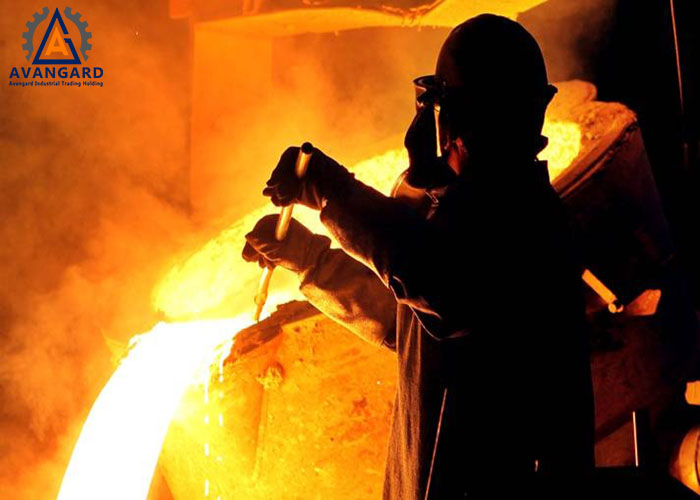
چدنهای سفید پرکروم یا چدن های کروم به عنوان یکی از پیشرفتهترین آلیاژهای مقاوم به سایش و خوردگی شناخته میشوند که کاربردهای فراوانی در صنایع مختلف دارند. چدنهای سفید آلیاژی پرکروم با داشتن محتوای کروم بالا (12 تا 35 درصد) و کربن (1.5تا 3.5 درصد)، ساختاری منحصر به فرد دارند. حضور کروم، که یکی از قویترین کاربیدزاها و عامل تشکیل پرلیت است، موجب تشکیل ریزساختارهایی با فازهای زمینهای شامل فریت، آستنیت یا مارتنزیت و کاربیدهایی مانند M₇C₃ و M₃C میشود. این کاربیدها به طور مستقیم از مذاب طی انجماد یا در حین عملیات حرارتی ایجاد شده و سختی و مقاومت به سایش بسیار بالایی را به این چدنها میبخشند.
در فرآیند انجماد این آلیاژها، به دلیل حضور کروم، گرافیت تشکیل نمیشود و فازهای کاربیدی پایدار به وجود میآیند. برای جلوگیری از تشکیل پرلیت در فاز زمینه، معمولاً از مقادیر کمی عناصر آلیاژی نظیر نیکل، مولیبدن یا مس استفاده میشود که به بهبود خواص مکانیکی آلیاژ و افزایش مقاومت آن کمک میکند. با افزایش میزان کروم در ترکیب آلیاژ، کاربیدهای M₃C به تدریج جای خود را به کاربیدهای M₇C₃ میدهند و در چدنهایی با کروم بیش از ۱۵ درصد، بیشتر کاربیدها از نوع M₇C₃ هستند. این ویژگی موجب میشود که چدنهای پرکرم مقاومت استثنایی در برابر سایش، حرارت، و خوردگی از خود نشان دهند.
یکی از مهم ترین استانداردهای معتبر جهانی در خصوص این نوع چدنهای پر کرم، ASTM A532 میباشد که ویژگیهای شیمیایی و مکانیکی مورد نیاز برای تولید چدنهای سفید الیاژی پرکرم ضدسایش را مشخص می نماید. این استاندارد تضمین میکند که آلیاژ تولیدشده دارای کیفیت مناسب برای کاربردهای سنگین صنعتی باشد و در عین حال با قیمت مناسبتر نسبت به فولادهای ضدزنگ عرضه شود.
به نقل از متافو چدن پر کروم یکی از انواع چدن سفید است که با محتوای بالای کروم، مقاومت خوبی در برابر سایش از خود نشان میدهد. این نوع چدن یکی از بهترین ترکیبها برای ارائه همزمان مقاومت به سایش و چقرمگی است و قابلیت ریختهگری قطعات با وزن بالا را دارد. چدن سفید به سه دسته اصلی تقسیم میشود: چدنهای غیرآلیاژی، کمآلیاژ و پرآلیاژ. چدن غیرآلیاژی معمولاً دارای ساختار پرلیتی ریز است، اما با افزودن عناصری مانند کروم، نیکل و مولیبدن، میتوان ساختارهایی مانند مارتنزیتی یا آستنیتی ایجاد کرد. چدن پرآلیاژ دارای ۱۵ تا ۳۰ درصد کروم است که ویژگیهای خاصی را به آن میبخشد.
چدنهای سفید پرکرم به دلیل خواص ویژهای که ارائه میدهند، در کاربردهایی نظیر تجهیزات معادن شن و ماسه، تیغههای آسیاب، قطعات انتقال مواد، قطعات سنگ شکن و اجزای کورههای صنعتی به کار میروند. این آلیاژها مقاومت عالی در برابر اکسیداسیون و رشد در دماهای بالا دارند و به دلیل ساختار سخت و مستحکم خود، گزینهای ایدهآل برای شرایطی هستند که نیاز به مقاومت در برابر سایش و خوردگی است اما فشار ضربهای زیادی وجود ندارد.
مهندسین شرکت آوانگارد، فارغالتحصیلان دانشگاههای معتبر ایران و کانادا، با بیش از دو دهه تجربه در زمینه تولید و ریختهگری چدنهای سفید پرکرم، توانایی تولید انواع قطعات صنعتی را با کیفیت بالا و مطابق با استاندارد ASTM A532 دارند. این شرکت با تکیه بر تخصص تیم مهندسی خود در مهندسی معکوس و مدل سازی و طراحی مدلهای پیچیده، آماده ارائه بهترین محصولات به صنایع مختلف است. استفاده از مواد اولیه ریختگری با کیفیت و فناوری پیشرفته، تضمینکننده تولید قطعاتی با بالاترین مقاومت به سایش و خوردگی برای نیازهای خاص صنعتی است.
مقاومت به خوردگی چدن پر کروم
چدنهای پرکرم به دلیل ترکیب شیمیایی خاص و محتوای بالای کروم (12 تا 35 درصد) مقاومت بسیار خوبی در برابر خوردگی از خود نشان میدهند. این چدنها بهویژه در محیطهایی که اسیدهای اکسیدکننده حضور دارند، عملکرد قابل توجهی دارند، اما در برابر اسیدهای احیاکننده مقاومت چندانی ندارند. خواص ضد خوردگی این چدنها آنها را به گزینهای مناسب برای استفاده در محیطهای حاوی اسیدهای ضعیف در شرایط اکسیداسیون، محلولهای نمک، محلولهای اسیدهای آلی، و حتی شرایط اتمسفری عمومی تبدیل کرده است.
یکی از ویژگیهای برجسته چدنهای پرکرم، مقاومت استثنایی آنها در برابر اسید نیتریک (Nitric Acid) است. این چدنها میتوانند تمامی غلظتهای بالای 95 درصد اسید نیتریک را در دمای محیط تحمل کنند، بهطوری که میزان خوردگی آنها در سال کمتر از 0.12 میلیمتر است. این سطح از مقاومت حتی در دماهای نزدیک به نقطه جوش و غلظتهای تا 70 درصد نیز حفظ میشود، که نشاندهنده پایداری بالای ساختار این آلیاژ در شرایط سخت صنعتی است.
خواص ضد خوردگی چدنهای پرکرم عمدتاً به دلیل حضور فازهای کاربیدی و کروم در ساختار آلیاژ است. کروم در واکنش با اکسیژن محیط، یک لایه اکسیدی نازک و پایدار بر روی سطح آلیاژ تشکیل میدهد. این لایه، که به عنوان لایه غیرفعال (Passive Layer) شناخته میشود، مانع از نفوذ بیشتر عوامل خورنده به داخل آلیاژ شده و مقاومت به خوردگی را افزایش میدهد. این ویژگی بهویژه در محیطهای اسیدی با اکسیدکنندگی بالا اهمیت دارد.
چدنهای پرکروم در صنایع مختلفی از جمله شیمیایی، پتروشیمی، و فرآوری مواد معدنی کاربرد دارند. این چدنها به دلیل مقاومت بالا در برابر اسیدهای نیتریک و محلولهای نمکی، برای ساخت قطعاتی نظیر پمپها، لولهها، و مخازن ذخیرهسازی مواد شیمیایی مناسب هستند.
مقاومت به سایش چدن پر کروم
چدنهای سفید پرکروم به دلیل ترکیب شیمیایی خاص و ساختار متالورژیکی خود، از جمله مواد مقاوم به سایش با ویژگیهای برجسته در صنایع مختلف هستند. این چدنها معمولاً حاوی 12 تا 35 درصد کروم و 1.5 تا 3.5 درصد کربن هستند که باعث تشکیل کاربیدهای مقاوم به سایش مانند M₇C₃ و M₃C میشود. این کاربیدها، با توجه به نوع و مقدار کروم موجود، ویژگیهای منحصر به فردی را در برابر سایش ایجاد میکنند. چدنهای سفید پرکروم بهویژه در صنایع معدن، سیمان، فولادسازی و سایر بخشهای صنعتی که نیاز به مقاومت بالایی در برابر سایش دارند، کاربرد فراوانی دارند.
این چدنها معمولاً در دو رنج درصدی از کروم ساخته میشوند:
- چدنهای با 12 تا 15 درصد کروم، برای کاربردهایی که نیاز به مقاومت متوسط در برابر سایش دارند.
- چدنهای با 20 تا 30 درصد کروم، برای کاربردهایی که نیاز به مقاومت بسیار بالا در برابر سایش دارند.
این ترکیب شیمیایی باعث میشود که چدنهای سفید پرکروم در مقابل سایش شدید و شرایط سخت کاری عملکرد بسیار خوبی داشته باشند. این آلیاژها بهویژه در قطعاتی مانند لاینرها، پمپها و آسیابها که در معرض سایش مداوم هستند، مورد استفاده قرار میگیرند.
با این حال، یکی از چالشهای اصلی در استفاده از چدنهای سفید پرکروم، شکنندگی بالا و کاهش مقاومت به ضربه در این آلیاژها است. برای غلبه بر این مشکل، عملیات حرارتی خاصی مانند عملیات آستنیته کردن و آبکاری بهکار گرفته میشود تا ضمن حفظ خواص سایش، چقرمگی و مقاومت به ضربه افزایش یابد.
- عملیات حرارتی مناسب میتواند مقاومت به ضربه چدنهای سفید پرکروم را به طور چشمگیری بهبود بخشد.
