- صفحه اصلی
- خدمات ریخته گری
- ذوب ریزی در ریخته گری
هلدینگ آوانگارد مفتخر است با تکیه بر بیش از دو دهه تجربه و تحصیلات بالای علمی از دانشگاه های معتبر داخل و خارج از کشور و همچنین تولید بیش از ده هزار قطعه اعم از قطعات صنایع ماشین سازی-خودرو سازی-قالب سازی-نفت و گاز و پتروشیمی-صنایع نیروگاهی- صنایع سیمان و فراوری مواد معدنی باآلیاژهایی نظیر گروههای فولادهای كربنی، كم آلیاژی، مقاوم به حرارت(استیل و نسوز)، منگنزی (هادفیلد)، پركروم و نیز چدنهای پركروم(های کروم)، و همچنین قادر به تولید قطعات ، براساس آنالیز خاص، استانداردها و ویژگیهای مورد نظر، در خدمت شما صنعتگران محترم می باشدکه با بهترین و بالاترین کیفیت و مناسب ترین قیمت، خدمات ریخته گری خود را تقدیم شما عزیزان نماید.
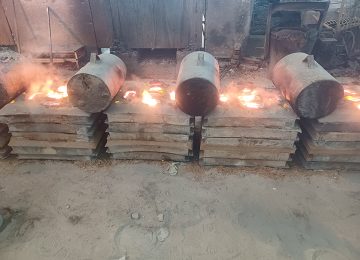
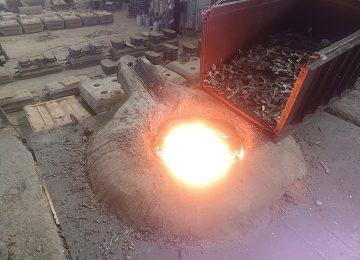
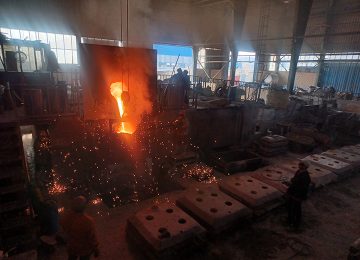
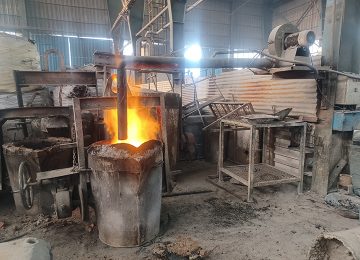
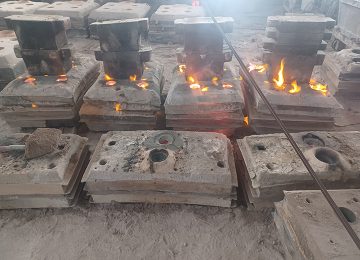
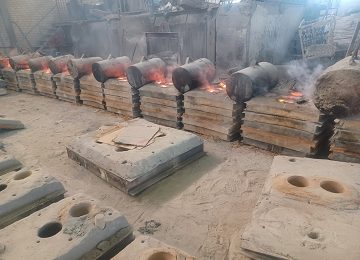
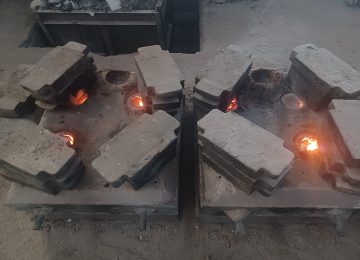
ریختهگری قدمتی 7 هزار ساله دارد. قدیمی ترین قطعه ریختهگری جهان یک قورباغه مسی متعلق به 3200 سال قبل از میلاد مسیح است که در بینالنهرین پیدا شدهاست. روشهای مختلفی برای تولید قطعات فلزی از جنس آهن، فولاد و فلزات غیر آهنی (برنز، آلومینیوم، برنج و غیره) وجود دارد. مهمترین روش، روش ریختهگری است. ریختهگری مکانیزمی است که طی آن فلزها و آلیاژها به حالت ذوب شده، درون قالب ریخته می شوند، و بعد از سرد شدن و انجماد کامل ظاهر قالب را به خود می گیرند. عملیات ریخته گری برای شکل دادن به مذاب و تولید قطعات پیچیده انجام می شود.
همانطور که بیان شد، ریخته گری شامل شکلدهی به یک آلیاژ از طریق ذوب و انجماد آن است. این روش ساده اما کاربردی، زیر بنای صنایع بزرگ فولادی در دنیا می باشد. اگرچه که روشهای دیگری نیز برای شکلدهی به انواع فولاد و چدن وجود دارند، اما ریخته گری دارای مزایای زیادی نسبت به سایر روشها است .
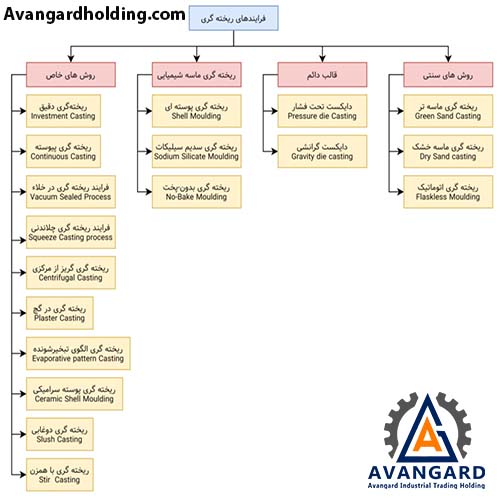
صنعت ریختهگری فلزات، مکانیزم مهم تولیدی است که محصولات ریختگری متفاوتی را برای زندگی انسان ها تولید میکند. با توسعه اقتصاد جهانی، صنعت ریختهگری فلزات، طی سالهای اخیر بهسرعت در حال رشد است. ظرفیت تولید فلزات ریختگری در دنیا از مقدار 92 میلیون تن در سال 2010 به 112 میلیون تن در سال 2016 افزایش پیدا کرده است. صنعت ریختگری فلزات، قطعات با اشکال پیچیده را که در کالاهای مصرفی و صنعتی متعددی استفاده می شود، تولید میکند.
