- صفحه اصلی
- خدمات ریخته گری
- آزمایشگاه وکنترل کیفیت در ریخته گری
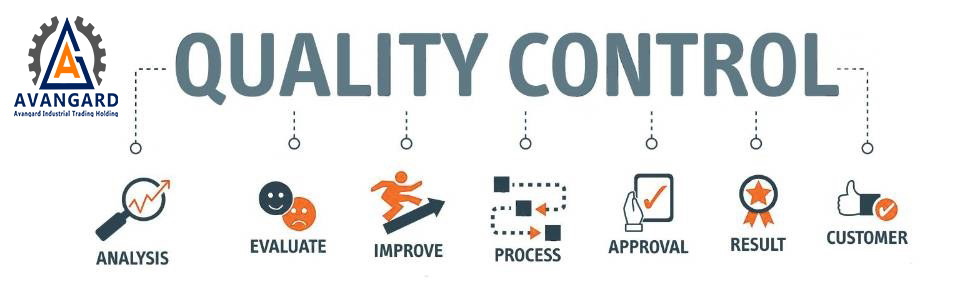
علاوه بر آنالیز قراضه، بررسی مواد مورد استفاده برای قالبگیری و مونتاژ نیز انجام می گردد.
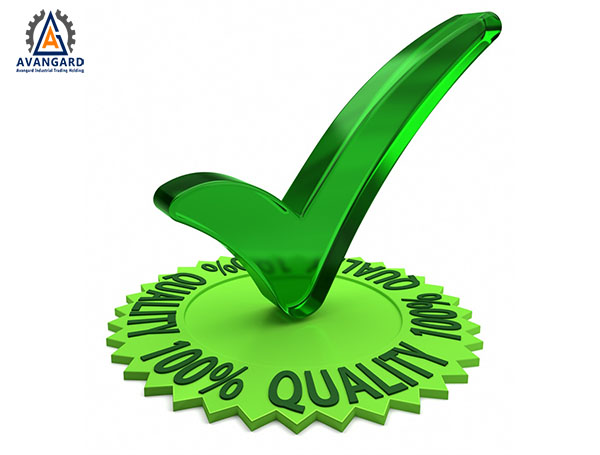
بخش ذوب به صورت متوالی، نمونه هایی را برای آنالیز به آزمایشگاه ارسال و در کمترین زمان ممکن از نتیجه آنالیز با خبر می شود تا ترکیب شیمیایی ذوب را تصحیح کند که در ادامه مطالب در خصوص دستگاه کوانتومتر بیشتر صحبت خواهیم کرد.
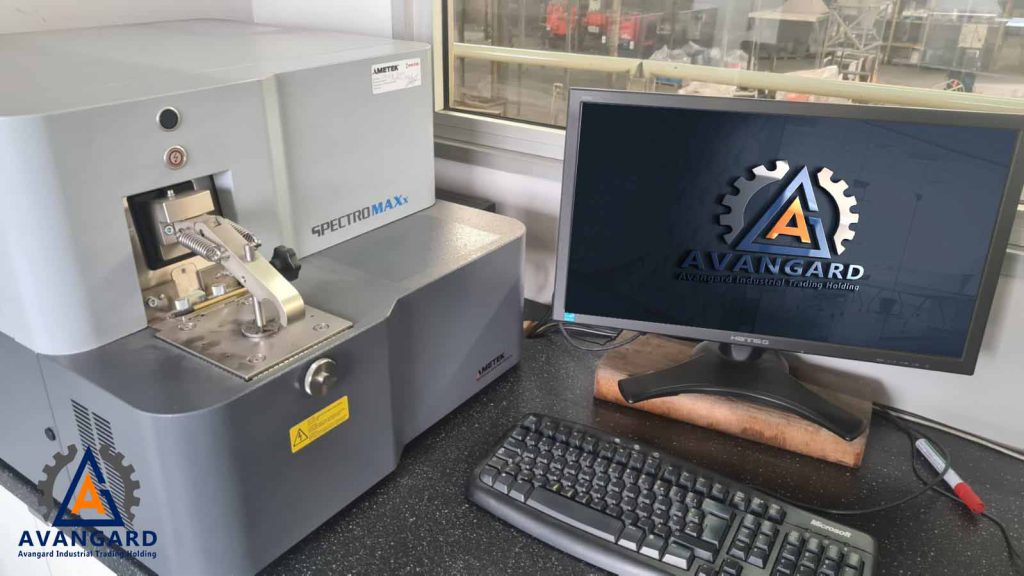
سختی قطعات تولید شده به عنوان یکی از مهمترین خواص مکانیکی قطعات تحت سایش همواره تحت کنترل است. به لحاظ حجیم بودن قطعات ریختگی، از دستگاه سختی سنج پرتابل برای اندازه گیری سختی استفاده می شود. همچنین ریزساختار محصولات تولیدی با کمک امکانات متالوگرافی موجود بررسی شده و امکان تصویربرداری و بایگانی نمونه ریزساختار به عنوان یکی از فاکتورهای کنترلی وجود دارد.
یکی دیگر از فعالیت های آزمایشگاه کنترل کیفیت در تائید قطعات تولید شده، انجام تست التراسونیک و دیگر تست های مرسوم در صنعت ریخته گری بر روی قطعات است تا از عدم وجود عیوب داخلی اطمینان حاصل شود. که در ادامه در خصوص تست های رایج بیشتر صحبت خواهیم داشت.
انواع آزمایش های کاربردی در شرکت آوانگارد:
- آنالیز شیمیایی (کوانتومتر)
- متالوگرافی و تعیین ساختار
- سختی سنجی
- تست مایع نافذ (تست PT )
- تست ذرات مغناطیسی (MT)
- تست التراسونیک (تست UT )
- رادیوگرافی (تست RT )
- تست خواص مکانیکی ( تست کشش، تست ضربه و…)
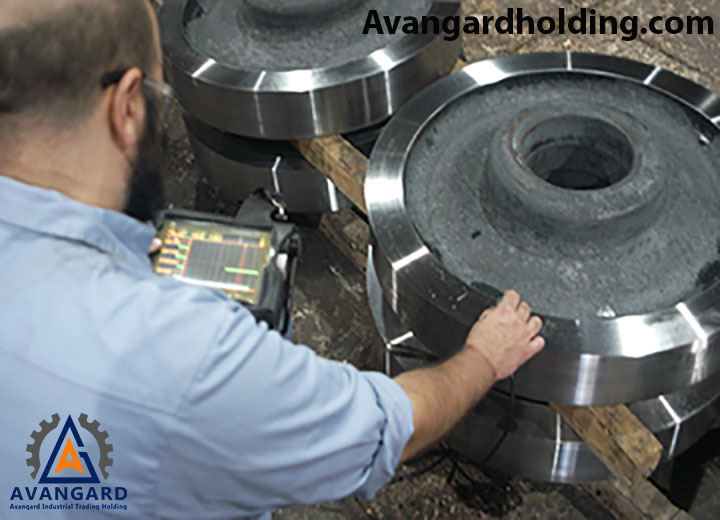
شرکت آوانگارد به عنوان یکی از شرکت های تولید کننده و تامین کننده در صنعت ریخته گری با برآورده کردن الزامات قانونی و نیاز های خاص مشتری، رسالت خود را جهت جلب رضایت و اعتماد مشتریان قرار داده و در این جهت اهداف اصلی زیر را دنبال می کند:
- تلاش در جهت ارتقاءکیفیت محصولات و بهبود مستمر کیفیت برای افزایش رضایت مشتری که هدف اصلی سازمان است .