- با استفاده از مبرد در فرآیند ریختهگری، سرعت انجماد را افزایش داده و بدون کاهش قابل توجه در مقاومت به سایش، مقاومت به ضربه نیز بهبود مییابد.
در نهایت، با استفاده از ترکیب مناسب کروم و سایر عناصر آلیاژی مانند مولیبدن، نیکل و مس، میتوان چدنهای سفید پرکروم با ویژگیهای بهینه برای شرایط مختلف کاری تولید کرد. این ویژگیها باعث شده است که این نوع چدنها یکی از پرکاربردترین مواد در صنایع مقاوم به سایش باشند.
تاریخچه پیدایش چدن
چدن به عنوان یکی از مهمترین آلیاژهای آهنی، دارای تاریخچهای غنی و جالب است که ریشههای آن به قرنها قبل بازمیگردد. نخستین شواهد باستانشناسی استفاده از چدن به قرن پنجم پیش از میلاد در چین باستان بازمیگردد. در آن زمان، چدن به دلیل ویژگیهای منحصر به فرد خود، بهویژه سختی و دوام بالا، در ساخت تجهیزات جنگی، ابزارهای کشاورزی، و حتی در طراحیهای معماری مورد استفاده قرار میگرفت.
در دوران قرون وسطی، استفاده از چدن به اروپا گسترش یافت. در قرن پانزدهم میلادی، صنعتگران بورگوندی در فرانسه از چدن برای تولید توپخانه بهره گرفتند. این کاربرد، نقطه عطفی در استفاده از فلزات برای مقاصد نظامی بود و باعث افزایش تقاضا برای چدن شد.
یکی از برجستهترین دستاوردهای تاریخی در استفاده از چدن، ساخت نخستین پل چدنی در جهان بود که در دهه 1770 میلادی توسط ابراهام داربی III در انگلستان طراحی و اجرا شد. این پل که به نام پل آهن (Iron Bridge) شهرت دارد، نمادی از انقلاب صنعتی و پیشرفت تکنولوژی متالورژی در آن زمان است. علاوه بر این، در قرنهای بعد، چدن بهطور گستردهای در ساخت ساختمانها و سازههای معماری استفاده شد و به یکی از مصالح کلیدی در صنعت ساختمانسازی تبدیل گردید.
تاریخچه چدن نشاندهنده تحول تدریجی دانش متالورژی و نوآوریهای صنعتی است. از ابزارهای ساده کشاورزی در چین باستان تا سازههای پیچیده و برجسته در دوران انقلاب صنعتی، این آلیاژ نقش مهمی در توسعه تمدن بشری ایفا کرده است.
چدن
چدن آلیاژی از آهن و کربن است که محتوای کربن آن بین 2.1 تا 6.2 درصد متغیر است. این آلیاژ به دلیل خواص ویژه خود در بسیاری از صنایع به کار میرود. ساختار و ویژگیهای چدن عمدتاً به درصد کربن و سیلیسیم موجود در آن بستگی دارد. بیش از 95 درصد وزنی این آلیاژ را آهن تشکیل میدهد، در حالی که کربن و سیلیسیم به عنوان عناصر آلیاژی اصلی، تأثیر مستقیم بر سختی، مقاومت و قابلیت ماشینکاری آن دارند. به طور معمول، چدن دارای رنج 2.1 تا 4 درصد عنصر کربن و حدود 1 تا 3 درصد عنصر سیلیسیم می باشد که این ترکیب آن را به آلیاژی سهگانه تبدیل میکند.
چدنها به انواع مختلفی مانند چدن خاکستری (Gray Cast Iron)، چدن داکتیل (Ductile Iron)، چدن سفید (White Cast Iron)، و سایر انواع تقسیمبندی میشوند. هر کدام از این انواع دارای ویژگیهای منحصربهفردی هستند که آنها را برای کاربردهای مختلف مناسب میکند که در مقاله چدن چیست؟ به طور کامل به انواع چدن پرداخته ایم. در این مقاله، تمرکز ما بر روی چدن سفید آلیاژی پرکروم است که یکی از پیشرفتهترین و مقاومترین انواع چدن محسوب میشود.
چدنهای سفید آلیاژی به دلیل ویژگیهای خاص خود، مانند مقاومت بسیار بالا در برابر سایش و سختی سطحی فوقالعاده، در بسیاری از صنایع جایگاه ویژهای دارند. در این گروه، عناصری مانند کروم و نیکل به آلیاژ اضافه میشوند تا خواص مکانیکی و فیزیکی آن را بهبود بخشند. چدنهای نایهارد و چدن پرکروم نمونههای بارزی از این گروه هستند که با ساختار میکروسکوپی مارتنزیتی شناخته میشوند. وجود این ساختار باعث میشود مقاومت سایشی بسیار بالایی داشته باشند و در برابر فرسایش عملکرد فوقالعادهای ارائه دهند. بهویژه در صنایعی که قطعات در تماس مداوم با مواد سخت یا ساینده هستند، استفاده از این نوع چدنها بسیار رایج است.
چدنهای آلیاژی به دلیل حضور کاربیدهای سخت کروم و نیکل، سختی سطحی بسیار بالایی دارند و میتوانند با عملیات حرارتی به درجه سختی حدود HRC 60 برسند. این ویژگیها آنها را برای کاربردهایی با سایش شدید، مانند آسترهای آسیاب، چکشهای کوبیت و تیغههای برش، ایدهآل میسازد. با این حال، به دلیل سختی بالا، مقاومت این آلیاژها در برابر ضربه پایین است و شکنندگی بیشتری نسبت به سایر آلیاژهای چدن دارند. همچنین، این آلیاژها قابلیت ماشینکاری محدودی دارند، که نیاز به دقت بالایی در فرایند تولید و شکلدهی قطعات از آنها را ایجاد میکند.
کاربردهای این چدنها بسیار گسترده است و در صنایعی مانند معدن، سیمان، نفت و گاز، و پتروشیمی به کار میروند. قطعاتی مانند ولوها، پمپها، تیغههای مقاوم به خوردگی و تجهیزات حرارتی از جمله محصولاتی هستند که از این آلیاژها تولید میشوند. ترکیب مقاومت به سایش، طول عمر بالا، و سختی سطحی فوقالعاده، چدنهای آلیاژی را به انتخابی برتر برای شرایط عملیاتی سخت تبدیل کرده است.
اگرچه چدنهای آلیاژی به دلیل ویژگیهای منحصربهفرد خود در بسیاری از صنایع جایگاه ویژهای دارند، اما تولید و استفاده از آنها نیازمند دانش فنی بالا و مواد اولیه با کیفیت است. انتخاب درصد مناسب از عناصر آلیاژی مانند کروم و نیکل، همراه با اجرای صحیح عملیات حرارتی، نقش کلیدی در دستیابی به خواص مکانیکی و فیزیکی مطلوب این آلیاژها دارد.
برای آشنایی بیشتر با ویژگیها و کاربردهای چدن سفید آلیاژی پرکروم و تأثیر آن در صنایع مختلف، با ما همراه باشید.
چدن سفید
چدن سفید پرکروم از زیر مجموعه های چدن سفید می باشد و همچنین چدن سفید به دلیل ساختار خاص و خواص مکانیکی برجسته، یکی از مهمترین زیرمجموعههای آلیاژهای آهنی محسوب میشود. چدن سفید از ترکیب آهن، سیلیسیم و کربن تشکیل میشود که در آن کربن عمدتاً بهصورت سمنتیت (Fe₃C) موجود است. ساختار چدن سفید بهگونهای است که در طی فرآیند سرد شدن، نواحی مختلفی بهوجود میآید که از ترکیب پرلیت و لدبوریت یوتکتیکی تشکیل شده است. این ساختار منحصر به فرد باعث میشود که چدن سفید دارای خواص مکانیکی خاصی نظیر سختی بالا و مقاومت سایشی فوقالعاده باشد.
چدن سفید بهطور کلی دارای خواص ویژهای است که آن را برای کاربردهایی با شرایط سایش و فشار زیاد مناسب میسازد. یکی از ویژگیهای برجسته این چدن، مقاومت بسیار بالای آن در برابر سایش است. ساختار سمنتیت موجود در چدن سفید باعث میشود که این آلیاژ در برابر سایشهای مکانیکی و شیمیایی بسیار مقاوم باشد. با این حال، چدن سفید بهدلیل ساختار کریستالی خود، معمولاً شکننده است و میتواند در برابر ضربههای شدید دچار ترک شود. این ویژگیهای خاص، باعث شده که استفاده از این چدن تنها در محیطهایی با شرایط ویژه و برای قطعات خاص محدود باشد.
برای بهبود خواص مکانیکی و کاهش شکنندگی، از روشهای مختلفی برای آلیاژی کردن چدن سفید استفاده میشود. افزودن عناصر آلیاژی مانند کروم، مولیبدن و نیکل به چدن سفید میتواند ساختار کاربیدها را تغییر دهد و خواص فیزیکی و مکانیکی آن را بهبود بخشد. بهویژه، افزودن کروم بهعنوان یک عنصر کاربیدساز موجب میشود که کاربیدهای موجود در چدن از نوع M₃C یا M₇C₃ تشکیل شوند. کاربیدهای M₇C₃ که در حضور کروم زیاد بهوجود میآیند، دارای سختی و مقاومت بالاتری نسبت به کاربیدهای M₃C هستند و باعث ایجاد ساختار ظریفتری در چدن میشوند که منجر به بهبود چقرمگی و کاهش شکنندگی میشود. این ویژگیها به چدن سفید آلیاژی امکان میدهند که در شرایط سایش شدید و در دماهای بالا عملکرد بهتری داشته باشد.
عوامل مختلفی مانند نوع کاربیدها، اندازه و شکل آنها، و ساختار زمینه بر ویژگیهای چدن سفید تأثیر میگذارند. نوع کاربیدها یکی از مهمترین عواملی است که بر خواص چدن سفید تأثیر دارد. بهطور معمول، کاربیدهای M₃C سختی کمتری نسبت به کاربیدهای M₇C₃ دارند و مقاومت سایشی آنها کمتر است. علاوه بر این، اندازه و شکل کاربیدها نیز میتواند بر خواص مکانیکی چدن سفید تأثیرگذار باشد. اندازه دانههای ریزتر و توزیع یکنواختتر کاربیدها باعث افزایش مقاومت به ضربه و بهبود خواص مکانیکی میشود.