شرکت آوانگارد با برخورداری از کادر مجرب مهندسی و تجربه بالای تولید انواع قطعات فولاد وچدن، قادر به تولید انواع قطعات با شکل های هندسی پیچیده وآلیاژهایی مطابق با درخواست شما عزیزان خواهد بود. در ادامه در خصوص آلیاژهای تولیدی در عملیات ذوب و ریخته گری بیشتر صحبت خواهیم داشت.
مطلب مرتبط: برشکاری و تمیزکاری در ریخته گری
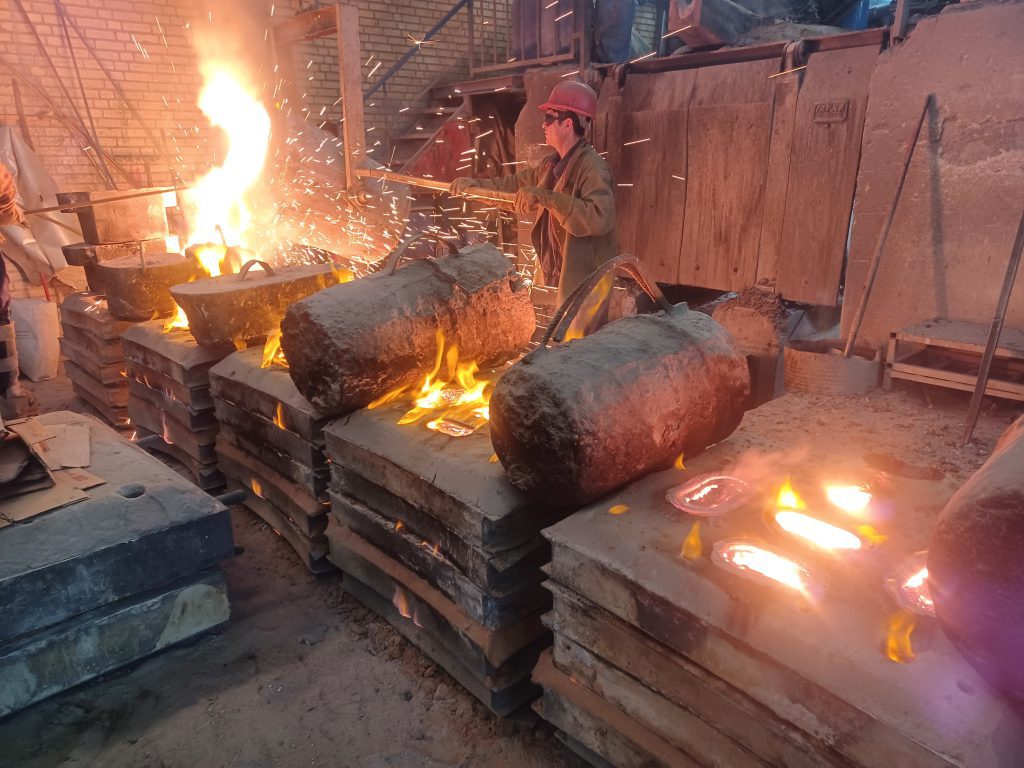
پس از مراحل قالبگیری و مونتاژ که در مراحل قبلی در سایت هولدینگ آوانگارد به اختصار در مورد آن صحبت داشته ایم، وارد مرحله ذوب ریزی می شویم.
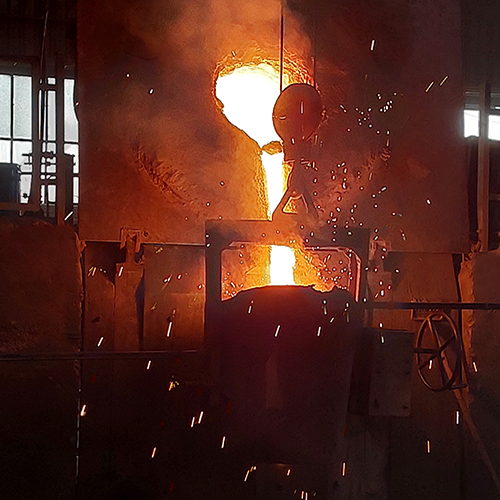
برای ساخت بسیاری از قطعات فلزی، مکانیزم تولید از ذوب کردن فلزات آغاز میشود. در این حالت لازم است دمای فلز تا نقطه ذوب بالا رود و برای عملیات متالورژیک، اغلب لازم است در دمای مورد نظر نگهداری شود. استفاده از کوره القائی، یکی از بهترین روشها برای انجام این پردازش است و پس از آلیاژ سازی دقیق، کوره دار طبق محاسبه شارژ انجام شده، اقدام به عملیات ذوب داخل کوره نموده و پس از آماده سازی ذوب، یک نمونه جهت آنالیز ذوب با دستگاه کوانتومتر تهیه و به واحد آزمایشگاه ارسال می نماید.