- کاهش هزینه ها و ضایعات تولیدی با افزایش نسبی راندمان .
- توجه به سیستم آموزشی به عنوان ابزاری جهت ارتقاء توان تخصصی و فرهنگی پرسنل.
- تحویل بموقع محصول به مشتریان.
ابزار ها و تجهیزات در این حوزه در حقیقت زیر ساخت یک سیستم کنترل و اتوماسیون را تشکیل می دهند و شامل ابزاری نظیر : انواع کنترلر ، نشان دهنده ، ترانسمیتر، رکوردر و … می باشند که این ابزارها وظیفه اندازه گیری ، انتقال ، نمایش ، ثبت و کنترل پارامترهای مهم فیزیکی نظیر دما ، فشار، فلو، سطح مایعات ،ابعاد و … را در پروسه های صنعتی به شکلی دقیق بر دوش دارند.
متر ها یکی از ابزارهای اندازهگیری بسیار پر کاربرد در صنایع مختلف هستند. برخلاف ابزارهایی مانند میکرو متر و کولیس ، متر ها دقت بسیار زیادی ندارند اما میتوانند بازههای گسترده ای را اندازهگیری کنند که در مقایسه با محدوده اندازهگیری آنها، دقت قابل قبولی را دارند. به طور کلی متر ها بر اساس نوع اندازهگیری به دو نوع لیزری و ساده تقسیم میشوند.
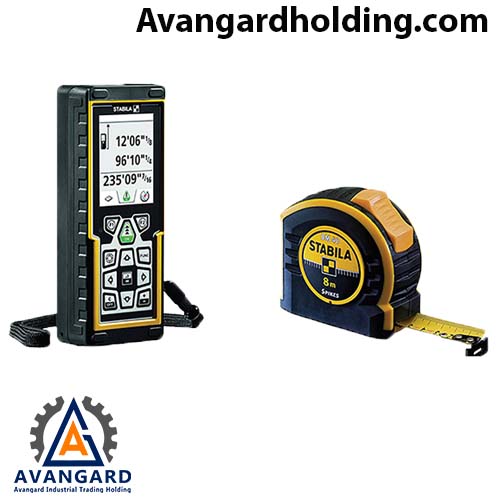
کولیس نوعی ابزار اندازهگیری با دقت بالاست که استفاده از آن در صنایع مختلف بسیار رایج است از کولیس می توان بعنوان دست راست مهندسین در صنایع مختلف نام برد. کولیس ها، فک هایی دارند که امکان اندازهگیری ابعاد مختلف اجسام مانند قطر داخلی و خارجی، طول، ضخامت و عمق را فراهم میکنند. به طور کلی کولیس ها از نظر نوع خواندن به سه نوع ساده، دیجیتال و ساعتی تقسیم میشوند، یکی از دلایل اصلی استفاده از کولیس ها دقت بالای آنها است. دقت اندازه گیری کولیس های ساده از حاصل تقسیم مقدار یک بر تعداد تقسیمات ورنیه به دست میآید. دقت اندازه گیری کولیس های معمولی و پر مصرف در صنعت حدودا تا 0.01 میلیمتر می باشد.
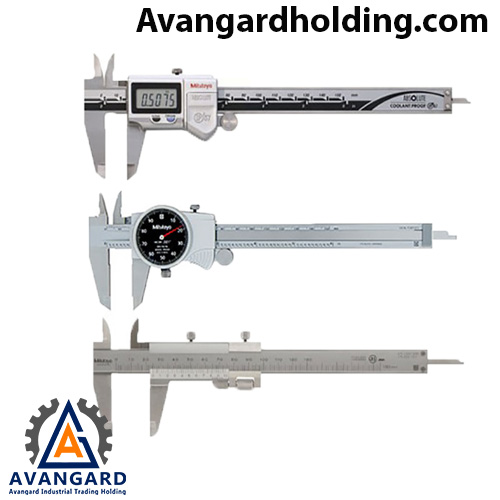
نوعی دیگر از ابزارهای اندازهگیری دقیق میکرومتر ها یا ریز سنج ها هستند که از دقت بسیار بالایی در اندازهگیری برخوردار هستند و به همین دلیل در مواقعی که دقت کولیس پاسخگو نباشد ﻣﯽ ﺗﻮان ﺑﺮای اندازه گیری های داﺧﻠﯽ، ﺧﺎرﺟﯽ، ارﺗﻔﺎع و ﺿﺨﺎﻣﺖ برخی قطعات از میکرو متر استفاده کرد. دقت میکرومتر ها معمولا به 0.001 میلیمتر میرسد.رمیکرومتر ها نیز دارای 2 نوع ساده و دیجیتال می باشد که در مدل دیجیتال اندازه گرفته شده به راحتی از روی صفحه نمایشگر قابل مشاهده است اما نوع ساده آن روش مخصوص خود را برای خواندن مقدار به دست آمده دارد.
در میکرومترها نیروی وارد ﺑﺮ ﻓﮏ ها و ﻗﻄﻌﻪ ﮐﺎر ﺑﺎ سیستم ﺟﻐﺠﻐﻪ، ﺗﺤﺖ ﮐﻨﺘﺮل در آﻣﺪه اﺳﺖ. این موضوع ﺑﺮﺧﻼف نحوه خواندن کولیس های ورنیه دار میلیمتری می باشد ﮐﻪ نیروی وارده از ﻃﺮف ﻓﮏ ها ﺑﻪ ﻗﻄﻌﻪ ﮐﺎر ﺗﺤﺖ ﮐﻨﺘﺮل ﻧﺒﻮد، این به آن معنی است که نیروی وارد بر قطعه کار به حد مشخصی که رسید دسته جغجغه به صورت هرز می چرخد و همین امر دقت کار را بالا می برد.
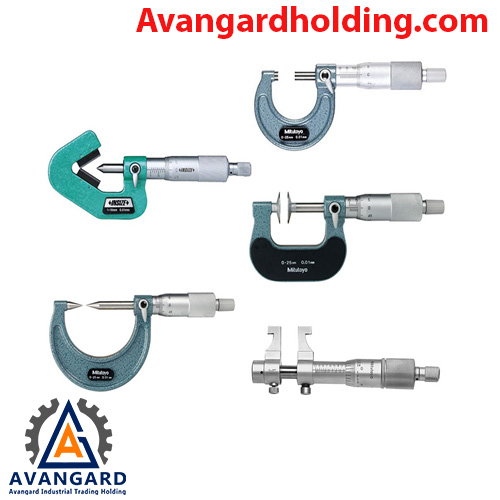
زاویه سنج ابزار مخصوصی برای اندازهگیری زاویه های مختلف اجسام است که از کاربرد فراوانی در مشاغل گوناگون برخوردار است. یکی از این کاربردها تعیین زاویه برش به خصوص در فارسی بر کردن قطعات است. زاویه سنج ها در 2 مدل ساده و دیجیتال استفاده می شوند. زاویه سنج ساده دارای یک نقاله و یک خط کش متصل به هم می باشد که با قرارگیری شی مورد نظر وسط این دو، می توان زاویه بدست آمده را از روی نقاله خواند. در نوع دیجیتال دو خطکش از طریق یک مفصل به همدیگر وصل شدهاند که بوسیله یک نمایشگر دیجیتال مقدار زاویه بین این دو خط کش به راحتی قابل خواندن خواهد بود.
