارج می شوند. مسیر راهگاه های ذوب نیز با ابزارهای خاصی پرداخت و سپس سطح آنها صاف می گردد.
محصول مرتبط: محصولات ریخته گری
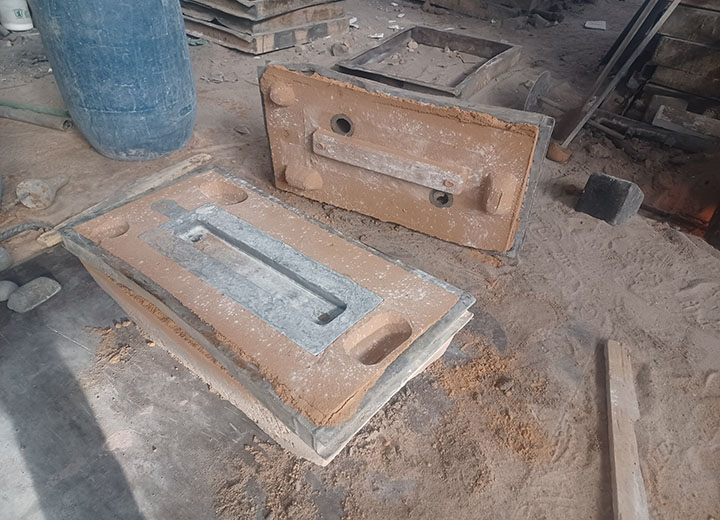
سپس سطح قالب با استفاده از پوشان های دیرگداز به دلایل ذیل با ضخامت مناسب پوشش داده می شود:
زمانی که فلز مذاب با دمای بالا داخل قالب ماسه ای ذوب ریزی می شود، واکنش های مخربی بین مذاب و ماسه یا چسب ایجاد می شود که در سطح قطعه عیوبی از جمله ماسه سوزی، زبری و ناهمواری بوجود می آورد که در بسیاری از موارد قطعه را غیر قابل استفاده می کند. عیوبی مانند ماسه سوزی، کندگی و شستن ماسه و فعل و انفعالات شیمیایی بین فلز مذاب و ماسه از این دسته هستند. حال اگر از پوشانی مناسب برای پوشش سطح ماسه ای که در تماس با فلز مذاب است استفاده کنیم می توانیم تا حد زیادی چنین عیوبی را حذف کنیم.
پوشان نسوز یک نوع رنگ مخصوص برای استفاده در صنعت ریخته گری ماسه ای است. تفاوت آنها با رنگ های معمولی در این است که بگونه ای طراحی شده اند تا در برابر دمای بالای فلز مذاب مقاومت کرده و بصورت یک مانع در مقابل فلز ذوب شده و قالب ماسه ای و یا سطح ماهیچه قرار گیرند. از روشهای متداول پاشش پوشان بر روی قالب با استفاده از پیستوله یا فرچه می باشد.
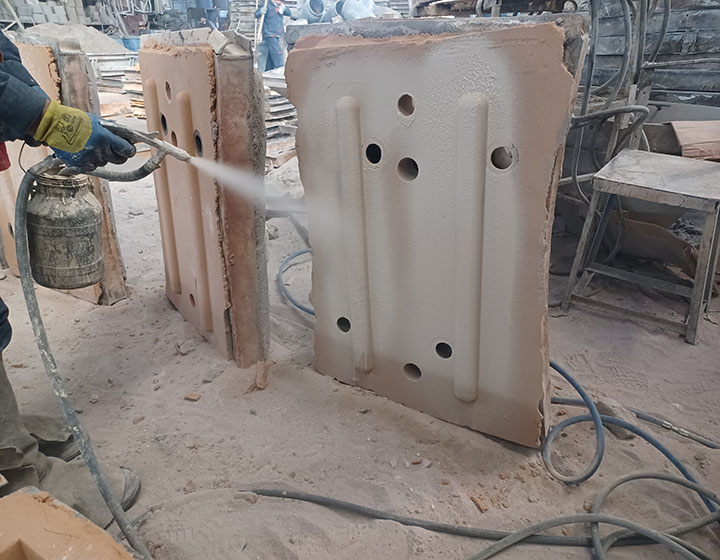
بعد از خشک شدن کامل قالب و پوشان، ماهیچه در درون قالب قرار داده می شود
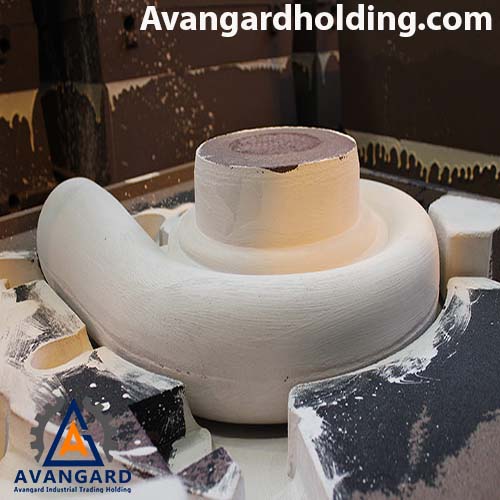
در پایان قالب مونتاژ شده و آماده ذوب ریزی می شود.
مطلب مرتبط: عملیات حرارتی در ریخته گری
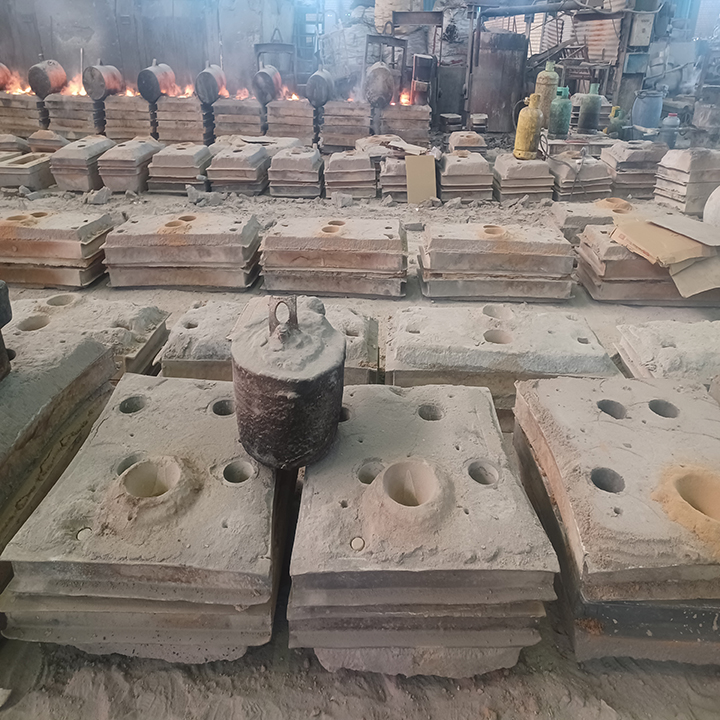