- صفحه اصلی
- خدمات ریخته گری
- انجماد در ریخته گری
تیم مهندسی شرکت آوانگارد با تکیه بر بیش از دو دهه تجربه و تحصیلات بالای علمی از دانشگاه های معتبر داخل و خارج از کشور و همچنین تولید بیش از ده هزار قطعه اعم از قطعات صنایع ماشین سازی-خودرو سازی-قالب سازی-نفت و گاز و پتروشیمی-صنایع نیروگاهی- صنایع سیمان و فراوری مواد معدنی باآلیاژهایی نظیر گروههای فولادهای كربنی، كم آلیاژی، مقاوم به حرارت(استیل و نسوز)، منگنزی(هادفیلد)، پركروم و نیز چدنهای های كروم، و همچنین قادر به تولید قطعات، براساس آنالیز خاص، استانداردها و ویژگیهای مورد نظر شما مشتریان محترم با کمک از نرم افزار های بروز مهندسی و آزمایشگاه مجهز متالوگرافی و دیگر آزمایشات مکانیکی با تعریف شیب انجماد مناسب و دیگر فرایند مورد نیاز، قطعه مورد درخواست را طبق خواص و ساختار مدنظر به شما عزیزان با سرتیفیکت معتبر و بهترین کیفیت و نازل ترین قیمت تقدیم می نماید.
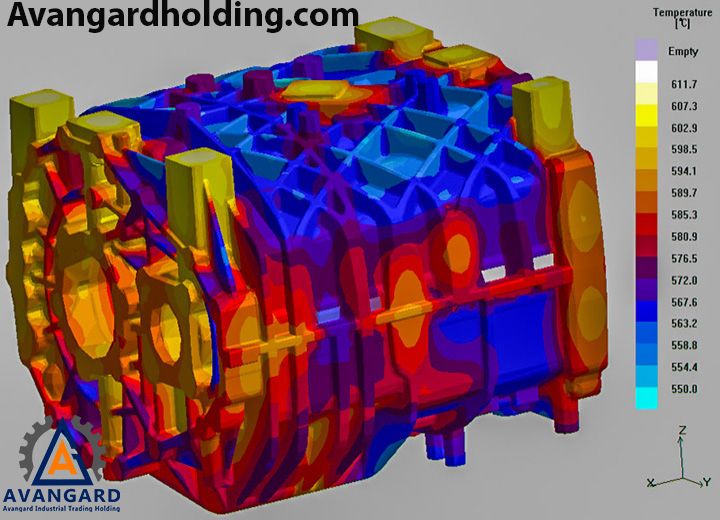
در واقع از زمانی که بشر توانمندی ذوب و استخراج فلزات را به دست آورد، پدیده انجماد جزیی از دانش و مهارت بشر در ساخت لوازم و تجهیزات مورد نیازش بوده است. انجماد یکی از روش های اقتصادی برای تولید بسیاری از فلزات محسوب می شود.
در دهه های اخیر با توسعه دانش بشری در شناخت مواد و تأثیر متغیرهای فرایندهای تولید بر ریزساختار و خواص مکانیکی، اهمیت انجماد در فلزات ریختگری بسیار بیشتر شده است. سرعت انجماد ذوب، ریزساختار نهایی قطعه را تعیین می کند و ریزساختار قطعه نیز خواص آن را تعیین می کند. به همین خاطر در بعضی از موارد برای تنظیم سرعت انجماد و همچنین انجماد یکنواخت در قطعه، در اطراف قالب هیترها و خنک کننده هایی نصب می کنند. باید به این نکته توجه داشت که سرعت سرد شدن در مکان های مختلف قطعه متفاوت است.