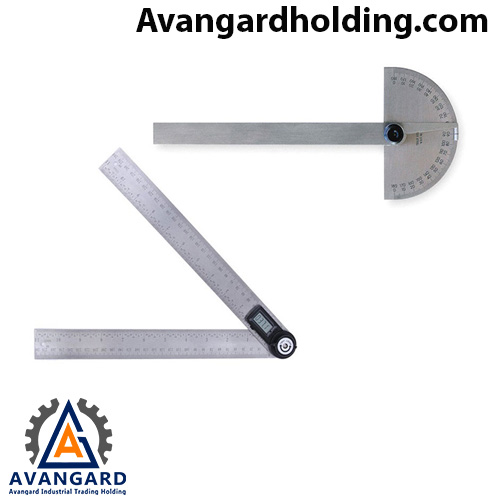
گونیا یک نوع ابزار اندازه گیری صلب است که برای تعیین زاویه 90 درجه و عمود بودن دو قطعه بر همدیگر مورد استفاده قرار میگیرد. گونیا ها با دقتهای متفاوت و در ابعاد مختلفی تولید میشوند. گونیا مویی، گونیا نجاری و گونیا مرکب نمونه هایی از انواع پر مصرف در صنعت هستند. گونیا مویی دقیق ترین نوع گونیا حساب می شود که با دقت بالا و از جنس فولاد ضدزنگ ساخته میشود و در مشاغلی مانند تراشکاری که به دقت زیادی نیاز است استفاده می شود. گونیا های نجاری دارای ابعاد بزرگتری نسبت به گونیا های مویی هستند اما دقت پایین تری دارند و از یک خط کش و یک پایه تشکیل شدهاند. گونیا سه تکه یا گونیا مرکب نوعی ابزار اندازه گیری پر کاربرد است که علاوه بر گونیا از آن میتوان به عنوان زاویه سنج، خطکش، تراز و مرکز یاب استفاده کرد.
محصول مرتبط: محصولات ریخته گری
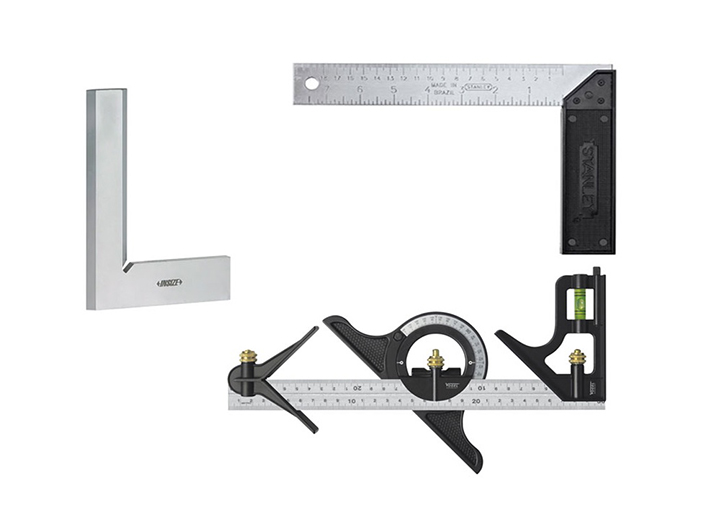
پرگارهای صنعتی یکی از انواع پرگار ها هستند که برای انجام بسیاری از کارها مانند اندازه گیری، اندازه گذاری، سنجش نسبت دو قطعه، خط کشی، پیدا کردن مرکز دایره، کشیدن دایره، پیدا کردن خط های عمود بر دایره و بسیاری دیگر از کارهایی که در هندسه صنعتی بکار می رود استفاده می شود.انواع مختلفی از پرگارهای صنعتی وجود دارد که درصنایعی مثل مهندسی و نقشه کشی و … استفاده می شوند که از انواع آن می توان پرگار صنعتی مستقیم، پرگار صنعتی داخل سنج، پرگار صنعتی خارج سنج، پرگار صنعتی مدرج، پرگار صنعتی عقربه ای، پرگار صنعتی دیجیتال، پرگار صنعتی مقسم و پرگار صنعتی میکرومتر را نام برد.
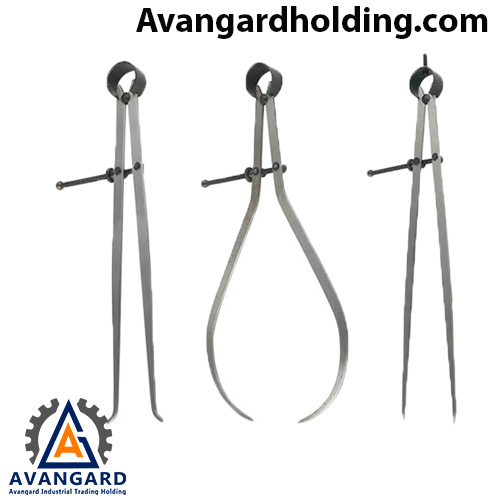
خط کش صنعتی یکی دیگر از ابزارهای اندازه گیری است که برای ترسیم خطوط و یا اندازه گیری قطعات و یا جهت کنترل در میزات تختی سطوح مورد استفاده قرار می گیرد. خط کش های صنعتی برای محیط های صنعتی طراحی شده اند پس از استحکام بالایی برخوردار هستند و معمولا از جنس فولاد ضد زنگ می باشند و در برابر سایش و خوردگی مقاوم هستند.
انواع خط کش
خط کش ها انواع گوناگونی دارند که عبارتند از:
خط کش ساده: از لبه های مدرج شده این خط کش برای اندازه گیری و خط کشی استفاده می کنند.
خط کش مویی: از این خط کش برای اندازه گیری صافی لبه و تشخیص میزات تختی با کمک فیلر استفاده می شود.
خط کش دیجیتال: یکی دیگر از انواع خط کش هاست که برای مواقعی که سرعت و دقت اندازه گیری اهمیت داشته باشد از آن استفاده می شود.
خط کش الگوبرداری: از این خط کش برای اندازه گیری زوایای غیرقابل دسترس و دشوار در صنعت چوب و مدل سازی قطعات ریختگی استفاده می شود.