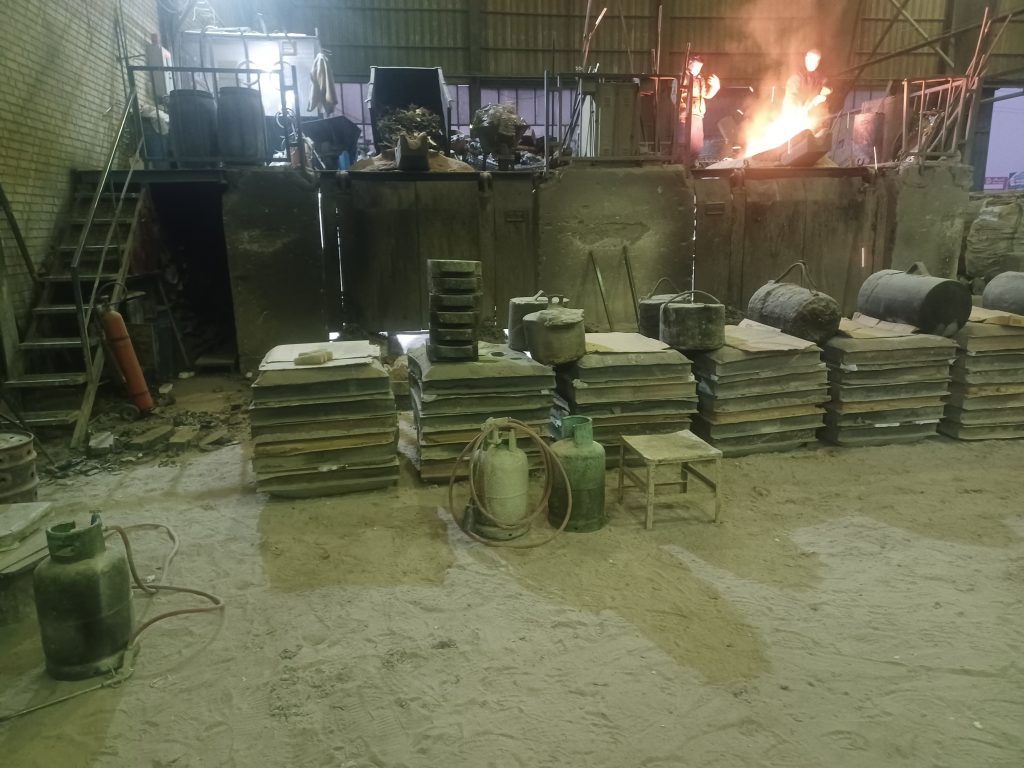
اندازه گیری عناصر مختلف در مذاب و کنترل دقیق آنالیز شیمیایی بوسیله کوانتومتر توسط مهندسین با تجربه در آزمایشگاه هلدینگ آوانگارد انجام می گیرد. بدین روش که ابتدا سطح قطعه، مورد سنگ زنی قرار گرفته به طوری که سطح آن کاملاً صاف شده و عاری از هر گونه آلودگی و چربی باشد و نمونه از قسمت پرداخت شده بر روی محل اسپارک دستگاه قرار داده می شود. مکانیزم این آزمایش بر پایه نشر نوری است. ذرات تشکیل دهنده فلز مورد نظر در اثر اسپارک به صورت اتم و یون تجزیه شده که این یون ها تحریک شده و تابش می کنند. این نور تابش شده از طریق یک فیبر نوری از درون یک طیف سنج نوری عبور داده می شود. سپس با توجه به محدوده طول موج نشر نور هر عنصر، دقیق ترین خط نشری برای اندازه گیری غلظت آن عنصر در نمونه انتخاب می شود.
شدت نشر برای هر عنصر متناسب با غلظت عنصر مدنظر در نمونه بوده و با استفاده از نمونه های استاندارد موجود و منحنی های کالیبراسیون می توان بطور مستقیم درصد عناصر را در نمونه محاسبه نمود.
پس از اسپارک که به اصطلاح همان جرقه ای است که الکترود دستگاه بر روی سطح قطعه ایجاد می کند، توسط طول موج های که از قبل برای دستگاه تعریف شده است توسط کادر مجرب آزمایشگاه آوانگارد به میزان عناصرموجود در قطعه پی برده می شود وپس از تایید آلیاژ، اجازه تخلیه مذاب به داخل قالب از سوی واحد آزمایشگاه صادر می گردد .
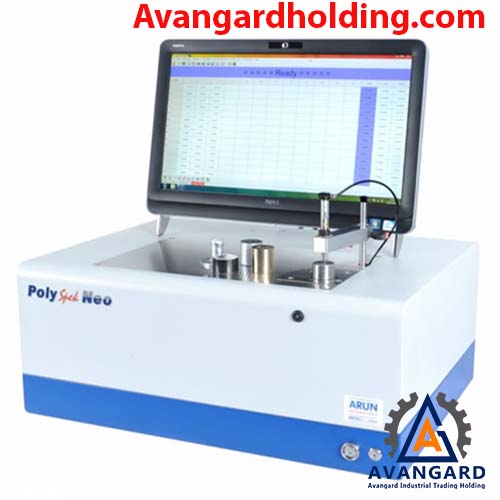
چرا به کوانتومتر نیاز داریم؟
همواره در ساخت قطعات، تعیین جنس، یكی از فاكتورهای مهم كارآیی قطعه است. جنس هر قطعه باید مناسب با شرایط كاری مانند، محیط كار قطعه، دمای كار قطعه، اتمسفركار قطعه، جنس سایر قطعات درگیر با قطعه و وظیفهای كه از قطعه انتظار میرود، باشد. به همین دلیل انتخاب صحیح جنس و اطمینان از آنالیز یك قطعه بسیار حائز اهمیت است كه برای تامین این هدف استفاده از كوانتومترهای دقیق با دقت صدم درصد ضروری است.
مطلب مرتبط: آزمایشگاه و کنترل کیفیت در ریخته گری
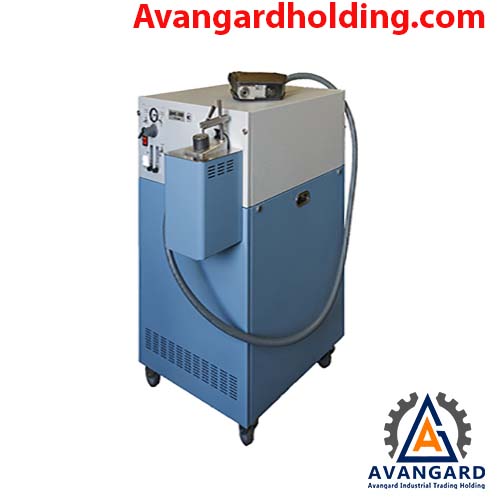
برخی از آلیاژ های پر مصرف در مجموعه آوانگارد
عنوان فولادهای كربنی، به فولادهای ساده كربنی، كه فاقد مقادیر قابل توجهی عناصر آلیاژی باشند، اطلاق می شود. این فولادها اساساً، در كارهای عمومی مهندسی، ساختمانی و تجهیزات تحت فشار هیدرولیكی، مورد استفاده قرار می گیرند. فولادهای كم آلیاژی، بدلیل وجود عناصر آلیاژی، مانند كروم، مولیبدن و نیكل، دارای خواص مكانیكی بالاتری در مقایسه با فولادهای ساده كربنی هستند. در فولادهای کربنی، بعلت عناصر آلیاژی مناسب در ترکیب، مقاومت به سایش و خوردگی، بهبود پیدا می کند.