مطلب مرتبط: محصولات ریخته گری
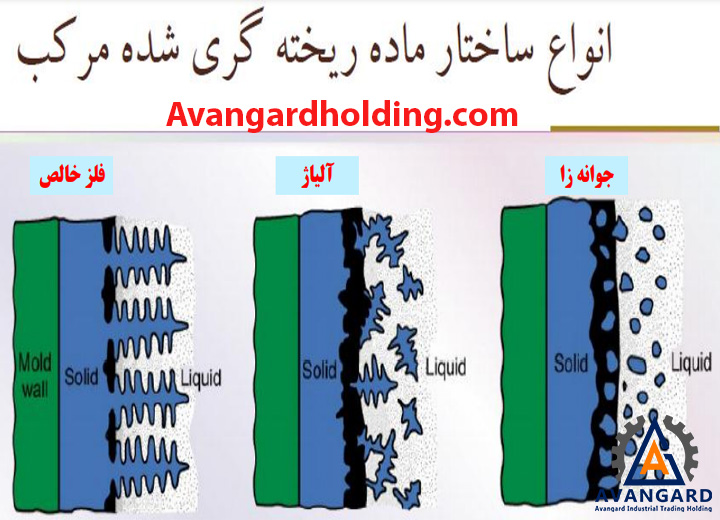
در حال حاضر برای تحلیل پدیده های انجماد در ریخته گری، از یک سو نگرشها و فنون متنوع متالورژیکی برای کنترل و بهبود ریزساختارهای انجمادی در حال توسعه است و از سوی دیگر، با استفاده از کامپیوترهای قوی جهت تحلیل های عددی و شبیه سازی های مهندسی، رفتارهای انتقال حرارت، جریان سیال و استحاله های فازی در انجماد برای قطعات و آلیاژهای مختلف مورد بررسی و ارزیابی قرار می گیرد.
انجماد با توجه به اینکه نوع ذوب فلزي کدامیک از موارد زیر است متفاوت است:
- یک عنصر خالص
- یک آلیاژ
- انجماد فلزات خالص
به خاطر انتقال حرارت بالا در دیواره قالب، بلافاصله بعد از ریختن مذاب پوسته نازکی از فلز منجمد در فصل مشترك دیواره قالب و مذاب شکل می گیرد. در این پوسته، به خاطر سرعت بالاي سرد شدن، ریزساختار بصورت دانه هاي ریز و تصادفی است. همانطور که انجماد پیش می رود دانه ها در جهت انتقال حرارت کشیده می شوند.
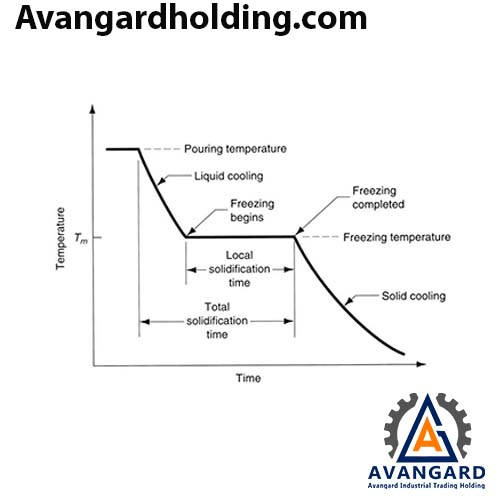
بیشتر آلیاژها به جاي اینکه در یک نقطه منجمد شوند در دامنه اي از دما منجمد می شوند. انجماد از دماي مذاب شروع شده و تا دماي انجماد، منجمد می شود. مانند فلزات خالص، بلافاصله پس از ریختن مذاب پوسته نازکی از فلز منجمد شده در فصل مشترك مذاب و دیواره قالب تشکیل می شود.
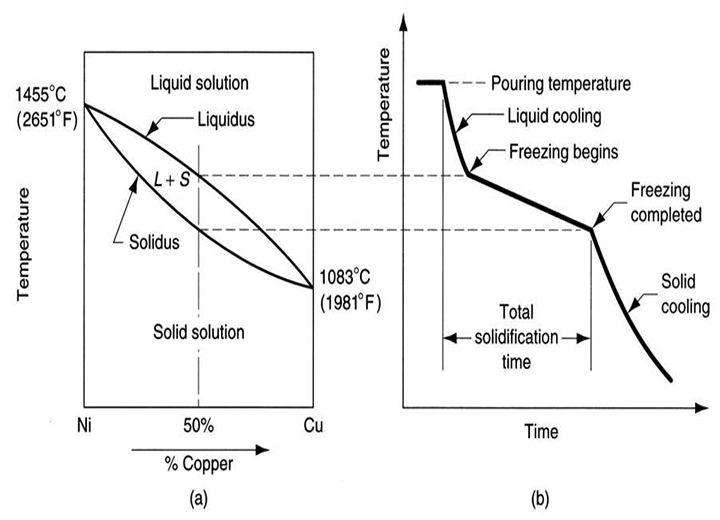
دندریتها کم کم شکل می گیرند. اما با توجه به دامنه وسیع دمایی بین خط انجماد و خط مذاب، بخشی از مذاب زودتر منجمد شده که نسبت به بخشی که دیرتر سرد می شود دانه هایش بیشتر در جهت انتقال حرارت رشد می کند. در نتیجه مذاب فلزي در مرکز قطعه دیرتر سرد شده و درنتیجه ساختار ریزدانه تر است.