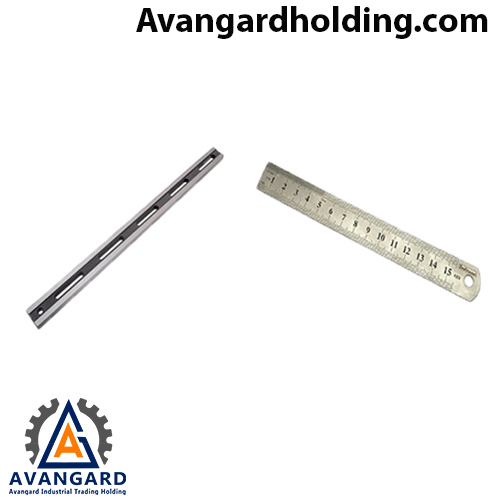
آچار فیلر (Feeler Gauge) به مجموعهای از چند ورق کوچک فلزی اطلاق میشود که هر کدام از این ورقها با توجه به استادارد از یک سطح و ضخامت مشخص ساخته شده است. این نوارها با توجه به فاصله دو سطح مماس بین خط کش فلزی با سطح قطعه کار، در شیار بین آنها قرار میگیرد و بنا به اندازه فاصله و سایز ضخامت نوار آچار فیلر، نشان میدهد که اندازه فاصله سطح بین خط کش و قطعه چه مقدار می باشد یا به اصطلاح میزان تختی را مشخص می نماید
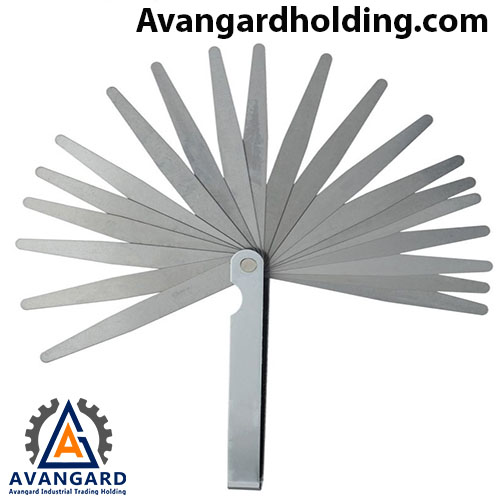
ساعت اندازه گیری یا ساعت اندیکاتور یکی از پرمصرف ترین انواع ابزارهای اندازه گیری دقیق است که برای اندازه گیری اختلاف سطح یک یا دو قطعه، یا برای کوپل کردن و هم راستا کردن دو شفت و قطعه، و یا برای سنجش تخت و تراز بودن قطعه و …
در بخش های مختلف صنعت کاربرد فراوان دارد که در انواع مختلفی مانند ساعت شیطانکی، ساعت اندیکاتور ساعتی یا ساعت اندیکاتور عقربه ای و ساعت اندیکاتور دیجیتال در بازار وجود دارند.
ساعت اندیکاتور نوعی ابزار اندازه گیری با دقت بسیار بالاست که در انواع صنایع سبک و سنگین مورد استفاده قرار می گیرد. علت این نامگذاری شباهت بالای این ابزار با ساعتهای عقربه ای است. دلیل اصلی بکارگیری از آن دقت اندازهگیری آن است که این دقت معمولا بین 0.01 تا 0.001 میلیمتر قرار دارد که کاملا به مدل ساعت و شرکت سازنده آن بستگی دارد.
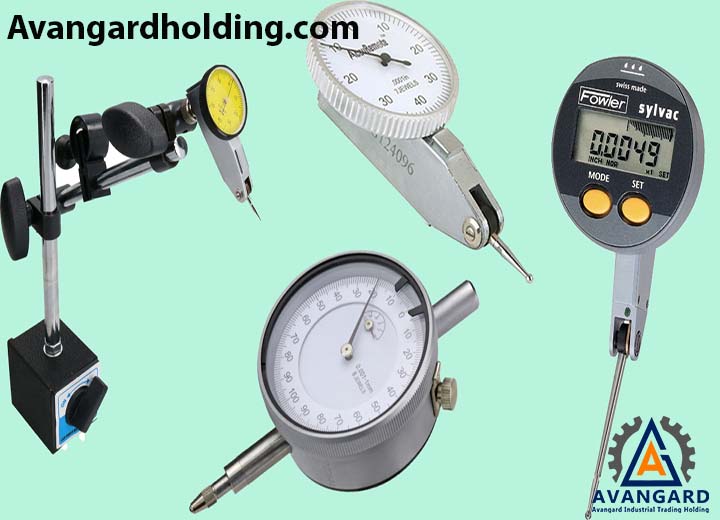
تراز یکی از انواع ابزارهای دستی است که کاربرد بسیار زیادی در فرایند قالبگیری در ریخته گری دارد. از این وسیله به منظور کنترل شیب سطح و مشخص کردن افقی و عمود بودن سطوح استفاده میشود. بهتر است بدانید که امروزه ترازهای متفاوتی با قابلیتهای گوناگون طراحی و تولید شده است. ترازهایی که علاوه بر کنترل شیب توانایی اندازه گیری زاویههای مختلفی را نیز دارند. ترازها به طور کلی به دو دسته مندرج و غیر مندرج تقسیم بندی میشوند، لازم بذکر است که امروزه ترازهای دیجیتال و لیزری نیز به بازار آمده اند.
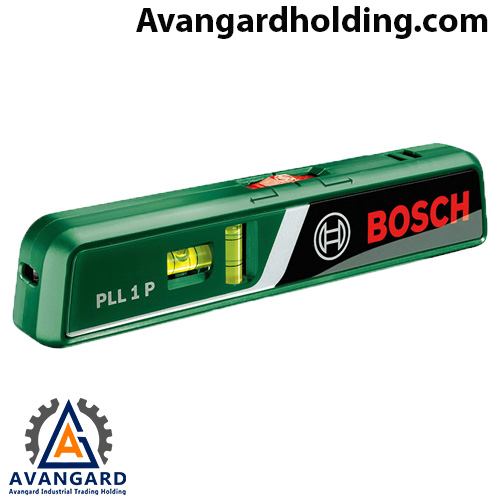
بومه وسیله ای است جهت سنجش دانسیته که داروساز فرانسوی آنتون بومه (Antoine Baumé) در سال 1768 برای اندازه گیری دانسیته مایعات مختلف ابداع نمود. مقیاس بومه (B) یک واحد برای اندازه گیری چگالی نسبی مایعات (چگالی مایعات نسبت به چگالی آب) است و واحد بومه سنج به درصد می باشد. بومه آزمایشگاهی ابزار سادهای برای کنترل و اندازه گیری چگالی و یا گرانش ویژه یک محلول است. بومه آزمایشگاهی شامل یک استوانه شناور است که انتهای پایینی آن به شکل مخروط و سنگین و انتهای بالایی آن به صورت لولهای باریک است. زمانی که بومه آزمایشگاهی را در یک مایع قرار دهیم شکل عمودی به خود خواهد گرفت و در مایع فروخواهد رفت که میزان فرورفتن این ابزار با چگالی آن مایع ارتباط دارد، عملکرد بومه آزمایشگاهی بر پایه قانون ارشمیدس است که یک جامد معلق در سیال بوسیله یک نیرو برابر وزن سیال جابجا شده و شناور میماند.
در واحد کنترل کیفیت آوانگارد جهت کنترل مواد اولیه ریخته گری مانند پوشان قالب(رنگ قالب)،الکل صنعتی،چسب سیلیکات سدیم و … از این ابزار استفاده می شود.