با توجه به خاصیت مقاومت به چقرمگی و سایش مناسب فولادهای پركروم، از آنها، بطور عمده ای، در فرآیندهای خرد کن های مواد، کاربرد دارد. با در نظر گرفتن شرایط كاربردی آنها، این گروه از فولادهای مارتنزیتی، با ارائه مقاومت به سایش توام با استحكام عالی، توانسته اند در فاصله بین خواص فولادهای منگنزی و چدن های پركروم قرار گیرند. امروزه، چدنهای پركروم، در شرایطی كه قطعات تحت ضربات متوسط و سایش شدیدی قرار دارند، به عنوان یك جایگزین برای فولادهای پركروم، در نظر گرفته می شوند. این دسته از چدن های سفید، مقاومت به سایش بسیار خوبی دارند که علت آن وجود زمینه مارتنزیتی توام با كاربیدهای رسوبی است. در شرایطی كه قطعه تحت ضربات متوسط و سایش شدید می باشد، انتخاب چدنهای نیكل كرومی گزینه مناسبی می باشد
فولادهای مقاوم به حرارت، بطور وسیع برای كار در شرایط با دمای بالا بكار می روند. نوع محیط و استحكام مكانیكی در دمای بالا از شرایط اصلی انتخاب فولاد نسوز می باشند. فولادهای مقاوم به حرارت در مدت زمات طولانی سیكل كاری، مقاومت به خوردگی و استحكام مكانیكی خوبی را از خود نشان می دهند. فولادهای با تركیب آهن، كروم و نیكل، اساساً دارای زمینه آستنیتی بوده و در دمای بالا، از خود استحكام و چقرمگی خوبی را نشان می دهند. بعلاوه، آلیاژ نیكل – كروم در شرایطی كه قطعه، تحت تأثیر خاكستر ناشی از احتراق سوخت های سنگین است، دارای مقاومت قابل توجهی در برابر خوردگی بوده و در مقایسه با فولادهای نسوز، دارای مقاومت به خزش بالاتری هم می باشند.
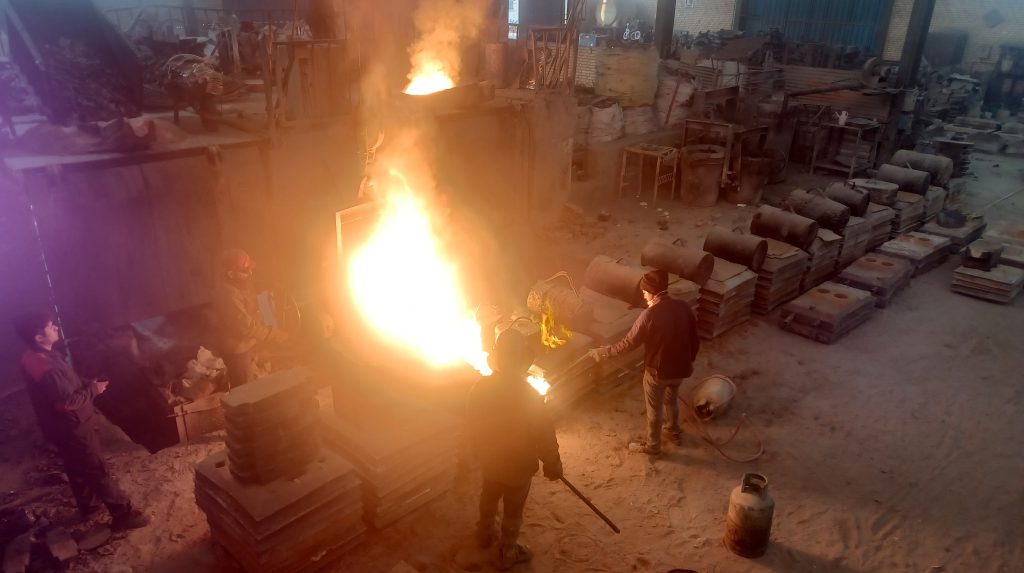
نقطه ذوب و نقطه جوش برای همه عناصر منحصر به فرد و مختص به خود آن فلز است. اگر دو فلز با هم ترکیب شده و تشکیل آلیاژ دهند، در این حالت نقطه ذوب و نقطه جوش آنها تغییر می کند. دانستن نقطه ذوب عناصر و آلیاژها به صنعتگران کمک میکند تا آنها را به صورت اصولی و استاندارد ذوب کنند که برای فلز یا آلیاژ مورد نظر مشکلی پیش نیاید. آهن و فولاد نیز دارای نقاط ذوب خاصی هستند و علاقمندان و فعالان این حوزه نه تنها نقطه ذوب آهن و فولاد، بلکه باید نقطه ذوب تمامی آلیاژهای مربوط به این دو فلز را نیز بدانند. در اینجا قصد داریم تا در مورد نقطه ذوب آهن و فولاد و آلیاژهای مختلف آن صحبت کنیم و آنها را مورد بررسی قرار دهیم.