در مورد ساختار زمینه، حضور زمینه مارتنزیتی برای دستیابی به بالاترین مقاومت سایشی ترجیح داده میشود. در هنگام سرد شدن سریع، آستنیت موجود در ساختار چدن سفید به مارتنزیت تبدیل میشود که باعث افزایش سختی و مقاومت سایشی این آلیاژ میشود. با این حال، در مواردی که نیاز به تحمل ضربات شدید وجود دارد، حضور مقداری آستنیت باقیمانده مجاز است. آستنیت باقیمانده در این موارد میتواند به چدن سفید اجازه دهد تا در برابر ضربات شدید مقاومت کند.
چدن سفید در صنعتهایی که نیاز به مقاومت سایشی و خوردگی دارند، کاربرد زیادی دارد. این آلیاژ معمولاً در تولید قطعات مقاوم به سایش نظیر دیسکهای ترمز، لوازم جانبی دستگاههای صنعتی و قطعات ماشینآلات سنگین استفاده میشود. در صنایع معدنی و سیمان و سنگ شکن و راهسازی ، این چدن به دلیل ویژگیهای ویژهای که دارد، برای ساخت قطعاتی که تحت سایش و فشار زیادی قرار میگیرند، بهکار میرود. استفاده از این چدن در محیطهایی با شرایط دما و فشار بالا نیز رایج است.
یکی از مشکلات اصلی چدن سفید، چقرمگی پایین آن است که به دلیل شبکه کاربید آهن (Fe₃C) در ساختار آن ایجاد میشود. با این حال، افزودن عناصر آلیاژی مناسب میتواند خواص مکانیکی چدن سفید را بهبود دهد. بهویژه افزودن کروم به چدن سفید باعث افزایش سختی، مقاومت در برابر سایش و بهبود چقرمگی میشود. از دیگر عناصر آلیاژی که میتوانند ویژگیهای چدن سفید را بهبود بخشند، میتوان به مولیبدن، نیکل و مس اشاره کرد.
در نهایت، شرکت آوانگارد با استفاده از تکنولوژیهای پیشرفته و تیم متخصص در زمینه ریختهگری و آلیاژسازی، که بعنوان بهترین ریخته گری در تهران و ایران شناخته می شود، قادر به تولید چدن سفید با ویژگیهای بهینه برای کاربردهای مختلف در صنایع گوناگون می باشد. این محصولات با بالاترین استانداردهای کیفی تولید میشوند و میتوانند نیازهای صنایع مختلف را در زمینه مقاومت سایشی و خوردگی برطرف کنند.
چدنهای آلیاژی (Alloy Cast Iron)
چدنهای آلیاژی به گروهی از چدنها اطلاق میشوند که در ترکیب شیمیایی خود، عناصری مانند کروم (Cr)، نیکل (Ni)، مولیبدن (Mo)، سیلیسیم (Si) و منگنز (Mn) دارند که باعث بهبود خواص فیزیکی و شیمیایی این آلیاژها میشود. این چدنها به دلیل خواص ویژهای که دارند، به طور گسترده در صنایع مختلف بهویژه در صنایع خودرو، سیمان، معدن، شیمیایی و فولادسازی کاربرد دارند.
چدنهای آلیاژی به دلیل داشتن خواص مقاومتی در برابر سایش، خوردگی و حرارت، در مقایسه با فولادهای آلیاژی و دیگر مواد فلزی، گزینه مناسبی برای استفاده در شرایط سخت صنعتی هستند. علاوه بر این، این چدنها در مقایسه با فولادهای آلیاژی از قیمت پایینتری برخوردار هستند و فرآیند ریختهگری آنها سادهتر است که در این خصوص پیشنهاد مطالعه مقاله شباهت ها و تفاوت ها در ریخته گری فولاد و چدن را داریم.
آنالیز گرید های مختلف چدن مقاوم به سایش Astm A532
Chemical composition, max(unless range is given)% | ||||||||||||
Hardness max, HB | Cu | Mo | Cr | Ni | P | S | Mn | Si | C | Grade or class | Specification | |
550min | 1 | 1.4-4.0 | 3.3-5.0 | 0.3 | 0.15 | 2 | 0.8 | 2.80-3.60 | I-A | Abrasion Resistant Iron | ASTM A532 | |
550min | 1 | 1.4-4.0 | 3.3-5.0 | 0.3 | 0.15 | 2 | 0.8 | 2.40-3.00 | I-B | |||
550min | 1 | 1.0-2.5 | 4 | 0.3 | 0.15 | 2 | 0.8 | 2.50-3.70 | I-C | |||
500min | 1.5 | 7.0-11.0 | 4.5-7.0 | 0.1 | 0.15 | 2 | 2 | 2.50-3.60 | I-D | |||
550min | 1.2 | 3 | 11.0-14.0 | 2.5 | 0.1 | 0.06 | 2 | 1.5 | 2.00-3.30 | II-A | ||
450min | 1.2 | 3 | 14.0-18.0 | 2.5 | 0.1 | 0.06 | 2 | 1.5 | 2.00-3.30 | II-B | ||
450min | 1.2 | 3 | 18.0-23.0 | 2.5 | 0.1 | 0.06 | 2 | 1.5 | 2.00-3.30 | II-D | ||
450min | 1.2 | 3 | 23.0-30.0 | 2.5 | 0.1 | 0.06 | 2 | 1.5 | 2.00-3.30 | III-A |
چدنهای آلیاژی مقاوم به سایش (Wear-Resistant Cast Irons)
این نوع چدنها به دلیل ترکیب شیمیایی خاص و سطح سخت شده، مقاومت بالایی در برابر سایش و فرسایش دارند. یکی از مشهورترین انواع این چدنها، چدن های کروم دار هستند که معمولا دارای 12 تا 35 درصد کروم هستند. ترکیب کروم بالا در این چدنها باعث افزایش سختی و کاهش مقاومت در برابر سایش میشود.
چدنهای کروم دار مقاوم به سایش (High Chromium Wear-Resistant Cast Irons): این چدنها حاوی 12-30درصد کروم و 4-2 درصد کربن هستند. این ترکیب باعث میشود که چدنها در برابر سایش شدید مقاومت زیادی از خود نشان دهند. این نوع چدنها به طور گسترده در صنایع مختلف مانند تولید آسیابها، زرههای آسیاب، پمپهای ضد سایش، بوشها و سیلندرها کاربرد دارند.
چدنهای نیکل سخت یا چدن نایهارد: (Ni-Hard Cast Irons) ترکیبی از مقاومت و کارایی در شرایط سخت
چدنهای نیکل سخت، که با نام تجاری Ni-Hard نیز شناخته میشوند، از جمله چدنهای آلیاژی مقاوم به سایش هستند که با ترکیب عناصری مانند نیکل (Nickel) و کروم (Chromium) تولید میشوند. این چدنها معمولاً حاوی 4 تا 6 درصد نیکل و 9 درصد کروم هستند و با استفاده از عملیات حرارتی خاص، ویژگیهای مکانیکی آنها بهبود مییابد و مقاومت آنها در برابر سایش و ضربه بهطور چشمگیری افزایش مییابد. این ویژگیها باعث شده است که چدنهای نیکل سخت در صنایعی که نیاز به مقاومت در برابر سایش و ضربههای شدید دارند، مانند تولید قطعات آسیابها، سنگشکنها و تجهیزات صنعتی، بهطور گستردهای مورد استفاده قرار گیرند.
ترکیب شیمیایی چدنهای نیکل سخت به گونهای طراحی میشود که ساختار اصلی آنها بهطور عمده از ترکیب یوتکتیک و آستنیت جامد تشکیل میشود. فازهای کاربیدی که در این چدنها وجود دارند، نقش مهمی در افزایش مقاومت آنها به سایش دارند. مقدار کاربید یوتکتیک و ساختار زمینه به ترکیب شیمیایی چدن بستگی دارد. این کاربیدها در برابر سایش و ضربه مقاومت زیادی از خود نشان میدهند و بهویژه در کاربردهایی که قطعات تحت بارهای شدید قرار دارند، عملکرد مطلوبی از خود نشان میدهند.
چدن نیکل سخت نوع ۲ دارای ساختار لدبوریتی است که در آن کاربید M₃C بهصورت پیوسته در ریزساختار حضور دارد. این ساختار باعث میشود که چدن نوع ۲ چقرمگی کمتری داشته باشد و در کاربردهایی که تحت بارهای ضربهای و سایش شدید قرار میگیرند، ممکن است مقاومت کمتری از خود نشان دهد. در مقابل، چدن نیکل سخت نوع ۴ دارای ساختار یوتکتیکی است که در آن کاربیدهای نوع M₇C₃ بهطور ناپیوسته در ساختار حضور دارند. این نوع ساختار به دلیل ویژگیهای خاص خود، از جمله مقاومت بیشتر در برابر شکست، در بسیاری از کاربردهای صنعتی ترجیح داده میشود.
مزیت ساختار کاربیدی ناپیوسته در چدنهای نیکل سخت نوع ۴ این است که با وجود ترد بودن کاربید M₇C₃، ترکهای ایجاد شده در آن بهطور مؤثری پیش از آنکه به بخشهای نرمتر زمینه نفوذ کنند، متوقف میشوند. این ویژگی باعث میشود که چدن نیکل سخت نوع ۴ نسبت به چدنهای نیکل سخت نوع ۲ مقاومت بیشتری در برابر شکست داشته باشد. به همین دلیل، چدنهای نیکل سخت نوع ۴ در کاربردهایی که نیاز به مقاومت بالا در برابر سایش و ضربههای مکرر دارند، گزینهای مناسبتر به شمار میآیند.
ترکیب شیمیایی چدنهای نیکل سخت نقش حیاتی در تشکیل نوع خاصی از کاربیدها ایفا میکند. بهعنوان مثال، زمانی که مقدار Si بهعلاوه 0.3درصد Cr از 4.1درصد بیشتر شود، کاربیدهای ناپیوسته M₇C₃ بهجای کاربیدهای لدبوریتی M₃C تشکیل میشوند. این تغییرات در ترکیب شیمیایی باعث بهبود ویژگیهای مکانیکی و مقاومت به سایش چدن نیکل سخت میشود و به آنها اجازه میدهد که در شرایط سختتری بهخوبی عمل کنند.
در نهایت، چدنهای نیکل سخت به دلیل ویژگیهای منحصر به فرد ساختار کاربیدی و مقاومت بالا در برابر سایش و ضربه، در صنایع مختلفی مانند آسیابهای سیمان، سنگشکنها و تجهیزات فلزکاری بهطور گستردهای استفاده میشوند. انتخاب نوع مناسب چدن نیکل سخت (نوع ۲ یا ۴) بستگی به نیازهای خاص کاربرد و شرایط عملیاتی دارد.