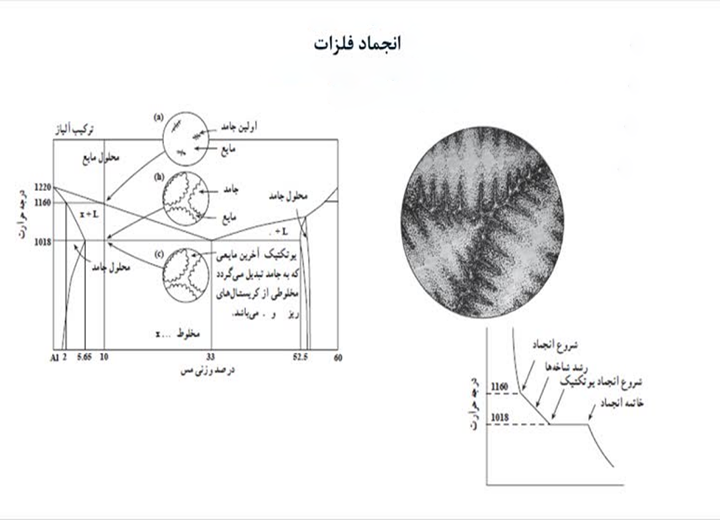
انقباض در سه مرحله اتفاق می افتد:
- در حین سرد شدن فلز در حالت مذاب
- درحین سرد شدن از حالت مایع به جامد
- هنگام سرد شدن جامد فلزي تا دماي محیط
اثر سرعت انجماد فلز مذاب در ريخته گرى انجمادی از جهات مختلفى مانند تأثير در توليد قطعه، ساختار فلز، خواص مكانيكى و … مهم است. به طورى كه افزايش سرعت انجماد سبب مى شود كه مذاب فلز درون قالب، در زمان كوتاه ترى منجمد شود و در يك فاصله زمانى مشخص تعداد قطعه بيشترى توليد گردد. بنابراين، اگر بتوان سرعت انجماد فلز مذاب در قالب را به گونه اى افزايش داد كه در خواص قطعه تغيير نامطلوبى ايجاد نشود، مى توان تعداد قطع توليدى را افزايش داد و از لحاظ اقتصادى با هزينه كمترى، تعداد قطعه بيشترى را توليد نمود. از طرف ديگر، سرعت انجماد مى تواند خواص و ساختار ميكروسكوپى قطعه را تغيير دهد؛ به گونه اى كه اگر سرعت انجماد يا به عبارت ديگر، سرعت سرد شدن مذاب افزايش يابد، تعداد بسيار زيادى جوانه جامد (هسته جامد) در مذاب به وجود مى آيد كه با ادامه رشد آن ها، يك ساختار ميكروسكوپى با دانه هاى ريز تشكيل مى شود. اين ساختار، داراى خواص مكانيكى نسبتاً خوبى مى باشد. در چنين ساختارى، به علت ريز بودن دانه ها، تعداد مرز دانه ها افزايش مى يابد؛ درنتيجه، براى تغيير شكل ساختار دانه ريز، نياز به نيرو و تنش بيشترى خواهد بود بنابراين، قطعه استحكام بيشترى از خود نشان خواهد داد. از طرفی ریز دانه بودن ساختار سبب افزایش چقرمگی و انعطاف پذیری شده و فلز مقاومت خوبی در برابر نیروهای مکانیکی از خود نشان می دهد.