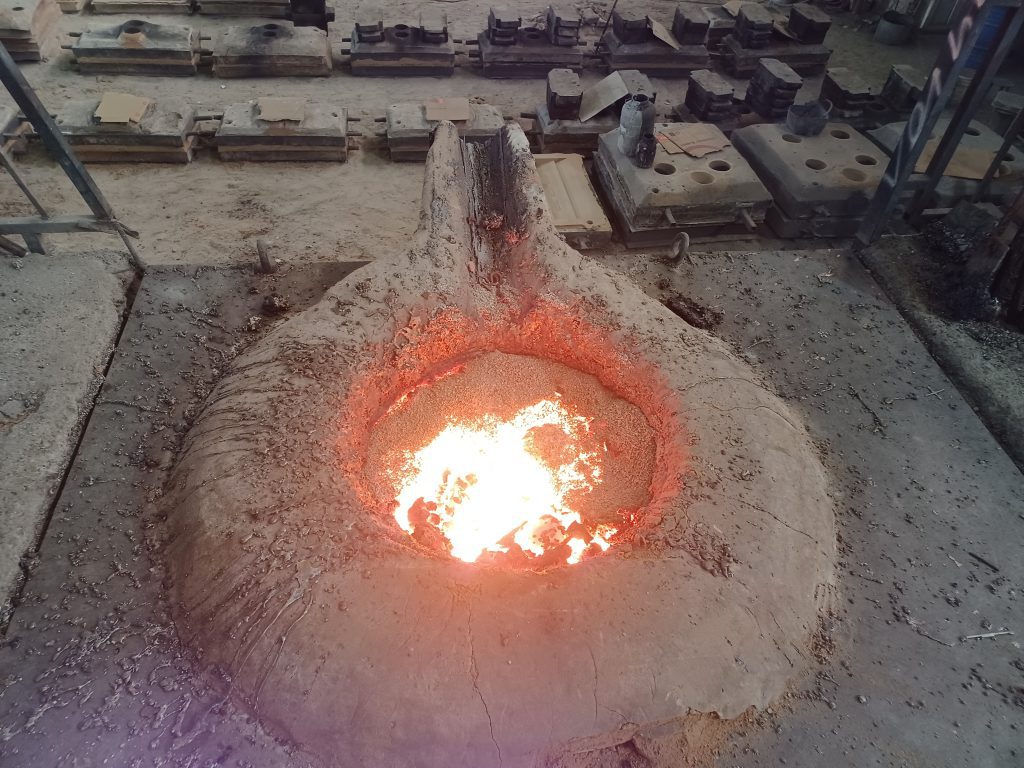
نقطه ذوب آهن
اتم های جامدات با نظم و آرایش خاصی در کنار یکدیگر قرار گرفتهاند. در حقیقت با گرما دادن به فلز و عنصر مورد نظر سبب ایجاد ارتعاش در آن خواهید شد. این دمای داده شده، اتم های عنصر را به حرکت درآورده و باعث میشود تا عناصر قابلیت چکش خواری و خم شدن پیدا کنند.
ذوب خمیری: با توجه به این که آلیاژها دیاگرامهای فازی مخصوص خود را دارند و از دمای ذوب تا انجماد آنها مطابق با دیاگرام خود مشخص است، با انتخاب دمای خمیری و حرارتدهی آهن، این ماده در حالتی که ترکیبی از جامد و مایع است قرار میگیرد.
نقطه ذوب آهن اسفنجی
آهن اسفنجی با حذف گاز اکسیژن داخل سنگ آهن توسط مواد احیایی و کربن بدست می آید و هنگام تبدیل آهن به فولاد، یکی از مراحلی که باید انجام شود تبدیل سنگ آهن به آهن اسفنجی می باشد. نقطه ذوب آهن اسفنجی در حدود پایین تر از 1200 درجه است. این نقطه ذوب پایین، به دلیل وجود حدود 30 الی 35 درصد ناخالصی موجود در آن است.
نقطه ذوب آهن خالص
آهنی که اغلب مورد استفاده قرار میگیرد، آهنی است که کمی ناخالصی به همراه خود دارد. آهن خالص نقطه ذوب متفاوتی نسبت به آهن ناخالص دارد. نقطه ذوب آهن وابسته به اندازه و ترکیب شیمیایی که دلیل ایجاد ناخالصی شده، میتواند متغیر باشد و از نقطه اصلی بیشتر یا کمتر شود. آهن به عنوان مادهای که از سنگ آهن بدست میآید، دارای نقطه ذوب مشخصی میباشد. نقطه ذوب آهن خالص به طور استاندارد 1538 درجه سانتی گراد است.
نقطه ذوب فولاد
فولاد، آلیاژی از آهن است. آهن خالص که پیش تر در خصوص آن صحبت کردیم، بسیار نرم و خورنده است و به دلیل اینکه با اکسیدها و سولفیدها در محیط واکنش نشان میدهد و به عبارتی در محیط فعال، نمی شود از آن استفاده کرد. یکی از نتیجه های اضافه کردن کربن به آهن، این است که سبب میشود تا واکنش پذیری پایینی پیدا کند و این عیب و مشکل آهن خالص را برطرف میکند. دمای ذوب فولاد چیزی در حدود 1425-1540درجه سانتیگراد است.
نقطه ذوب فولاد CK45
فولاد CK45 با توجه به ویژگی های خوب مکانیکی و فیزیکی آن از خواص مقاومت در برابر سایش و ضربه برخوردار است، اما متاسفانه به علت کم بودن مقدار کروم Ck45، این فولاد در مقابل زنگ زدگی و خوردگی مقاوم نیست. نقطهی ذوب این فولاد با توجه به مقدار و درصد غلظت مواد موجود در آن بستگی دارد. اما به صورت میانگین دمای ذوب این نوع از فولاد، بین -1560 1514 درجه سانتیگراد در نظر گرفته میشود.
نقطه ذوب فولاد زنگ نزن
فولاد زنگ نزن یا استنلس استیل به دلیل داشتن مقاومت بالا در برابر خوردگی، یکی از انواع فولاد است که در مهندسی مواد بسیار پر استفاده است. حضور تقریبا 12 درصد کروم در ترکیب عناصر فولاد زنگ نزن سبب ایجاد مقاومت بالای آن شده است. با تولید فولاد استنلس استیل و افزودن آن به آهن، از سطوح آهن در برابر اکسید شدن و خوردگی محافظت میشود. در برخی از انواع فولاد زنگ نزن، ترکیبات نیکل،مولیبدن،تنگستن،نیوبیوم،تیتانیوم،وانادیوم و آلومینیوم نیز وجود دارد که باعث ایجاد مقاومت به خوردگی بیشتر در آنها و در نتیجه زیادتر شدن قیمت تولید قطعات ریخته گری استنلس استیل میشود. فولاد زنگنزن شامل گریدهای مختلفی است و به دلیل اینکه آلیاژی محسوب میشود، در گریدهای مختلف نقطه ذوب متفاوتی دارند.
آلیاژهای مازاد نیز از محدوده ذوب عنصر عبور می کنند. آهن خالص (آهن) دارای نقطه ذوب ثابت 1538 درجه سانتی گراد ، کروم (Cr) 1860 درجه سانتیگراد و نیکل (Ni) 1453 درجه سانتیگراد، در مقایسه با طیف وسیعی از 1400-1530 درجه سانتیگراد برای فولاد ضد زنگ است.