ویژگیها و خواص چدنهای نیکل سخت
- مقاومت در برابر سایش و ضربه:
چدنهای Ni-Hard به دلیل وجود کاربیدهای سخت مانند M₃C و M₇C₃ در ساختارشان، در برابر سایش و ضربات مکرر بسیار مقاوم هستند. - دو نوع اصلی چدن نیکل سخت:
- Ni-Hard I :حاوی 4-5 درصد نیکل، مناسب برای کاربردهایی با نیاز به سختی بالا.
- Ni-Hard II : حاوی بیش از 5 درصد نیکل و کروم بالاتر، با چقرمگی بیشتر و مناسب برای شرایط سختتر.
کاربردهای چدنهای نیکل سخت
چدنهای نیکل سخت به دلیل مقاومت بالا در برابر سایش و قابلیت تحمل شرایط کاری سخت، در صنایع مختلفی استفاده میشوند:
- صنایع سیمان:
- تولید گلولههای آسیاب (Grinding Balls)
- جدارههای پوستهای آسیابهای سیمان (Mill Liners)
- صنایع معدنی و فلزی:
- قطعات سنگشکنهای ضربهای (Impact Crusher Parts)
- غلطکهای فلزکاری (Metal Rolling Rolls)
- صنایع حمل و نقل مواد:
- قطعات مورد استفاده در تجهیزات نورد و حمل مواد در نوار نقاله.
مقایسه چدنهای نیکل سخت و چدنهای پر کروم
چدنهای نیکل سخت 4 (Ni-Hard 4) و چدنهای پر کروم هر دو در شرایط سخت صنعتی عملکرد بالایی دارند، اما تفاوتهایی در ویژگیها و کاربردهای آنها وجود دارد:
- چدنهای Ni-Hard 4:
- ساختاری با کاربیدهای ناپیوسته M₇C₃، که چقرمگی بیشتری نسبت به نوع Ni-Hard 2 دارند.
- مناسب برای کاربردهایی که نیاز به سختیپذیری بالا دارند.
- چدنهای پر کروم:
- مقاومت شکست بالاتر، که آنها را برای شرایطی با ضربات سنگینتر مناسبتر میکند.
مزایای چدنهای نیکل سخت
- قابلیت سختیپذیری بالا: این ویژگی امکان استفاده از این چدنها را در قطعاتی که نیاز به سختی سطحی بالا و مقاومت در برابر سایش دارند، فراهم میکند.
- عملکرد بهینه در شرایط سایش و ضربه: این چدنها در صنایعی مانند سیمان و معادن که قطعات تحت سایش و ضربههای مکرر قرار میگیرند، انتخابی ایدهآل هستند.
چدنهای نیکل سخت به دلیل ویژگیهای منحصربهفردشان، همچنان یکی از پرکاربردترین مواد در صنایع سنگین و شرایط کاری دشوار هستند و نقش مهمی در بهبود عملکرد و کاهش هزینههای نگهداری تجهیزات صنعتی ایفا میکنند که در مقاله چدن نیکل سخت یا چدن نایهارد به طور کامل به این نوع چدن آلیاژی پرداخته ایم.
چدنهای مقاوم به خوردگی با کروم بالا (High Chromium Corrosion-Resistant Cast Irons)
چدنهای پر کروم که معمولاً دارای درصد کروم بین 20 تا 35 درصد هستند، به دلیل ویژگیهای مقاومتی بالای خود در برابر خوردگی و سایش، در صنایع مختلف کاربرد گستردهای دارند. این چدنها به ویژه در محیطهایی که در معرض اسیدهای اکسیدکننده مانند اسید نیتریک و شرایط خورندگی شیمیایی قرار دارند، به دلیل مقاومت بالا در برابر خوردگی، مورد استفاده قرار میگیرند. ویژگی مهم این چدنها این است که به طور خاص در برابر اسیدهای ضعیف، محلولهای نمک، اسیدهای آلی و در شرایط عمومی اتمسفری عملکرد خوبی دارند. در این ترکیبها، کروم نقش اصلی را در افزایش مقاومت به خوردگی ایفا میکند و باعث بهبود دوام قطعات در برابر خوردگی و سایش میشود.
چدنهای پر کروم معمولاً در صنایع خاصی که نیاز به مقاومت در برابر خوردگی و دماهای بالا دارند، به کار میروند. برای مثال، این چدنها معمولاً برای استفاده در دیگهای آنیلینگ سرب، روی و آلومینیوم، زنجیرهای انتقالدهنده و دیگر قطعاتی که در معرض خوردگی و دماهای بالا قرار دارند، استفاده میشوند. این چدنها به دلیل ویژگیهای مقاومتی خود در برابر اسیدهای سولفوریک و فسفریک، به ویژه در غلظتهای بالا و در دماهای مختلف عملکرد بسیار خوبی دارند.
چدنهای پر کروم با کروم 30 تا 35 درصد به طور خاص برای استفاده در محیطهای با خوردگی شدید طراحی شدهاند. این چدنها در برابر تمام غلظتهای اسیدهای سولفوریک، حتی در دماهای بالا، مقاومت مفیدی دارند. به طور خاص، این چدنها در برابر اسیدهای سولفوریک در دماهای تا 80 درجه سانتیگراد، محلولهای سولفیت در کارخانههای کاغذسازی، محلولهای سفیدکننده در دماهای محیطی و همچنین سولفات آلومینیوم سرد در غلظتهای تا 5 درصد مقاومت خوبی از خود نشان میدهند. علاوه بر این، این چدنها در برابر اسید فسفریک در غلظتهای 60 درصد و دماهای بالا تا نقطه جوش و همچنین در برابر غلظتهای 85 درصد اسید فسفریک در دماهای تا 80 درجه سانتیگراد مقاوم هستند.
چدنهای پر کروم همچنین در برابر آب دریا و آبهای معدنی که حاوی محلولهای اسیدی هستند، مقاومت خوبی دارند. این چدنها به دلیل ترکیب مناسب کروم و کربن، خواص مکانیکی بهتری نسبت به چدنهای پر سیلیس دارند و زمانی که مقدار کروم و کربن به طور بهینه بالانس شوند، به راحتی میتوانند عملیات حرارتی شوند. چدنهای پر کروم با درصد کروم بالا، به ویژه در شرایط محیطی با خوردگی شدید، عملکرد بهتری دارند و به دلیل مقاومت بالای خود در برابر خوردگی و سایش، در صنایعی مانند صنایع شیمیایی، ساخت تجهیزات ضد خوردگی، دیگهای آنیلینگ و قطعاتی که در معرض دماهای بالا و خوردگی قرار دارند، به طور گسترده استفاده میشوند.
این چدنها در دماهای بالا و در شرایطی که نیاز به مقاومت در برابر اسیدهای خورنده و سایشهای شدید وجود دارد، بهترین عملکرد را از خود نشان میدهند و به همین دلیل در بسیاری از صنایع حساس، از جمله صنایع شیمیایی و پتروشیمی، کاربرد فراوانی دارند.
چدنهای مقاوم به خوردگی با سیلیسیم بالا (High Silicon Corrosion-Resistant Cast Irons)
چدنهای پر سیلیسیم، که حاوی حدود 14 الی 17 درصد عنصر سیلیسیم هستند، بهویژه به دلیل ویژگیهای منحصر به فرد عنصر سیلیسیم در افزایش مقاومت به خوردگی و تحمل دماهای بالا شناخته میشوند. سیلیسیم در این چدنها نه تنها از تشکیل کاربیدهای سخت جلوگیری میکند، بلکه باعث بهبود مقاومت آنها در برابر اسیدهای خورنده مانند اسیدهای نیتریک و سولفوریک میشود. این ویژگیها باعث شدهاند که چدنهای پر سیلیسیم در صنایعی که نیاز به مقاومت بالا در برابر شرایط خورنده دارند، بهطور گستردهای استفاده شوند.
چدنهای پر سیلیسیم و مولیبدن دار که در محدوده تا 3.5 درصد مولیبدن در الیاژ خود به همراه دارند، در بسیاری از کاربردهای صنعتی برای حمل اسیدهای خورنده مورد استفاده قرار میگیرند. این چدنها، بهویژه با مقدار سیلیسیم 14.5 درصد یا بیشتر، مقاومت بالایی در برابر اسید سولفوریک یک گرم 30 درصد پیدا میکنند. افزایش مقدار سیلیسیم تا 16.5 درصد در چدنهای خاکستری، بهطور قابل توجهی مقاومت این چدنها را در برابر خوردگی ناشی از اسیدهای سولفوریک و نیتریک افزایش میدهد و این مقاومت در تمام غلظتهای این اسیدها موثر است.
چدنهای خاکستری با 14 درصد سیلیسیم در برابر اسید کلریدریک مقاومت کمتری دارند، اما میتوان با افزودن 3.5 درصد مولیبدن، این مقاومت را بهبود بخشید. همچنین، با افزایش مقدار سیلیسیم تا 17 درصد، مقاومت در برابر خوردگی در برابر این نوع اسیدها نیز افزایش مییابد. این چدنها بهویژه در تماس با محلولهای حاوی نمک مس یا گاز مرطوب کلرین، مقاومت قابل توجهی از خود نشان میدهند و در برابر اسیدهای آلی نیز در تمامی غلظتها و دماها مقاوم هستند.
با این حال، چدنهای پر سیلیسیم دارای خواص مکانیکی ضعیفی هستند و بهویژه در برابر شوکهای مکانیکی و حرارتی مقاومت کمی دارند. ریختهگری این چدنها دشوار است و قابلیت ماشینکاری و برادهبرداری کمی دارند. علیرغم این محدودیتها، استفاده عمده این چدنها به دلیل مقاومت برجستهشان در برابر اسیدها است. این چدنها بهطور گستردهای در لولهکشیهای کارخانههای شیمیایی و آزمایشگاهها برای انتقال مواد خورنده بهکار میروند.
- کاربردها: این چدنها بهویژه در صنایع پتروشیمی، تولید اسید سولفوریک و نیتریک، و صنایع مواد منفجره کاربرد دارند.
چدنهای آستنیتی (Austenitic Cast Irons)
چدنهای آوستینیتی به عنوان یکی از انواع چدنهای آلیاژی، به دلیل ویژگیهای خاص خود در برابر خوردگی و خواص مکانیکی، کاربرد گستردهای در صنایع مختلف دارند. این چدنها به شدت به ترکیب شیمیایی خود وابسته هستند و رعایت دقیق مقادیر عناصر در محدودههای تعیین شده از اهمیت بالایی برخوردار است. بهویژه سیلیسیم در این آلیاژها نقش کلیدی دارد، چرا که از تشکیل کاربیدها جلوگیری کرده و باعث رسوب گرافیت میشود. به همین دلیل، باید مقدار سیلیسیم را در حد مجاز استاندارد به بالاترین حد ممکن رساند تا خواص مطلوب چدن آوستینیتی حاصل شود.