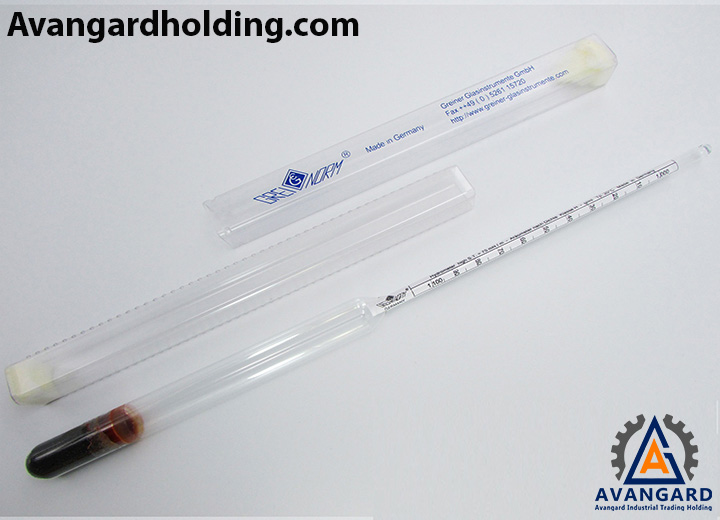
ترمومتر دستگاهی است که دما رابراساس واحد اندازه گیری سیلسیوس، فارنهایت، کلوین وگرادیان اندازه گیری می کند.
انواع ترمومترها در صنایع مختلف متفاوت است در اینجا ما به معرفی ترمومترهایی که در صنعت فولاد، ذوب و ریخته گری مورد استفاده قرار می گیرد می پردازیم .
دمای فلز مذاب باید در حد محدوده مشخص و مورد نیاز بخش متالورژی و کنترل کیفیت باشد . تشخیص دمای مذاب هنگام رسیدن فلز به حالت مذاب در کوره ذوب و بار ریزی آن ، برای ریخته گر ماهر چه سنتی و چه علمی حائز اهمیت می باشد. ندانستن دمای ذوب و افزایش غیر نرمال دمای آن باعث به وجود آمدن مشکلات فراوانی مانند اتلاف برخی عناصر و کاهش عمر مفید بدنه کوره و حتی تغییر شکل قالب می شود. حتی ندانستن کم بودن دمای مذاب و ذوب ریزی باعث بروز مشکلاتی همچون ماسیدن مذاب در پاتیل یا راه گاه های فرعی و اصلی قالب، نرسیدن مذاب به تمامی قسمتهای قالب و غیره می شود. بنابراین دانستن دمای صحیح مذاب برای ریخته گر یکی از دانسته های بسیار مهم در مورد مذاب می باشد.
در میان روش های شناخته شده اندازه گیری دمای مذاب به دو روش مشخص می گردد، یک نوع غیرتماسی( روش لیزری یا روش پیرومتری( چشمی)) و نوع دیگرترمومترهای تماسی مورد تقسیم بندی می شوند که دربین این ترمومترها ،ترمومترهای تماسی جهت دمای مذاب دارای دقت بالایی هستند و همچنین در واحد کنترل کیفیت آوانگارد جهت کنترل دمای قطعه برای تخلیه از قالب یا دمای کوره عملیات حرارتی و … از ترمومتر نوع غیرتماسی( روش لیزری یا روش پیرومتری) نیز استفاده می شود.
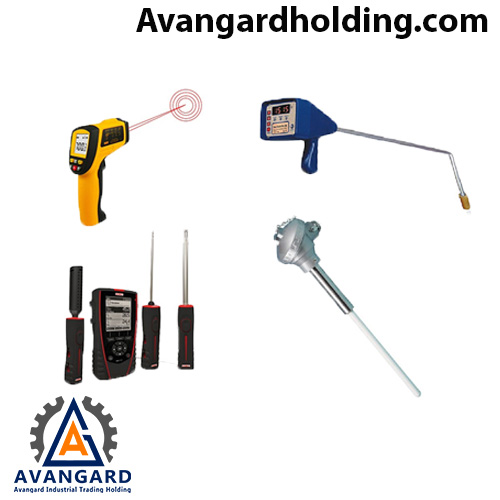
کوانتومتر دستگاهی است که به کمک آن می توان مقدار درصد عناصر مختلف موجود در یک قطعه را اندازه گیری کرد. دستگاه طیف سنج نوری یا کوانتومتر، از جمله سیستمهای آنالیز دقیق برای اندازه گیری عناصر موجود در فلزات است که قابلیت تجزیه آلیاژها را با دقت زیاد دارد و تمامی عناصر آلیاژی ر نمونه را تعیین میکند. بدین گونه که ابتدا سطح قطعه ای که نیاز به تست دارد مورد آماده سازی قرار گرفته به طوری که سطح آن کاملاً صاف و عاری از هر گونه آلودگی و چربی می شود و نمونه درست از همان قسمت پرداخت شده بر روی محلی که قرار است اسپارک زده شود قرار داده می شود. مکانیزم این آزمایش بر پایه نشر نوری است. نمونه ماده مورد آزمایش در اثر تخلیه الکتریکی تبخیر می شود، اتم ها و یون های تشکیل شده از تبخیر اتمی تحریک شده و تابش می کند، سپس با توجه به محدوده طول موج نشر نور هر عنصر، دقیق ترین خط نشری برای اندازه گیری غلظت آن عنصر در نمونه انتخاب می شود.
در بیشتر کوانتومتر ها بعلت محدودیت در محل قرارگیری نمونه، توانایی آنالیز نمونه ها با هر سایزی وجود ندارد. و باید در ابعاد خاصی نمونه تهیه و مورد آزمایش قرار داده شوند. البته لازم به توضیح است که نتایج حاصل از این دستگاه ها دارای دقت بالاتری نسبت به دستگاه های پرتابل است که قطعه را در فضای باز مورد اسپارک قرار می دهند. اسپارک همان جرقه ای است که الکترود دستگاه کوانتومتر بر روی سطح قطعه مد نظر ایجاد می کند تا توسط طول موج های که از قبل برای دستگاه تعریف شده است به میزان عناصرموجود در قطعه پی برده شود.
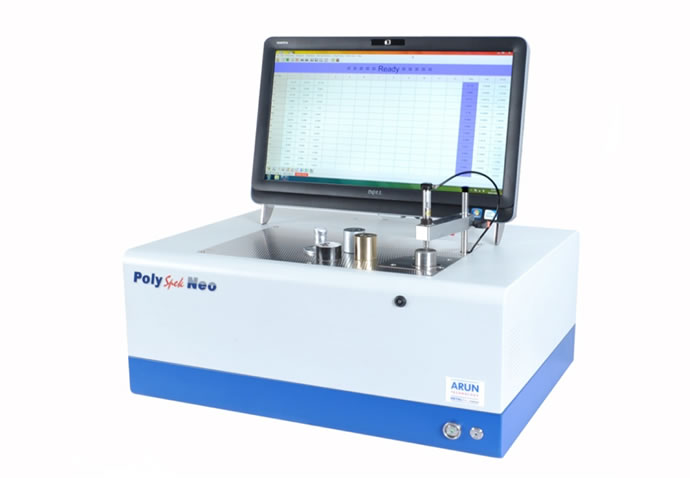
سختی سنجی به میزان فرو رفتن یک جسم سخت فرو رونده بر روی سطح یک فلز یا ماده دیگر است که بوسیله تمام دستگاه های سختی سنج انجام می شود و واحد های مختلفی از جمله راکول، برینل ، ویکرز و دیگر واحد های سختی را دارند.