- لازم بذکر است شرکت آوانگارد تجربه موفقی در تولید فولاد های زنگنزن یا فولاد ضدزنگ یا استنلس استیل، (Stainless Steel) در انواع ذیل را دارا می باشد:
- فولاد زنگنزن آستنیتی (Austenitic Stainless Steel) ( سری 200 و سری 300)
- فولادهای زنگنزن آهنی فریتی (Ferritic stainless steel)
- فولاد زنگنزن مارتنزیتی (Martensitic Stainless Steel)
- فولاد زنگنزن دوپلکس (Steel Duplex)
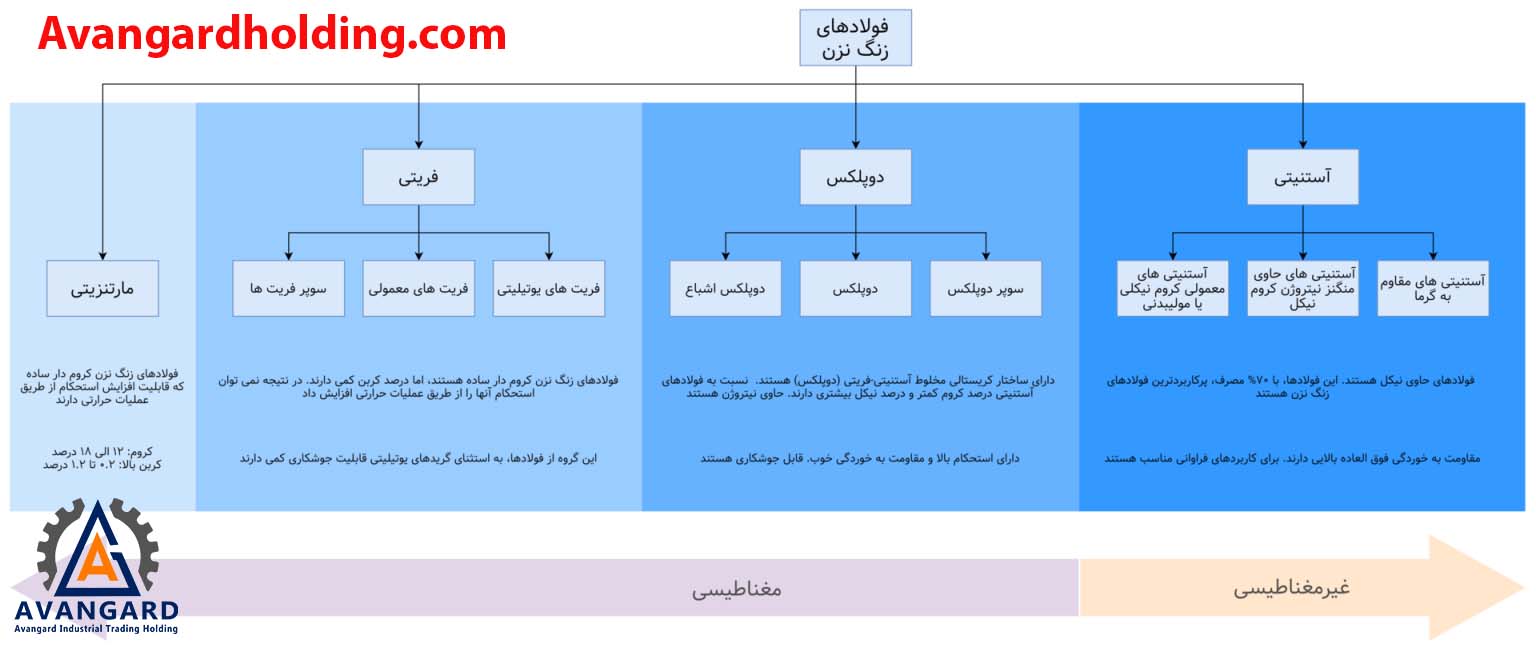
نقطه ذوب استیل 316
استیل به آلیاژی گفته میشود که پایهی آن عنصر آهن است و کمتر از 2% کربن دارد. استیل 316 حاوی ترکیباتی از نیکل، کروم و مولبیدن است. حضور مولبیدن در ترکیبات این ماده به دلیل بالا بردن مقاومت استیل در برابر خوردگی ناشی از کلراید است. درصورتیکه حرف L بعد از نام این استیل بیاید، به معنای مقدار کم کربن است که در آلیاژ آن مورد استفاده قرار گرفته و این مقدار کم عنصر کربن باعث میشود تا بعد از جوشکاری نیز لایهی محافظتی آن وجود داشته باشد. یکی از عمده روشهای تولید این نوع استیل 316، بازیافت ضایعات آن است و حدود 70 درصد استیلهای تولید شده، با ذوب ضایعات این استیل و قالبگیری دوباره آن شکل گرفتند. استیل 316 زیر مجموعه ای از فولاد های استیل زنگ نزن است و نقطه ذوب آن تقریبا برابر با فولاد زنگ نزن است. لازم بذکر است شرکت آوانگارد سابقه درخشانی در تولیدقطعات استیل316L را دارد.
چدن نیز مثل فولاد آلیاژی از ترکیب آهن و کربن است. اما با یک تفاوت عمده که درصد کربن موجود در چدن بالاتر از دو درصد و درصد کربن موجود در فولاد تا حدود 2.1 است. چدن در دسته آلیاژهای ریختهگری آورده میشود. در فولاد عناصر دیگری نیز مانند سیلیسیم، منگنز، نیکل و کروم نیز وجود دارند. ریختهگری چدن خیلی آسان است و نسبت به فولاد درصد انقباض کمتری دارد و همین خاصیت سبب شده است تا در سازههای آهنی زینتی و معماری، چدن نسبت به فولاد فلز ایدهآلتری باشد. چدن نسبت به فولاد در برابر خوردگی آسیبپذیری زیادتری از خود نشان میدهد و همچنین دارای چقرمگی پایین و خمش ناپذیرتر و خشکتر هست. هزینهی تولید فولاد از هزینه تولید چدن بیشتر است.
اما اگر قصد مقایسه نقطهی ذوب این دو ماده با یکدیگر را داشته باشیم، با توجه به اینکه هردوی آنها آلیاژی از آهن هستند ولی، چدن نسبت به فولاد، از نقطهی ذوب کمتری برخوردار است. نقطه ذوب چدن در حدود 950 الی 980 درجه سانتیگراد است.