نوع کاربید موجود در این چدنها تأثیر مهمی بر خواص ریختهگری دارد. تشکیل کاربید نشاندهنده کاهش رسوب گرافیت در هنگام انجماد است که در نتیجه آن، انبساط چدن در قالب کمتر میشود. از سوی دیگر، کاربیدهای یوتکتیک کروم که در مراحل انتهایی انجماد تشکیل میشوند، نمیتوانند بهخوبی تغذیه شوند و این امر منجر به ایجاد خلل و فرج و انقباضهای بین دندریتی در قطعه میشود. بنابراین، از نظر انقباض ناشی از انجماد، بهتر است که میزان کاربیدها حداقل باشد. همچنین، در بیشتر چدنهای آوستینیتی، کروم وجود دارد که تشکیل کاربیدهای کروم را به دنبال دارد. کروم در این آلیاژها بهویژه برای افزایش مقاومت در برابر خوردگی و اکسید شدن استفاده میشود و در برخی موارد، برای بهبود مقاومت سایشی، میزان کروم به بیش از 3 درصد افزایش مییابد.
عوامل مؤثر در ریختهگری قطعات چدن آوستینیتی
ریختهگری بدون عیب قطعات چدن آوستینیتی علاوه بر اینکه به روشهای راهگاهی و تغذیهگذاری بستگی دارد، به عوامل دیگری نیز وابسته است که برخی از آنها با یکدیگر ارتباط دارند. این عوامل شامل اندازه قطعه ریختگی، استحکام قالب، ترکیب شیمیایی، درجه حرارت ریختن و جوانهزایی میشوند. در این بین، باید توجه کرد که چدنهای نوع آوستینیتی با گرافیت نوع ورقهای از نظر خصوصیات انقباضی و سایر ویژگیهای ریختگری شباهت زیادی به چدنهای خاکستری ندارند. بهطور خاص، این چدنها به دلیل ویژگیهای خاص خود در هنگام انجماد و تشکیل ساختار گرافیتی، نیاز به کنترل دقیق در فرآیند ریختهگری دارند تا از بروز مشکلاتی مانند انقباضهای غیرعادی یا عیوب سطحی جلوگیری شود.
کاربرد قطعات چدن آستینیتی
چدنهای آوستینیتی به دلیل ویژگیهای خاص خود در برابر خوردگی و مقاومت در دماهای بالا، در بسیاری از صنایع کاربرد دارند. این آلیاژها برای تولید قطعاتی که باید در محیطهای گوناگون در برابر خوردگی و پوستهشدن مقاوم باشند، بسیار مناسب هستند. از جمله کاربردهای اصلی این چدنها میتوان به تولید رینگ پیستونهای موتورهای دیزلی، پمپها و شیرهای مورد استفاده در صنایع نمکزدایی، شیمیایی و نفتی اشاره کرد. همچنین این چدنها در صنایع مختلفی که با مایعات خورنده سروکار دارند، مانند صنایع کشاورزی و تصفیه آب، کاربرد دارند.
چدنهای آوستینیتی بهویژه در دماهای بالا تا 800 درجه سانتیگراد مقاومت خوبی از خود نشان میدهند و در شرایطی که نیاز به مقاومت در برابر خزش و رشد در دماهای بالا باشد، استفاده میشوند. این آلیاژها همچنین در تولید توربو شارژرها، لولههای اگزوز، شیرهای مقاوم در برابر دماهای بالا، کمپرسورها، کلیدهای الکتریکی و پروانههای کشتیها نیز کاربرد دارند. یکی از مهمترین ویژگیهای این چدنها مقاومت آنها در برابر خوردگی در آب دریا است که باعث افزایش استفاده از این آلیاژها در صنایع دریایی و دیگر صنایع بهویژه در صنایع نفت و گاز، و کشتیسازی میشود.
چدنهای نسوز (Heat-Resistant Cast Irons)
چدنهای نسوز به گروهی از چدنها اطلاق میشوند که در برابر دماهای بالا و شرایط حرارتی شدید مقاومت دارند. این چدنها با افزودن عناصر آلیاژی مانند کروم، سیلیسیم و نیکل به آلیاژ خود، خواص نسوز را به دست میآورند.
- چدن نسوز پر کروم: این چدنها دارای حدود 20 درصد کروم هستند و میتوانند تا دمای 1000 درجه سانتیگراد را تحمل کنند.
- چدن نسوز با سیلیسیم بالا: چدنهایی با 5.5 تا 6 درصد سیلیسیم که معمولاً در دماهای بالاتر از 900 درجه سانتیگراد استفاده میشوند.
- چدن نسوز نیکروسیلال: (Ni-Si) این چدنها دارای نیکل و سیلیسیم بالا هستند و برای شرایطی که در معرض گازهای گوگردی قرار دارند، مناسب هستند.
این چدنها در صنایع فلزی و شیمیایی که نیاز به مقاومت در برابر حرارتهای بالا دارند، بهطور گستردهای مورد استفاده قرار میگیرند.
چدن سفید آلیاژی پرکروم
چدن سفید آلیاژی پرکروم (High Chromium White Cast Iron) یکی از پرکاربردترین انواع چدنهای سفید است که مقاومت فوقالعادهای در برابر سایش (Wear Resistance) و خوردگی (Corrosion Resistance) ارائه میدهد. این ویژگیها آن را برای استفاده در صنایع معدن، صنایع شن و ماسه، سیمان و پتروشیمی و ... مناسب کرده است. طبق استاندارد بینالمللی ASTM A532، این چدنها به دو کلاس اصلی II و III تقسیم میشوند که هر کدام خصوصیات و کاربردهای خاص خود را دارند.
تقسیمبندی چدن سفید آلیاژی پرکروم طبق استاندارد ASTM A532
کلاس II
این کلاس شامل پنج تیپ آلیاژی A، B، C، D و E است:
- تیپ :A حاوی حدود 12% کروم، مناسب برای کاربردهای عمومی با مقاومت سایشی متوسط.
- تیپ B و C
- تیپ B دارای 15% کروم با کربن پایین (Low Carbon)، مناسب برای شرایطی که مقاومت به ضربه اهمیت دارد.
- تیپ C با کربن بالا (High Carbon) و مقاومت سایشی بیشتر.
- تیپ D و: E دارای 20% عنصرکرم و تفاوت در مقدار کربن آنها.
- تیپ D با کربن پایینتر، چقرمگی بیشتری ارائه میدهد.
- تیپ E با کربن بالا، سختی بیشتری دارد.
کلاس III
این کلاس شامل آلیاژهایی با حدود 25% کروم است که مقاومت بسیار بالایی به سایش و خوردگی دارند و در محیطهای شدیداً خورنده، مانند صنایع شیمیایی و فرآوری مواد معدنی، به کار میروند.
ساختار متالورژیکی چدن سفید آلیاژی پرکروم
چدن سفید آلیاژی پرکروم شامل کاربیدهای کروم (Chromium Carbides) سخت است که در ماتریسی از مارتنزیت (Martensite) یا آستنیت (Austenite) قرار دارند. این ساختار باعث میشود:
- مقاومت سایشی و طول عمر قطعات افزایش یابد.
- قطعات در دماهای بالا عملکرد پایدارتری داشته باشند.
کاربردهای چدن سفید آلیاژی پرکروم
چدنهای مقاوم در مقابل سایش (Wear-Resistant Cast Irons) به دلیل خواص مکانیکی منحصربهفرد و مقاومت بالا در برابر سایش و خوردگی، در صنایع مختلف کاربرد گستردهای دارند. این نوع چدنها به دلیل حضور عناصری مانند کروم (Chromium) و مولیبدن (Molybdenum)، دارای ساختاری مستحکم و مقاوم هستند که آنها را برای استفاده در شرایط سخت عملیاتی ایدهآل میکند.
کاربردهای اصلی چدنهای مقاوم در برابر سایش
- تولید قطعات خودرو و ماشینآلات سنگین:
- بوشها (Bushings)
- سیلندرها (Cylinders)
- بوش سیلندرها (Cylinder Liners)
- کاسه چرخ (Brake Drums)
- صنایع ماشین و قالب
- لوازم یدکی و تجهیزات صنعتی خردایش:
- قطعات سنگشکنهای هیدروکن (Hydrocone Crusher Parts)
- قطعات سنگشکنهای فکی (Jaw Crusher Parts)
- لوازم یدکی سنگ شکن و تجهیزات سنگین معدنی و صنعتی
- صنایع معدنی و فرآوری مواد:
- ساخت گلولهها و زره آسیابها (Grinding Media and Mill Liners)
- تولید قالبهای حدیده برای کشش سیم (Wire Drawing Dies)
- غلطکهای نوار نقاله (Conveyor Rollers)
- پمپهای ضد سایش (Abrasion-Resistant Pumps)
- صنایع معدن و سیمان:
- تولید قطعاتی مانند قطعات آسترهای آسیاب ، سندان ها، قطعات ماسه ساز ، چکشها، بویژه چکش کوبیت بهرینگرHS10 ، چکش کوبیت بهرینگرHS14 ، چکش کوبیت بهرینگرHS11 ، چکش کوبیت بهرینگرHS7
- صنایع نفت و گاز:
- ساخت پمپها و ولوهای مقاوم به خوردگی.
- صنایع پتروشیمی: تولید قطعات مقاوم به حرارت و محیطهای خورنده.
مزایای چدن سفید آلیاژی پرکروم
- طول عمر بالا: مقاومت این چدنها در برابر سایش و خوردگی باعث کاهش هزینههای تعمیر و نگهداری میشود.
- عملکرد بهینه در شرایط سخت: این مواد در محیطهای پرتنش مانند معادن و صنایع فولاد عملکرد عالی دارند.
- مقاومت در برابر حرارت: ترکیب آلیاژی خاص این چدنها، آنها را برای کاربردهای دمای بالا مناسب میسازد.
- کاربردهای متنوع: از تجهیزات معدنی و قطعات ناخن و زیربندی تا صنایع شیمیایی.
این ویژگیها و کاربردها باعث شده است که چدنهای مقاوم در برابر سایش یکی از پرکاربردترین مواد در صنایع سنگین و ماشینآلات صنعتی باشند.