برای سنجش سختی فلزات اکثرا از واحد راکول استفاده می کنند که نماد لاتین آن HRC است و در صنعت ریخته گری نیز برای بیان سختی فولاد ها اکثرا از راکول استفاده می کنند.
سختی سنج ها به طور کلی در دو نوع دستگاه های قابل حمل یا سختی سنج پرتابل که می توان براحتی آن را در دست گرفت و پراب آن را روی فلز قرار، داد و سختی آن را اندازه گرفت و نوع دوم سختی سنج های بزرگ تر که قابل حمل نیستند و باید قطعه فلز یا فولاد را در زیر آن قرار داد و سختی آن را اندازه گرفت که بیشتر در محیط آزمایشگاه های صنعتی از آن استفاده می شود ،تقسیم بندی می شوند.
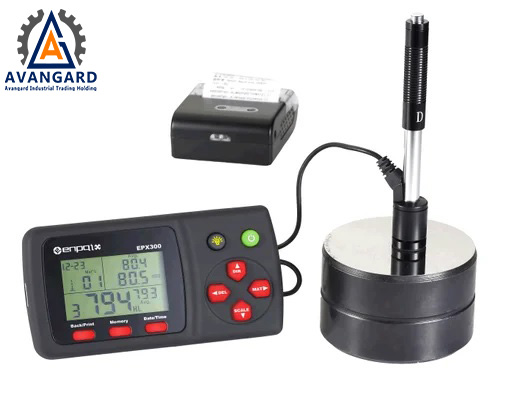
متالوگرافی به انگلیسی Metallography به علم و هنر آمادهسازی نمونههای فلزی و بررسی ریز ساختار میکروسکوپی آنها گفته میشود. در بسیاری از مواد، دانههای تشکیل دهنده آنها دارای ابعاد میکروسکوپی هستند و اندازه آنها در حدود میکرون می باشد که اجزای آنها باید با استفاده از میکروسکوپها دیده و بررسی شوند. اما مشکل فقط بزرگ نمایی نیست. بلکه سطح ریزساختار نیز باید آماده شود. در بررسیهای میکروسکوپی فقط سطح خارجی اجسام مورد بررسی قرار میگیرد، بنابراین باید سطحی بسیار شفاف و آینه ای جهت دستیابی به اجزاء مهم ریز ساختار فراهم شود. مجموعه فعالیتهایی که منجر به فراهم آمدن چنین سطحی میشود و بررسی میکروسکوپی ریز ساختار را متالوگرافی مینامیم، متالوگرافی به معنای بررسی و مطالعهی ریز ساختار داخلی فلزات میباشد. متالوگرافی به سرعت در رشته متالورژی جایگاه خود را به عنوان یکی از اصول مهم علم و مهندسی مواد پیدا کرد. امروزه بدون فهمیدن اصول مدرن متالوگرافی و استفادهی بهینه از آن، فعالیتهای صنعتی و پژوهشی و کنترل کیفیت با مشکل روبرو خواهد شد. بررسی میکروساختار و ماکروساختار فلزات با استفاده از میکروسکوپهای نوری، الکترونی و مقایسه آن ها با استانداردهای معین، پیشبینی خواص فیزیکی و مکانیکی ، تجزیه و تحلیل عیوب ساختاری و سطحی را امکان پذیر میسازد که امری مهم در صنعت ریخته گری می باشد که کادر مهندسی شرکت آوانگارد تسلط کامل به بخش متالوگرافی را دارا می باشند.
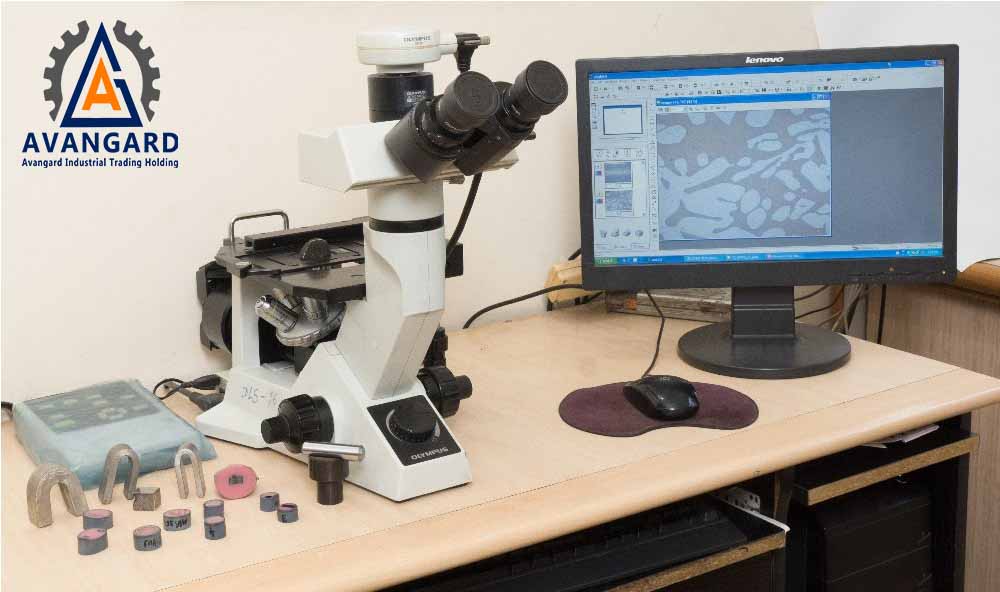
آزمون آلتراسونیک یا (UT) یک روش غیر مخرب است که در بازرسی عیوب داخلی انواع قطعات به خصوص قطعات ریخته گری شده بسیار پرکاربرد است. تستUT در تمامی صنایع مطرح و برای بازرسی جزیی تر قطعات ریخته گری، اتصالات جوش و موارد دیگر استفاده می شود. از آزمون اولتراسونیک برای پی بردن به عیوب داخلی قطعات نظیر عیوب انقباضی، ترک ها و حفرات استفاده می شود. در این مکانیزم، امواج فراصوت با بسامد زیاد توسط یک مولد صوتی بر روی قطعه هدایت می شود. این امواج پس از برخورد به عیوب زیرسطحی ماده بازتاب پیدا می کنند. که امواج بازتاب شده بوسیله یک مولد صوتی دریافت شده و به پالس های الکتریکی تبدیل می شوند. و در نهایت این پالس ها به صورت یک سیگنال واضح بر روی صفحه نمایش ظاهر می گردند. اپراتور با بررسی و تحلیل این سیگنال ها می تواند به اطلاعات مختلفی از قبیل مکان، ابعاد، عمق و نوع عیب بر روی قطعه پی ببرد.