مطلب مرتبط: طراحی و مدلسازی در ریخته گری
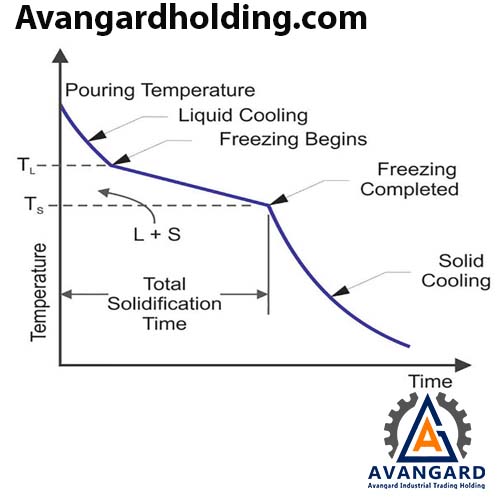
اگر سرعت تحت تبرید انجماد، يا سرعت سرد شدن مذاب کاهش پیدا کند، تعداد جوانه های (هسته هاى) جامد به حداقل خواهد رسید؛ که در این حالت رشد جوانه ها ادامه داشته و به ساختاری درشت دانه خواهيم رسيد. در قطعات با ساختار ميكروسكوپى با دانه هاى درشت، با توجه به كم بودن مقدار مرز دانه ها، استحكام نسبت به قطعات با ساختار دانه ريز كمتر است، اما در دماهاى بالا قطعه با ساختار دانه درشت مقاومت بهترى در برابر اعمال نيرو نسبت به قطعه با ساختار دانه ريز، خواهد داشت.
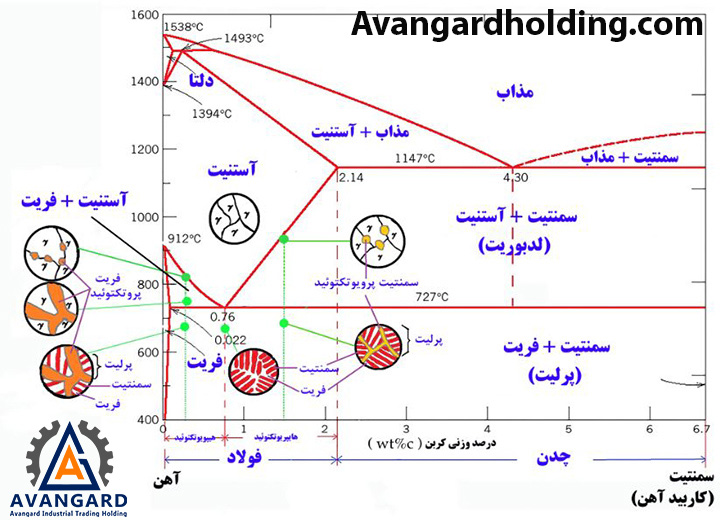
سرعت انجماد ذوب به ظرفيت حرارتى و هدایت حرارتى فلز مذاب و جنس ماده قالب بستگى دارد. به مقداری که هدايت حرارتى و ظرفيت حرارتى فلز مذاب و ماده تشکیل دهنده قالب بالاتر باشد، گرماى مذاب زودتر به خارج منتقل شده و مذاب خیلی سریع منجمد مى شود. به عنوان مثال، مذاب در قالب هاى فلزى و گرافيتى نسبت به مذاب در قالب ماسه اى سريع تر سرد شده و درنتيجه، سريع تر منجمد مى شود.
بهترين نوع انجماد قطعه ريخته گرى، انجماد جهت دار در ریخته گری يا كنترل شده است كه در آن انجماد مذاب از دورترين قسمت هاى قالب نسبت به تغذيه شروع شده و آخرين مرحله انجماد در تغذيه انجام مى شود. و راهی دیگر برای جهت دار کردن انجماد استفاده از مبرد CHILL که عموما از موادی نظیر مس، فولاد، گرافیت و آلومینیوم انتخاب میشوند و معمولا در داخل محفظه قالب و یا در دیواره آن به کار رود که در این حال مبرد داخلی internal chill و یا مبرد خارجی external chill نامیده میشوند و گاهی اوقات در برخی قسمتهای قالب استفاده از ماسه هایی نظیر ماسه کرومیت در حین قالبگیری پیشنهاد می شود که قابلیت تبریدی بالایی دارند. مبردها با تشکیل یک شیب دمایی بالاتر، جبهه انجماد را جهت داده و از این رو به ویژه در آلیاژهای با انجماد خمیری برد تغذیه را افزایش میدهند، علاوه بر آن در تمام آلیاژها نیز میتوان با استفاده از مبرد و یا لایهبندی (عایق بندی قسمتی از قالب) جهت انجماد را تنظیم نمود.در اين حالت، حفرات و مك هاى انقباضى در تغذيه تشكيل مى شوند. از طرف ديگر، گازها و ناخالصى هاى موجود در مذاب توسط جبهه انجماد به سمت تغذيه حركت كرده و از قطعه رانده مى شوند پس از انجماد، با جدا كردن تغذيه، به قطعه با كيفيت مناسب خواهيم رسيد.