چدن ضد سایش پر کروم
چدنهای سفید پر کروم (High Chromium White Cast Iron) به دلیل مقاومت بالای خود در برابر سایش و خوردگی، در صنایع مختلف کاربرد گستردهای دارند. این نوع آلیاژهای چدن کروم بالا یا چدن سفید کروم بالا حدود12 الی 34 درصد عنصر کروم و 1.5 الی3.5 درصد کربن می باشند که حضور کرم بالا منجر به تشکیل کاربیدهای کروم (M₇C₃) در ساختار میکروسکوپی آنها میگردد.
کاربیدهای کروم بهصورت شبکههای پیوسته در اطراف دانههای آستنیت تشکیل میشوند که این ساختار میتواند منجر به تردی و ترکخوردگی شود. با این حال، با تنظیم دقیق ترکیب شیمیایی و عملیات حرارتی مناسب، میتوان تعادلی بین مقاومت به سایش و چقرمگی ایجاد کرد. بهعنوان مثال، کاهش محتوای کربن زمینه و افزودن عناصر آلیاژی مناسب میتواند به بهبود همزمان چقرمگی و مقاومت سایشی چدن ضد سایش پر کروم منجر شود.
در کاربردهایی مانند خردکنندهها و آسیابها، قطعات باید علاوه بر مقاومت در برابر سایش، توانایی تحمل تنشهای دینامیکی را نیز داشته باشند تا از شکستهای ناگهانی جلوگیری شود. انتخاب ترکیب شیمیایی مناسب و انجام عملیات حرارتی بهینه، نقش مهمی در دستیابی به این خواص ایفا میکند. بهعنوان مثال، حضور کروم در ترکیب چدنهای سفید پر کروم، علاوه بر افزایش مقاومت به سایش، مقاومت در برابر خوردگی را نیز بهبود میبخشد.
ساختار میکروسکوپی این چدنها شامل کاربیدهای آهن-کروم یوتکتیک ناپیوسته و کاربیدهای ثانویه غنی از کروم در زمینهای از آستنیت یا محصولات استحاله آن است. با استفاده از عملیات حرارتی میتوان به ساختارهای مختلفی مانند آستنیتی، مارتنزیتی، بینیتی یا پرلیتی دست یافت که هر یک خواص مکانیکی و فیزیکی متفاوتی را ارائه میدهند.
در نتیجه، چدنهای سفید پر کروم با ترکیب شیمیایی مناسب و عملیات حرارتی بهینه، گزینهای ایدهآل برای کاربردهایی هستند که نیاز به مقاومت بالا در برابر سایش و خوردگی همراه با چقرمگی مناسب دارند.
ساختار میکروسکوپی چدن ضد سایش پر کروم
چدنهای ضد سایش پر کروم (High Chromium Wear-Resistant Cast Irons) به دلیل ساختار میکروسکوپی خاص خود، مقاومت بالایی در برابر سایش دارند. این ساختار شامل کاربیدهای یوتکتیک M₇C₃ (کاربیدهای آهن-کروم) است که در زمینهای از آستنیت یا محصولات استحالهای آن توزیع شدهاند.
در فرآیندهای سایشی، ذرات سخت به سطح فلز نفوذ کرده و با ایجاد خراشها و تغییر شکلها، ذراتی را از سطح جدا میکنند. برای مقابله با این سایش، ضروری است که ساختار فلز حاوی فازهای سختی باشد که بتوانند در برابر نفوذ ذرات ساینده مقاومت کنند. در چدنهای پر کروم، حضور کاربیدهای M₇C₃ با سختی بالا، این مقاومت را فراهم میکند.
انتخاب زمینه مناسب در این چدنها بسیار حائز اهمیت است. زمینه مارتنزیتی پرکربن و سخت، به دلیل حضور کاربیدهای ثانویه پراکنده، مقاومت سایشی بالایی را ارائه میدهد. همچنین، آستنیت ناپایدار با قابلیت کارسختی (Work Hardening) میتواند گزینه مناسبی باشد. در چدنهای سفید پر کروم، کاربیدها در زمینه پراکنده شدهاند که این برخلاف ساختار لدبوریتی در چدنهای سفید کم آلیاژ است.
مقدار کربن در ترکیب شیمیایی این چدنها نقش مهمی در تعیین حجم کاربیدها و در نتیجه مقاومت سایشی دارد. افزایش کربن تا حد یوتکتیک، حجم کاربیدها را افزایش داده و مقاومت سایشی را بهبود میبخشد. با این حال، افزایش بیش از حد کربن (هیپریوتکتیک) میتواند منجر به تشکیل کاربیدهای اولیه ترد شود که تحت تأثیر ضربههای مکانیکی، شکست خورده و باعث کاهش مقاومت سایشی و چقرمگی میشوند.
زمینههای نرمتر، مانند پرلیت، مقاومت سایشی کمتری دارند و تمایل کاربیدها به جدا شدن از زمینه را افزایش میدهند. این امر میتواند منجر به کاهش استحکام تسلیم و عدم پشتیبانی کافی از کاربیدها در برابر تنشهای مکانیکی شود. بنابراین، کنترل ترکیب شیمیایی و عملیات حرارتی مناسب برای دستیابی به ساختار میکروسکوپی بهینه، جهت بهبود همزمان مقاومت سایشی و چقرمگی در چدنهای ضد سایش پر کروم، ضروری است.
ذوب و ریختهگری چدنهای پر کروم (Melting and Casting of High Chromium Cast Irons)
چدنهای پر کروم یا چدن های کروم (High Chromium Cast Irons) به دلیل خواص مکانیکی برجسته، مقاومت فوقالعاده در برابر سایش و خوردگی، و کاربرد گسترده در صنایع سنگین بخصوص در ساخت دستگاه سنگ شکن، برخوردارند. این نوع چدنها حاوی درصد بالایی از کروم (بیش از 12 درصد) هستند که باعث تشکیل کاربیدهای کروم در ساختار میکروسکوپی آنها میشود. این کاربیدها مقاومت سایشی بالا و طول عمر طولانی قطعات تولیدی را تضمین میکنند.
فرآیند تولید چدنهای پر کروم شامل چند مرحله اصلی قالبگیری و ذوبریزی ، تخلیه و سنگ زنی یا تکمیل کاری و در نهایت عملیات حرارتی است: این مراحل باید با دقت و بر اساس استانداردهای مشخص انجام شوند تا از ایجاد عیوبی مانند ترکخوردگی، نفوذ ماسه یا کشیدگی جلوگیری شود.
۱. قالبگیری چدنهای پر کروم (Molding of High Chromium Cast Irons)
قالبگیری صحیح و دقیق، پایهگذار کیفیت نهایی قطعات تولیدی است. در این مرحله:
- انتخاب مواد قالبگیری: استفاده از ماسههایی با مقاومت بالا و ویژگیهای حرارتی مناسب برای جلوگیری از ماسهسوزی و نفوذ مذاب ضروری است.
- طراحی سیستم راهگاهی و تغذیه: یک سیستم راهگاهی مناسب به کاهش تلاطم مذاب و جلوگیری از ایجاد حفرههای گازی و انقباضی کمک میکند.
- استفاده از پوششهای مقاوم: پوشش قالب با پوشان قالب مقاوم در برابر دماهای بالا، عیوب سطحی قطعات را کاهش میدهد.
۲. ذوبریزی چدنهای پر کروم (Pouring of High Chromium Cast Irons)
ذوبریزی مرحلهای است که مذاب تولیدشده به قالب منتقل میشود. برای این مرحله:
- کنترل دمای ذوبریزی: دماهای بارریزی برای قطعات با ضخامت کمتر از 10 میلیمتر معمولاً بین 1350 تا 1400 درجه سانتیگراد تنظیم میشود.
- جلوگیری از کشیدگی و عیوب سطحی: استفاده از دماهای مناسب باعث جلوگیری از عیوبی مانند نفوذ مذاب یا ماسهسوزی میشود.
- کنترل سرعت ریختن مذاب: سرعت مناسب در ریختن مذاب از تلاطم و ایجاد حفرههای گازی جلوگیری میکند.
نقش عناصر مختلف در خواص و ریختهگری چدنها
- آلومینیوم (Aluminum)
آلومینیوم بهطور معمول در چدنها بهعنوان یک عامل کمککننده به فرآیند تشکیل فریت (Ferrite) عمل میکند. این عنصر همچنین باعث تسهیل تشکیل گرافیت در مقادیر بسیار کم (حدود 0.025 درصد) میشود. آلومینیوم به دلیل ویژگیهای خود، میتواند اثرات مثبتی در بهبود خواص مکانیکی چدنها داشته باشد، بهویژه در کاهش اندازه دانهها و بهبود قابلیت ماشینکاری.
- آنتیموان (Antimony)
آنتیموان بهعنوان یک پایدارکننده پرلیت (Pearlite) شناخته میشود. این عنصر معمولاً در چدنهای خاکستری برای افزایش مقاومت به سایش و بهبود خواص مکانیکی در دماهای بالا استفاده میشود. آنتیموان بهویژه در ایجاد ساختار پرلیت مؤثر است و موجب بهبود استحکام کششی و سختی چدنها میشود.
- بیسموت (Bismuth)
بیسموت بهعنوان پایدارکننده ضعیف پرلیت عمل میکند. این عنصر معمولاً در مقادیر کم به چدن اضافه میشود تا خواص فیزیکی و مکانیکی آن بهبود یابد. بیسموت همچنین میتواند به کاهش خواص شکنندگی چدنها کمک کند و در فرآیند ریختهگری تأثیرات مثبتی داشته باشد.
- بور (Boron)
بور (Boron) که در مقادیر بالای 0.15 درصد استفاده میشود، بهعنوان پایدارکننده قوی پرلیت عمل میکند. این عنصر توانایی تشکیل کاربیدهای بور را دارد که میتواند بهطور قابلتوجهی استحکام چدن را در برابر سایش و خوردگی افزایش دهد. بور همچنین میتواند در کاهش اندازه دانهها و بهبود خواص مکانیکی مؤثر باشد.
- کروم (Chromium)
کروم بهعنوان یکی از قویترین عناصر تشکیلدهنده کاربید (carbide-forming) شناخته میشود که توانایی تشکیل کاربیدهای پیچیده (complex carbides) را دارد. این عنصر با افزایش تمایل به سفید شدن و جلوگیری از گرافیته شدن قسمتهای نازک در حین سرد شدن، مانع از تجزیه کاربیدها (carbides) میشود. علاوه بر این، کروم به تشکیل پرلیت (pearlite) لایهای و سختتر کمک کرده و ساختاری مقاومتر به سایش فراهم میآورد.