ترکیبات شیمیایی و ساختار متالورژیکی دو دلیل بسیار مهم در نقطه ذوب فولاد هستند. شاید نقطه ذوب آهن عددی ثابت است، اما در بعضی مواقع یکی سری عمل هایی وجود دارد که میتواند این عدد را متغیر کرده و نقطه ذوب را بالاتر یا پایینتر ببرد. البته، مقدار اثر ترکیبات شیمیایی نسبت به ساختار متالورژیکی بیشتر است و ممکن است نقطه ذوب فولاد را تغییر دهد. با توجه به مطالب فوق میتوان نتیجه گرفت که با افزایش ناخالصیهای موجود در آهن، نقطه ذوب هم افزایش می یابد و هرچقدر درصد کربن داخل آن آلیاژ بیشتر باشد، نقطه ذوب آن آلیاژ از آهن هم کمتر است. این عامل بر قیمت قطعات ریخته گری به عنوان یک محصول فولادی موثر است.
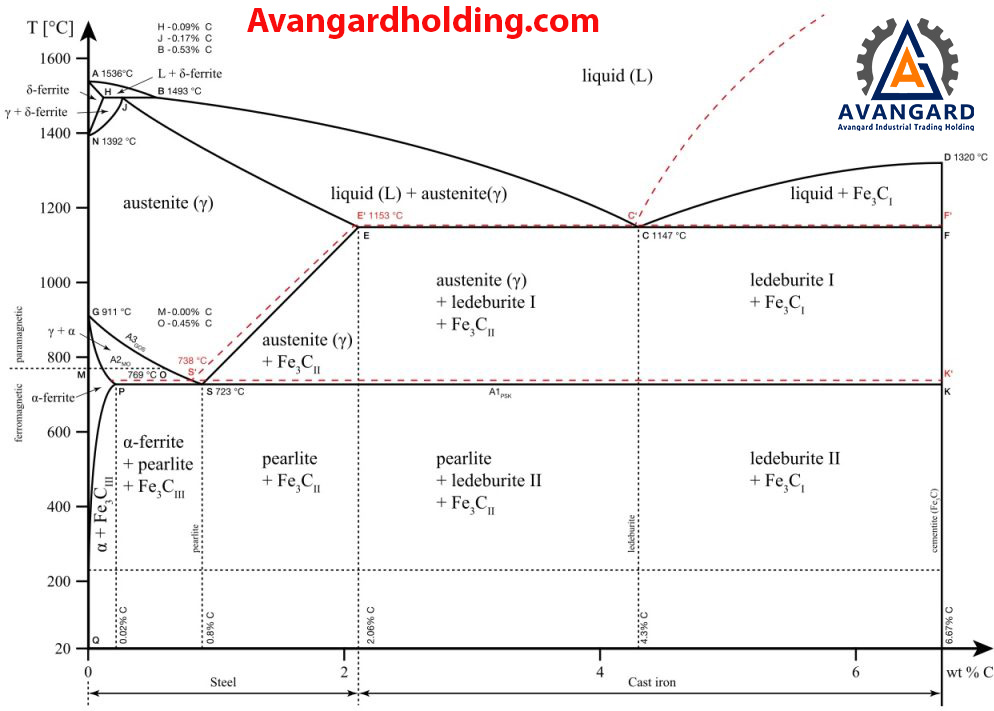
با پیشرفت تکنولوژی و توسعهی علم، نقطهی ذوب، بیش از پیش پر اهمیت شده و در صنعت بیشتر مورد استفاده قرار میگیرد.
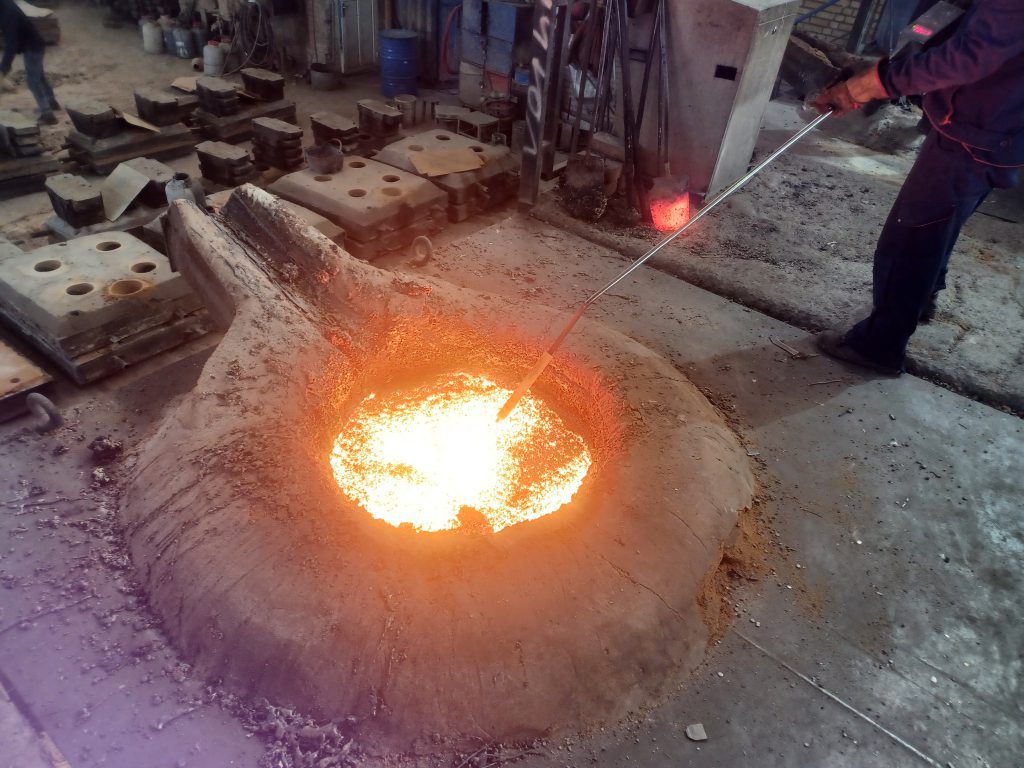
فهمیدن دمای ذوب فلز مذاب برای ریخته گر بسیار مهم و حیاتی است. ندانستن دمای مذاب آلیاژ مد نظر و بالا بردن بیش از حد دمای آن باعث بروز اشکالات زیادی از قبیل کاهش طول عمر مفید عایق کوره و پاتیل، اتلاف و سوختن بعضی از عناصر مفیدِ موجود در مذاب، تغییر فاز و ماهیت مذاب، سوختن و تغییر فرم قالب پس از ذوب ریزی، جذب گاز در برخی مواد و سایر موارد دیگر می شود. عکس این موضوع نیز یعنی ندانستن کم بودن دمای مذاب و ذوب ریزی ریخته گری باعث مشکلاتی همچون ماسیدن مذاب در پاتیل ذوب ریزی یا راه گاه قالب، نرسیدن مذاب به تمامی قسمتهای قالب، نرسیدن مذاب به خواص مورد نظر و غیره می شود.