مطلب مرتبط: طراحی و مدلسازی در ریخته گری
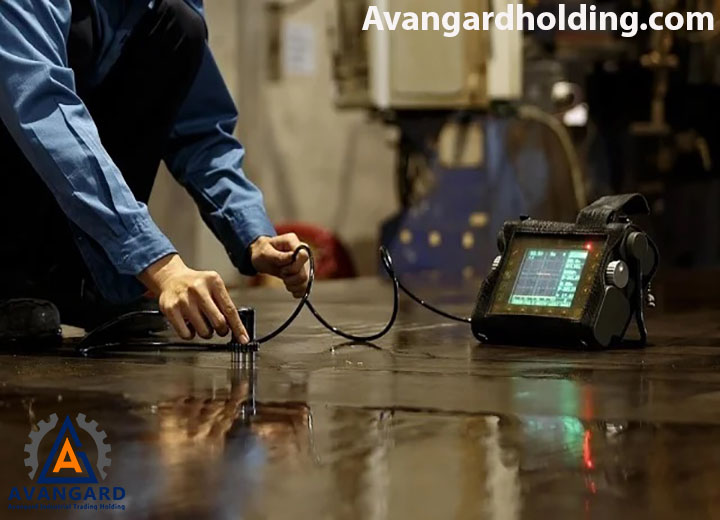
آزمایش مایع نافذ یا PT نوعی دیگری از آزمایش های NDT برای تشخیص و شناسایی عیوب سطحی و همچنین عیوب زیرسطحی است که به سطح راه دارند. آزمایش PT بهترین روش برای بازرسی انواع ترک های سطحی، تخلخل، تورق، عدم اتصال در جوش یا لبه های باز و هرگونه نشتی در قطعات ریخته گری شده می باشد . در امروزه، آزمایش PT با موفقیت در انواع مختلف صنایع مورد استفاده قرار میگیرد. این آزمون با موفقیت بر روی فلزات آهنی و غیرآهنی، سرامیکها، قطعات متالورژی پودر، قطعات جوشکاریشده، شیشهها و برخی از پلاستیکها انجام میشود. جهت تست PTنیازمند به سه نوع اسپری با نام های
1- اسپری تمیز کننده/پاک کننده Remover/Cleaner
2- اسپری ترک یاب نفوذکننده Penetrant
3-اسپری ترک یاب آشکار کننده Developer
می باشد که در تست PT مایع نافذ برای مدت زمانی مشخص، به سطح جسم مورد نظر اعمال می شود. این مایع نافذ به دلیل پدیده مویینگی به داخل عیب باز سطحی نفوذ می کند. در مرحله بعد مایع اضافی از روی سطح برداشته می شود. سپس سطح را خشک کرده و مایع آشکارساز جذب می شود که اندازه، موقعیت و ماهیت ناپیوستگی در صورت حضور، آشکار می گردد. بنابراین آزمایش PT با مشاهده سطح قطعه و دیدن کنتراست رنگی که بین مایع نافذ باقی مانده که از درون عیب به بیرون کشیده شده و سطح قطعه، انجام می گیرد.
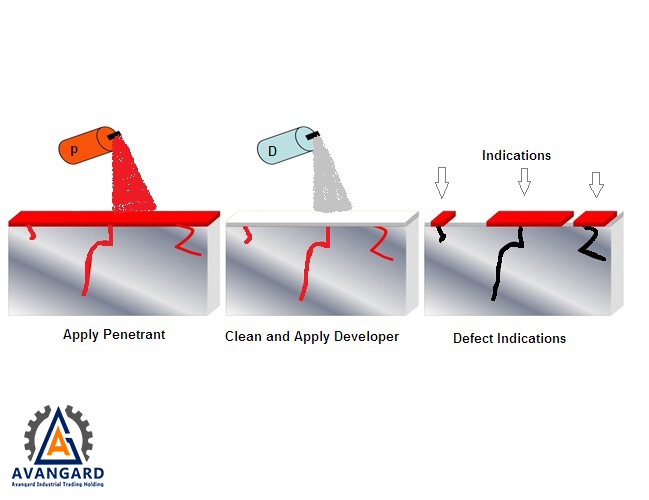
تست مغناطیسیMT که مخفف کلمه انگلیسی (Magnetic Particle Test ) است و گاهی اوقات با نام بازرسی ذرات مغناطیسی MPI که مخفف کلمه انگلیســــی (Magnetic Particle Inspection) شنــاخته می شود . یک روش بازرسی غیر مخرب NDT میباشد که جزو روش های ساده برای بررسی و تشخیص عیوب در داخل و نزدیک به سطح قطعه مورد استفاده قرار می گیرد . تست مغناطیسیMT بر اساس مفهوم نشت شار مغناطیسی انجام می شود .
تست مغناطیسیMT همانطور که از نام آن پیداست ، فقط قابلیت استفاده برای بازرسی موادی کـــه قابلیت مغناطیسی شدن (نظیر فولاد های کربنی) را دارند استفاده می شود .
برای این کار قطعه به صورت مستقیم یا غیرمستقیم آهنربا می شود. در آهنربا شدن قطعه بصورت مستقیم جریان برق مستقیم از داخل قطعه عبور داده می شود که سبب به وجود آمدن یک میدان مغناطیسی در ماده می شود . در آهنربا شدن قطعه بصورت غیرمستقیم میدان مغناطیسی توسط یک آهنربای دیگر در داخل قطعه تست القا می شود و شار مغناطیســـی بصورت یکپارچـــــه از قطب N بـه قطب S به جریان میافتد و در صورت وجود هرگونه ناپیوستگی،تخلخل ، وجود ترک و … داخل قطعه از آنجا که ذرات آهن در امتداد خطوط میدان مغناطیسی متمرکز می شوند ، وقتی بازرس به قسمتی از قطعه که ترک خورده است میرسد، قطبهای اضافی N و S در آنجا تجمع مییابند. با این مکانیزم، بازرس میتواند به وجود ترک در قطعه پی ببرد..