نتیجه چنین ساختاری، افزایش مقاومت به سایش (abrasion resistance) در دماهای پایین و بالا، بهبود مقاومت به خزش (creep resistance) و افزایش استحکام در دماهای بالا (high-temperature strength) است. همچنین، کروم موجب افزایش سختی و مقاومت در برابر فرسایش (wear) و اکسیداسیون (oxidation) در دماهای بالا میشود. این ویژگیها باعث بهبود عملکرد چدنهای آستینیتی و مقاوم به حرارت در شرایطی میشود که قطعات به طور متناوب در معرض تغییرات دما قرار میگیرند.
- مس (Copper)
مس در مقادیر کم میتواند گرافیت زا (Graphitizing) باشد و بهطور موثری تشکیل گرافیت را تسهیل کند. پس از قلع، مس بهعنوان یک پرلیتزای خوب شناخته میشود. این عنصر بهویژه در چدنهای خاکستری و آلیاژهایی که نیاز به مقاومت در برابر خوردگی دارند، بهکار میرود.
- منگنز (Manganese)
منگنز یکی از عناصر کاربیدزای (Carbide-forming) مهم است که همچنین باعث تشکیل پرلیت (Pearlite) میشود. این عنصر در چدنها برای بهبود مقاومت به سایش و افزایش استحکام کششی استفاده میشود. منگنز همچنین میتواند بهعنوان یک عامل اکسیژنزدای مؤثر در فرآیند ذوب چدن عمل کند.
- تلریم (Tellurium)
تلریم بهعنوان یک پایدارکننده قوی پرلیت شناخته میشود. این عنصر بهویژه در چدنهای با گرافیت ورقهای کاربرد دارد و میتواند خواص مکانیکی چدن را بهبود دهد. تلریم همچنین میتواند در کاهش اندازه دانهها و بهبود خواص ماشینکاری مؤثر باشد.
- تیتانیم (Titanium)
تیتانیوم در مقادیر زیر 0.25 درصد باعث تسهیل پیدایش گرافیت میشود. این عنصر بهویژه در چدنهای آلیاژی برای بهبود خواص مکانیکی و کاهش شکنندگی مورد استفاده قرار میگیرد. تیتانیم همچنین میتواند بهعنوان یک عامل کمکی در فرآیند تولید گرافیت در چدنهای آلیاژی بهکار رود.
- نیکل (Nickel)
نیکل بهعنوان یک عنصر ضعیف در ایجاد پرلیت (pearlite) شناخته میشود و همچنین فرآیند تشکیل گرافیت (graphite) و فریت (ferrite) را تسهیل میکند. این عنصر بهویژه در چدنهای آلیاژی که نیاز به مقاومت در برابر خوردگی (corrosion resistance) دارند، کاربرد دارد. نیکل بهویژه در چدنهای آستینیتی (austenitic cast irons) و مقاوم به حرارت برای بهبود خواص مکانیکی (mechanical properties) و مقاومت به خوردگی استفاده میشود.
نیکل یکی از رایجترین عناصر آلیاژی است که در چدنها بهکار میرود و تأثیرات منفی خاصی بر آنها ندارد. این عنصر به گرافیته شدن کمک میکند، اما اثر آن تنها به اندازه نصف سیلیسیم (silicon) است و علاوه بر این، باعث پراکندگی گرافیت در شکل بسیار ریز میشود. نیکل همچنین پایداری کاربیدهای اولیه (primary carbides) را کاهش داده و موجب ریز شدن و پایداری پرلیت (pearlite) میشود. این ویژگی با وجود مقدار کمی سیلیسیم بهتر صورت میگیرد و حتی میتواند منجر به ایجاد ساختار مارتنزیتی (martensitic structure) شود. همچنین، نیکل باعث ریز دانه شدن (grain refinement) چدنها میشود. به این ترتیب، نیکل استحکام چدن را بهطور یکنواخت و متناوب افزایش میدهد.
نیکل باعث افزایش وزن مخصوص (specific gravity) چدن شده و میزان تخلخل (porosity) آن را بهطور قابل توجهی کاهش میدهد. همچنین، این عنصر به همراه عناصری نظیر کروم (chromium) برای دستیابی به یکنواختی ریختهگری قطعات با ضخامتهای متغیر کاربرد وسیعی دارد.
- وانادیم (Vanadium)
وانادیوم بهعنوان یکی از قویترین عناصر کاربیدزای (Carbide-forming) شناخته میشود و همچنین قادر به ایجاد پرلیت قوی است. این عنصر معمولاً در چدنهای آلیاژی برای بهبود استحکام و مقاومت به سایش استفاده میشود. وانادیم همچنین میتواند بهعنوان یک عامل تقویتکننده در ساختار چدنها و بهبود خواص مکانیکی آنها عمل کند.
- منیزیم (Magnesium)
منیزیم بهعنوان یک عنصر کلیدی در تولید چدنهای نشکن (چدن داکتیل)، تأثیر بسزایی بر فرآیند ریختهگری دارد. اضافه کردن مقدار معینی از منیزیم به آهن مذاب، منجر به تشکیل گرافیتهای کرویشکل میشود که خواص مکانیکی چدن را بهبود میبخشد. این فرآیند با کاهش مقدار گوگرد و اکسیژن در مذاب، از تشکیل گرافیتهای رشتهای جلوگیری میکند و به بهبود کیفیت ریختهگری کمک میکند.
- گرافیت (Graphite)
گرافیت که در دسته انواع فرو آلیاژ در بخش مواد اولیه ریخته گری شرکت اوانگارد به فروش می رسد، بهعنوان یک افزودنی در ریختهگری چدنها برای کنترل شکل و اندازه گرافیتها در ساختار چدن استفاده میشود. این فروآلیاژ معمولاً در دو نوع بدون سولفور و با سولفور در بازار موجود است. گرافیت بدون سولفور در فرآیندهای تولید چدنهایی با گرافیتهای کرویشکل یا فشرده استفاده میشود و باعث بهبود خواص مکانیکی چدنها میشود. در حالی که گرافیت با سولفور بهطور معمول در تولید چدنهای خاکستری و چدنهایی با گرافیتهای ورقهای کاربرد دارد. گرافیت در این فرآیند بهعنوان یک عامل تقویتکننده عمل کرده و موجب بهبود خواص ریختهگری، از جمله کاهش انقباضات و افزایش چقرمگی میشود.
- نیوبیوم (Niobium)
چدنهای پرکروم (High-Chromium Cast Irons) به دلیل ترکیب بالای کروم در ساختار خود، مقاومت بالایی در برابر سایش و خوردگی دارند. افزودن نیوبیوم (Niobium) به این آلیاژها میتواند تأثیرات قابلتوجهی بر خواص مکانیکی و رفتار سایشی آنها داشته باشد.
مطالعات نشان دادهاند که افزودن نیوبیوم به چدنهای پرکروم، بهویژه در مقادیر 0.1% تا 1%، میتواند منجر به تشکیل کاربیدهای نیوبیوم (NbC) با سختی بسیار بالا شود. این کاربیدها در ساختار چدن پراکنده شده و بهعنوان فازهای سخت، مقاومت سایشی آلیاژ را افزایش میدهند. همچنین، افزودن نیوبیوم به چدن های کروم میتواند بهعنوان هسته جوانهزنی برای تشکیل کاربیدهای کروم (M7C3) عمل کند، که این امر منجر به بهبود توزیع و اندازه کاربیدها در ساختار میشود و در نتیجه، خواص مکانیکی و سایشی چدن را بهبود میبخشد.
علاوه بر این، حضور نیوبیوم در چدنهای پرکروم میتواند تأثیر مثبتی بر رفتار سایشی این آلیاژها داشته باشد. بررسیها نشان دادهاند که افزودن نیوبیوم به چدنهای سفید پرکروم، مقاومت سایشی و مقاومت در برابر ضربه را بهبود میبخشد. این بهبود خواص به دلیل تغییر در اندازه و توزیع کاربیدها و تشکیل کاربیدهای نیوبیوم است که سختی و مقاومت به سایش آلیاژ را افزایش میدهند.
در نتیجه، افزودن نیوبیوم به چدنهای پرکروم میتواند منجر به بهبود خواص مکانیکی و سایشی این آلیاژها شود. با این حال، برای دستیابی به بهترین نتایج، لازم است مقدار بهینه نیوبیوم و شرایط عملیات حرارتی بهدقت تعیین شوند.
- تنگستن (Tungsten)
اثر تنگستن در قطعات نایهارد و چدنهای پرکروم
- نقش تنگستن در قطعات نایهارد
تنگستن بهعنوان یکی از عناصر آلیاژی مهم در چدنهای نایهارد، بهویژه در نایهارد 4، نقش برجستهای در بهبود خواص مکانیکی ایفا میکند. افزودن این عنصر به چدن نایهارد، منجر به تشکیل کاربیدهای تنگستن میشود که ساختار ریزساختاری چدن را تقویت میکنند. این تقویت ساختاری باعث افزایش سختی، مقاومت به ضربه و تحمل شرایط عملیاتی سنگین میگردد. حضور کاربیدهای تنگستن، علاوه بر بهبود مقاومت سایشی، به کاهش احتمال ترکهای ناشی از تنشهای مکانیکی کمک میکند. - اثر تنگستن در چدنهای پرکروم
چدنهای پرکروم با 12 تا 28 درصد کروم و 1.5 تا 3.5 درصد کربن، شامل فازهای زمینه (فریت، پرلیت، آستنیت و مارتنزیت) و فازهای کاربیدی (Mo2C, M7C3, M3C) هستند. در این چدنها، گرافیت در طول انجماد تشکیل نمیشود و بهجای آن، فازهای کاربیدی پایدار ایجاد میگردند. برای جلوگیری از تشکیل پرلیت، عناصر دیگری نظیر نیکل، مولیبدن و مس نیز به آلیاژ اضافه میشوند. تنگستن در این چدنها بهعنوان یک عنصر کاربیدزای قوی، با کروم و آهن در تشکیل کاربیدهایی مانند Fe3W3C و Fe4W2C مشارکت میکند. این کاربیدها که به شکل ساختار یوتکتیکی استخوان ماهی در لابهلای آستنیت یوتکتیکی قرار میگیرند، مقاومت سایشی و سختی چدن را بهبود میبخشند. همچنین با افزایش درصد کروم، کاربیدهای نوع M3C جای خود را به نوع M7C3 میدهند که موجب ارتقای خواص مکانیکی و ساختاری میشود. لازم بذکر است که ، ترکیب شیمیایی این چدنها یکی از عوامل کلیدی در کنترل ریزساختار و عملکرد آنها است.