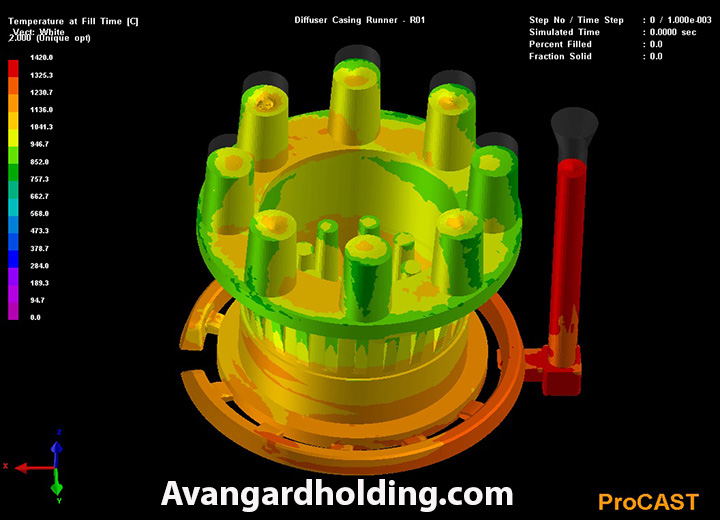
منطقه تبریدی Chill Zone :
دارای دانه های بسیار ریز در اثر برخورد مذاب با سطح قالب می باشد.
منطقه رشد ستونی:
در این منطقه دانه ها بصورت ستونی بوجود آمده و جهت گیری دانه ها همیشه در راستای کریستالی آنها و همچنین خلاف جهت انتقال حرارت می باشد. به طوری که ستون هایی که همراستایی بیشتری با جهت انتقال حرارت دارند به صورت رقابتی حرکت کرده و جلوی رشد سلول های مجاور خود را می گیرند. در صورتی که دمای بارریزی افزایش یابد، به دلیل بالا رفتن گرادیان حرارتی احتمال افزایش طول ستون ها بالا می رود. در صورتی که دمای بار ریزی کم شود، طول ستون ها به دلیل کاهش گرادیان، کم می شود.
منطقه محوری:
به دلیل کاهش درجه حرارت و افزایش غلظت، میزان تحت تبرید ترکیبی در مرکز قطعه افزایش پیدا کرده و جوانه زنی و رشد به صورت همگن امکان وقوع خواهند داشت. علاوه بر این، رشد رقابتی ستون ها می تواند منجر به کنده شدن قسمتی از آنها و پرتاب شدن آن در جبهه مذاب گردد.
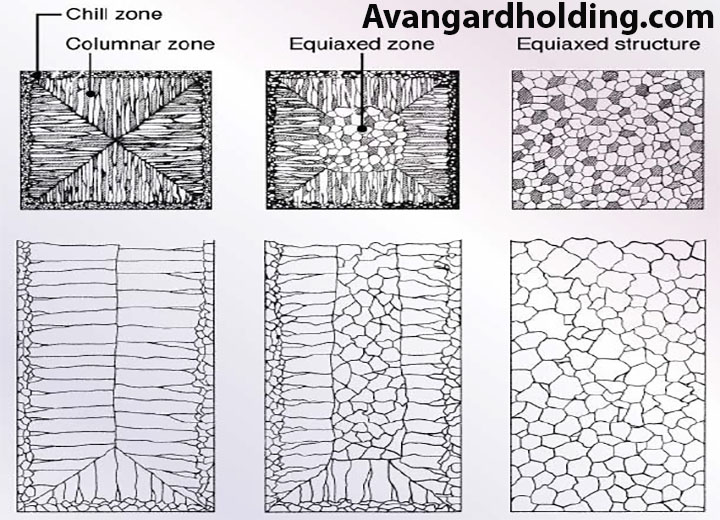