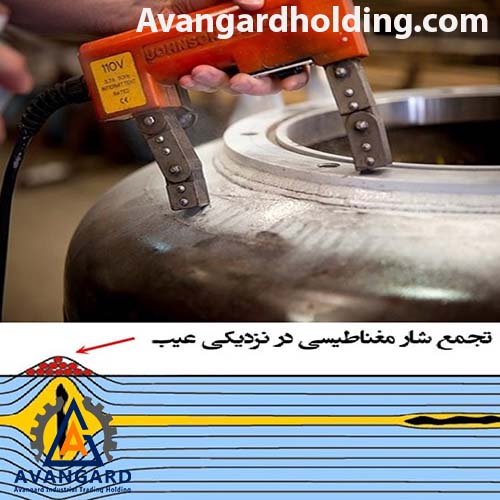
رادیوگرافی (تست RT ) يکي از پرکاربردترين روش هاي تست هاي غير مخرب (NDT)براي رديابي عيوب داخلي مثل حفره هاي گازي مي باشد.عيوب صفحه اي نيز مي توانند با جهت گيري مناسب توسط راديوگرافي رديابي شوند اين روش همچنين براي پيدا کردن تغييرات ترکيب در مواد، ضخامت سنجي، تعيين محل قطعات اضافي يا معيوب که در داخل دستگاه ها وجود دارند و از ديد پنهان مي باشند استفاده شوند. مزيت اوليه استفاده از پرتوهاي يونيزه کننده درNDT اين حقيقت مي باشد که مي توانند با استفاده از اين پرتوها در اجسام با اشکال مختلف و اندازه هاي ميکروني قطعات الکترونيکي استفاده شوند. در تست RT از اشعه ایکس یا گاما برای پرتونگاری استفاده می شود. پرتو ایکس یا گاما به جسم تابیده می شود و به علت طول موج پایین، اشعه ها جذب قطعه مورد آزمایش می شود. تست رادیوگرافی صنعتی یا RT یکی از تستهای غیرمخرب (NDT) برای بررسی قطعات ریختهگری است که به وجود و شکل عیوب ماکروسکوپیک یا سایر ناپیوستگیها در داخل قطعه اشاره میدهد. این روش از توان نفوذ پرتوهای ایکس یا گاما در اجسام بهره میبرد. هرچه طول موج کوتاه تر باشد قدرت نفوذ پرتو به داخل اجسام بیشتر است. تمام تابش در قطعه نفوذ نمی کند بلکه قسمتی از آن جذب می شود. مقدار جذب، تابعی از چگالی و ضخامت قطعه است. مثلا اگر حفره ای در قطعه وجود داشته باشد، پرتو تابش شده نسبت به یک قطعه سالم از میزان فلز کمتری عبور می کند. در نتیجه میزان پرتو جذب شده در ناحیه معیوب تغییر خواهد نمود. تغییرات در جذب پرتو روی فیلم حساس به تابش ثبت و حضور عیب نمودار می شود. از آنجا که نوع و اندازه عیوب تاثیرات متفاوتی بر عملکرد قطعه ریختهگری دارند، بازرس در تفسیر فیلم رادیوگرافی مسئول است نوع و اندازه عیوبی از قبیل تخلخل گازی یا حفرات زیرین، آخال های ماسه ای، حفرات انقباضی، انقباضات دندریتی، ترک ها، آخال ها و… را پیدا کند. در این زمینه استاندارد ASTM E155 برای کمک به بازرسین برای ارزیابی بهتر عیوب یافتشده در قطعات تولید شده ارائه شده است.
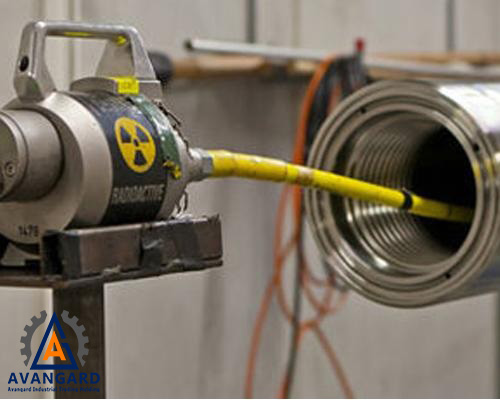
آزمون های خواص مکانیکی نیز همانند آزمون های غیر مخرب با این تفاوت که اکثر این تست ها مخرب هستند، یکی از روش های رسیدن به اطمینان ازعملکرد قطعه و ایمنی آن می باشد. تست های خواص مکانیکی یک بخش اصلی از فرآیند طراحی و ساخت محصولات هستند و از خواص مدنظر مواد تا نهایی شدن قطعه در فرآیند ساخت با ما همراه می باشد.
خواص مکانیکی هنگامی بیان می شود که نیرویی به یک متریال وارد شود. خواص مکانیکی معمولا به رفتار الاستیک و پلاستیک ماده مربوط می شود و بیشتر اوقات جهت اندازه گیری این خواص نیاز به تخریب ماده است به این صورت که تست های مکانیکی اغلب به صورت مخرب می باشند ولی در شرکت مهندسی آوانگارد گاهی اوقات با تایید مشتری از وای بلوک Y- Block بصورت چسبیده به قطعه استفاده می شود که پس از سیکل های عملیات حرارتی وای بلوک Y-Block مورد تست های مکانیکی مورد نیاز قرار می گیرد تا از تخریب قطعه جلوگیری شود. در شرکت آوانگارد برحسب آلیاژ و نیاز قطعه از انواع آزمون های مکانیکی /تست های مکانیکی از قبیل 1- آزمون کشش2- آزمون فشار3- آزمون سختی سنجی4- آزمون پیچش5- آزمون خمش6- آزمون ضربه7- آزمون خستگی8- آزمون خزش و… استفاده می شود.
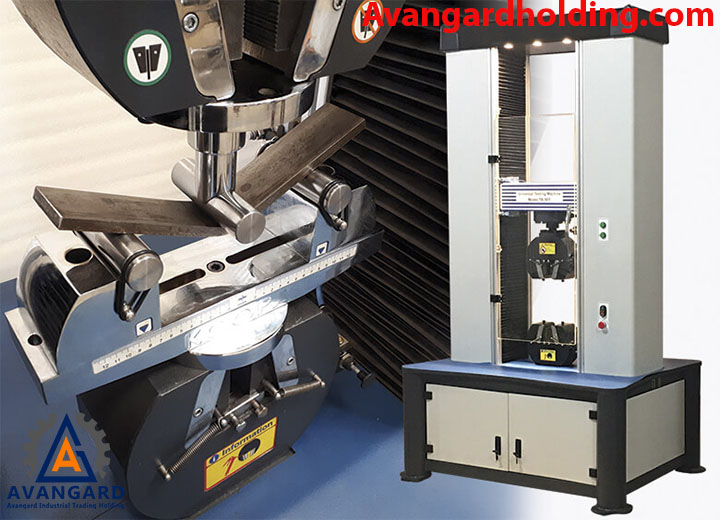
واحد کنترل کیفیت شرکت آوانگارد ضمن تاکید بر بهبود مستمر تمام مراحل طراحی اولیه، ریخته گری، عملیات حرارتی، ماشین کاری و کنترل دقیق تمام فرآیند های خرید، تولید و کنترل نهایی محصولات را بر عهده دارد؛ که کلیه انتظارات و خواسته های مشتریان و کارفرمایان محترم را برآورده سازد.
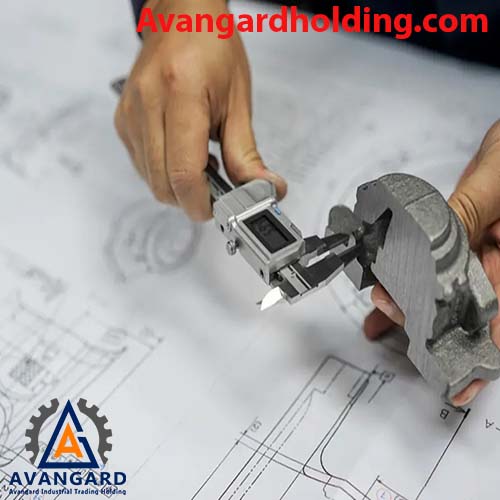
مسئولیت اصلی ما آن است که اطمینان یابیم نظام مدیریت کیفیت همواره برقرار و جاری است و محصول ارسالی دارای بالاترین حد استاندارد های مشتریان گرامی می باشد.