بنابر این دانستن دمای صحیح مذاب برای ریخته گر یکی از دانسته های بسیار مهم در مورد مذاب می باشد. برای بعضی آلیاژها دانستن دقیق دمای ذوب همانند دانستن آنالیز شیمیایی عناصر آلیاژ مهم و حیاتی می باشد.
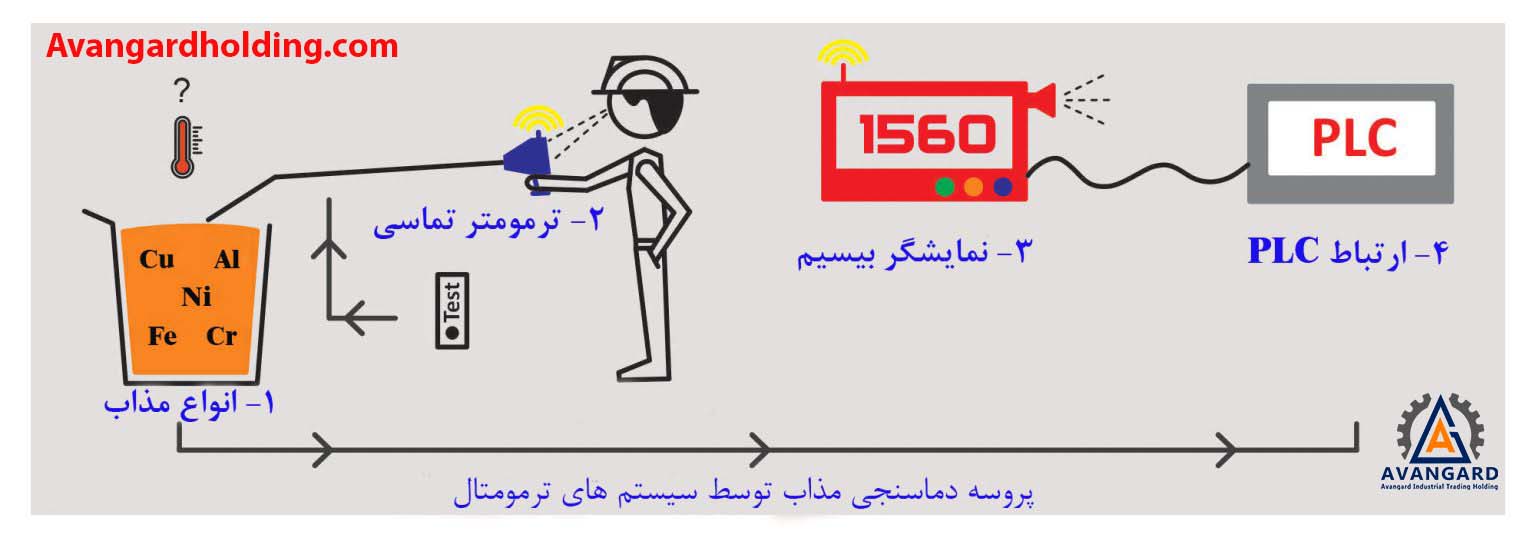
1-ریخته گری تخصصی انواع فولادها و چدن های ضد سایش نظیر فولادهای منگنزی ( هادفیلد ) با درصدهای مختلف منگنز و مولیبدن ، چدن نایهارد و چدن های، های کروم مورد استفاده به عنوان چکش، سندان و لاینر دستگاههای سنگ شکن شن وماسه وسیمان، با قیمت های مناسب و کیفیت بالا
*لازم به توضیح مجدد است که شرکت آوانگارد با کادر مجرب و مهندسی خود، تجربه تخصصی گسترده ای در تولید گروه وسیعی از آلیاژها را دارد. لیست کامل قطعات دستگاههای سنگ شکن در بخش محصولات آمده است و با بهترین قیمت و بالاترین کیفیت تقدیم شما عزیزان خواهد شد .
2- ریخته گری انواع فولادهای کربنی و کم آلیاژی از جمله آلیاژهای گروه GS… ، WCB ،42CrMo4 (Mo40) ، Gs – Ck45 ، فولادهای سختی سطحی شونده نظیر 1.7131 و سایر آلیاژهای ریختگی این گروه از فولادها
*کاربرد فولادهای فوق در صنایع ماشین سازی، صنایع ریلی و صنایع نفت و گاز می باشد .
3- ریخته گری انواع فولادهای ضد زنگ ( Stainless steel ) نظیر آلیاژهای 304 ، 316 ، 316L ، چدن نای رزیست و آلیاژهای خاص نظیر Duplex steel
*در این عرصه تجربه تولید قطعات مختلف ایمپلر و بدنه پمپ های آب ، نفت وگاز و حمل نمک یا اسید در این شرکت وجود دارد ، آلیاژهای دارای Ti ،Nb ، N ،V و W به کرات در این شرکت تولید و تحویل مشتریان گردیده است.
4-ریخته گری انواع فولادهای نسوز نظیر آلیاژهای 1.4841، 1.4848 ، 1.4837 ، 1.4823 و … مورد استفاده در محیط های با حرارت بالا در صنایع سیمان ، نفت و گاز و پتروشیمی
5- ریخته گری انواع چدن های خاکستری (GG) و نشکن ( GGG ) مطابق استاندارد های معتبر بین المللی نظیر DIN ، ASTM ، BS و غیرهتوضیح مجدد