تاثیر عملیات حرارتی بر سختی و ریزساختار چدن سفید آلیاژی های کروم
چدنهای سفید پرکروم به دلیل مقاومت بالای خود در برابر سایش و ویژگیهای مکانیکی منحصربهفرد، در کاربردهای صنعتی گستردهای مورد استفاده قرار میگیرند. این نوع چدنها در صنایعی مانند معدن، تولید سیمان، ساخت قالبهای آجر، تیغههای توربین ماشینهای شات پینینگ و بهویژه در تولید گلولههای آسیاب ، چکشهای سنگشکن و دستگاه ماسه ساز نقش حیاتی دارند. از نظر اقتصادی، این مواد به دلیل دوام و کارایی بالا، جایگاه ویژهای در صنایع مختلف به خود اختصاص دادهاند.
ساختار میکروسکوپی چدنهای سفید پرکروم عمدتاً شامل یک زمینه مارتنزیتی است که در شبکهای از کاربیدهای کمپلکس آهن و کروم توزیع شده است. این ساختار موجب ایجاد مقاومت به سایش بالا و تحمل ضربات مکانیکی ناشی از برخورد مصالح به سندان ها و چکش ها در دستگاه سنگ شکن و همچنین در دستگاه اسیاب گلولهها با یکدیگر و با بدنه آسیاب میشود. برای مثال در این بحث به گلوله اسیاب می پردازیم تا مسئله روشن تر شود. گلولههای آسیاب که در اندازههای مختلف تولید میشوند، در اتاقچههای آسیابهای سیمان سفید یا خاکستری به کار میروند. این گلولهها به دلیل نرخ سایش پایین، حداقل مواد فلزی را وارد محصول نهایی، مانند سیمان تولیدی، میکنند.
سختی حجمی قطعات پرکروم از دو جنبه اهمیت دارد. نخست، تفاوت شدید سختی بین سطح و مرکز قطعات میتواند موجب تغییر شکل قطعه شود. این مسئله معمولاً ناشی از غیرهمگن بودن ساختار و عملیات حرارتی نامناسب است. دوم، کاهش سختی از سطح به مرکز قطعات باعث کاهش کارایی گلولههای کوچکتر میشود و امکان استفاده مجدد از قطعات سایز بزرگ فرسوده را محدود میکند.
ریزساختار چدنهای سفید پرکروم شامل دندریتهای اولیه و ساختار یوتکتیکی است. کاربیدهای یوتکتیکی تشکیلشده در این ساختار، بسته به ترکیب شیمیایی و سرعت سرد شدن در حین انجماد، میتوانند یکی از سه نوع استوکیومتری (FeCr)23C6و (FeCr)7C3 یا (FeCr)3C باشند. در بیشتر موارد، کاربیدهای یوتکتیکی از نوع (FeCr)7C3 هستند، صرفنظر از درصد کروم موجود، سرعت سرد شدن، علاوه بر تعیین نوع فاز زمینه که میتواند شامل آستنیت، مارتنزیت یا پرلیت باشد، بر نوع و توزیع کاربیدها نیز تأثیر میگذارد و همچنین لازم بذکر است که، در سرعتهای سرد شدن پایین، کاربیدهای ثانویه در اطراف دندریتهای آستنیت تشکیل میشوند.
چدنهای سفید پرکروم یا چدنهای سفید های کروم با ترکیب هیپویوتکتیک، به دلیل عدم رسوب کاربیدهای اولیه، چقرمگی بیشتری نسبت به ترکیبهای هایپریوتکتیک دارند. ساختار ریختهگری این آلیاژها شامل دندریتهای اولیه و ساختار یوتکتیکی است که اندازه کلونی آن به دامنه انجماد و سرعت سرد شدن وابسته است. ساختار کاربیدهای یوتکتیکی به نوع و مقدار عناصر کاربیدزا و کربن معادل بستگی دارد.
در فرآیند سرد شدن تعادلی، از دمای یوتکتیک تا دمای بحرانی (720 درجه سانتیگراد)، رسوب کاربیدهای کروم از زمینه آستنیت آغاز میشود و با ادامه سرد شدن، استحاله پرویوتکتیکی رخ میدهد. در سرد شدن غیرتعادلی، آستنیت فوقاشباع از کربن و کروم ممکن است به بینیت یا پرلیت تبدیل شود. استفاده از عناصر آلیاژی میتواند از این استحاله جلوگیری کند. افزایش درصد کربن در این آلیاژها موجب افزایش سختی کاربیدهای یوتکتیکی میشود. در عین حال، وضعیت کاربیدهای یوتکتیکی (FeCr)7C3 در چدنهای حاوی 10 تا 26 درصد کروم، طی عملیات آستنیتهکردن تغییر نمیکند.
عملیات حرارتی چدن سفید پرکروم (عملیات حرارتی چدن سفید های کروم)
عملیات حرارتی در چدنهای سفید پرکروم (High-Chromium White Cast Iron) یا بعبارتی عملیات حرارتی های کروم ، شامل مراحل آنیل (Annealing)، سختکاری (Hardening) و تمپر (Tempering) است که به منظور دستیابی به ریزساختاری با کاربیدها و زمینه مناسب برای افزایش مقاومت به سایش و چقرمگی انجام میشود. برای دستیابی به حداکثر سختی و مقاومت به سایش، ایجاد زمینه مارتنزیتی (Martensitic Matrix) از طریق عملیات حرارتی ضروری است. استفاده از عناصر آلیاژی مناسب برای جلوگیری از تشکیل پرلیت (Pearlite) و افزایش قابلیت سختیپذیری (Hardenability) اهمیت دارد. با افزایش درصد کربن و کروم، توزیع یکنواختتری از کاربیدها در زمینه حاصل میشود و امکان دستیابی به مارتنزیت و کاربیدهای بیشتر در سرعتهای پایینتر سرمایش فراهم میگردد.
سرد کردن در هوای فشرده میتواند به تشکیل زمینه مارتنزیتی با تنشهای داخلی کمتر منجر شود. استفاده از عناصر آلیاژی مانند نیکل (Ni)، منگنز (Mn) و مس (Cu) میتواند درصد آستنیت باقیمانده (Retained Austenite) را افزایش داده و مقاومت به سایش را کاهش دهد.
ترکیب شیمیایی یک نوع چدن سفید پر کروم | ||||||||
Cu | Ni | Mo | Cr | S | P | Mn | Si | C |
0.07 | 0.2 | 0.5 | 15 | 0.007 | 0.03 | 0.6 | 0.8 | 2.6 |
دمای آستنیته کردن (Austenitizing Temperature) بر ساختار و خواص نهایی تأثیرگذار است و تعیینکننده درصد کربن محلول در زمینه آستنیت میباشد. محدوده دمای آستنیته کردن برای چدنهای سفید پرکروم حاوی 12 تا 20 درصد کروم بین 950 تا 1100 درجه سانتیگراد است. با افزایش دمای آستنیته، پایداری آستنیت افزایش یافته که در نتیجه میزان آستنیت باقیمانده افزایش و سختی کاهش مییابد. دمای آستنیته پایین نیز موجب تشکیل مارتنزیت کمکربن میشود که در نتیجه سختی و مقاومت به سایش کاهش مییابد.
با افزایش سرعت سرد کردن، استحالههای نفوذی به تعویق افتاده و ریزساختار زمینه به فازهای غیرتعادلی نظیر بینیت بالایی (Upper Bainite)، بینیت پایینی (Lower Bainite) و مارتنزیت تمایل پیدا میکند. تحقیقات نشان داده است که برای مقاطع تا ضخامت 120 میلیمتر، تفاوت سختی در دو محیط کوئنچ هوای فشرده و روغن نامحسوس است. محیط کوئنچ هوای فشرده از دمای آستنیته تا دمای پایینتر از تشکیل پرلیت (در حدود 550 درجه) سانتیگراد توصیه شده است.
دو نوع تمپر برای چدنهای سفید پرکروم پیشنهاد شده است: یکی تمپر در محدوده دمایی 205 الی 230 درجه سانتیگراد به مدت 2 الی 4 ساعت که به منظور افزایش تافنس و آزاد شدن تنشهای داخلی انجام میشود؛ دیگری تمپر دما بالا بهویژه برای قطعات بزرگ ریختهگری به منظور کاهش درصد آستنیت باقیمانده و افزایش مقاومت به ورقهای شدن در محدوده دمایی 480 الی 550 درجه سانتیگراد. ساختار پس از کوئنچ حاوی کسر حجمی از آستنیت باقیمانده است و زمان یا دمای بیش از حد تمپر موجب افت سختی و کاهش مقاومت به سایش میشود.
سیکل های عملیات حرارتی پیشنهادی بر روی یک نوع چدن پر کروم | ||
توضيح سيکل عمليات حرارتي | نام سيکل | شماره سيکل |
آستنیته کردن در دمای 970 درجه سانتیگراد، سپس کوئنچ با هوای فشرده تا دمای 500 درجه سانتیگراد، خنکسازی در هوا تا 50 درجه سانتیگراد و در نهایت تمپر در دمای 550 درجه سانتیگراد به مدت 2 ساعت و سرد کردن در هوا انجام میشود. | کوئنچ هواي فشرده | 1 |
آستنیته کردن در دمای 970 درجه سانتیگراد انجام شده و سپس قطعه در روغن کوئنچ میشود تا دمای 500 درجه سانتیگراد برسد. بعد از آن، قطعه در هوا تا دمای 50 درجه سانتیگراد خنک میشود. در نهایت، تمپر در دمای 550 درجه سانتیگراد به مدت 2 ساعت صورت گرفته و سپس قطعه در هوا سرد میشود. | کوئنچ روغن | 2 |
آستنیته کردن در دمای 970 درجه سانتیگراد انجام میشود، سپس قطعه به مدت 90 ثانیه در حمام نمک با دمای 500 درجه سانتیگراد نگهداری میشود. پس از آن، قطعه در هوای فشرده تا دمای 50 درجه سانتیگراد سرد میشود. در مرحله بعد، تمپر در دمای 520 درجه سانتیگراد به مدت 2 ساعت انجام میشود و در نهایت قطعه دوباره در برابر هوای فشرده سرد میشود. | مارتمپرینگ | 3 |
تأثیر عملیات حرارتی بر سختی و ریزساختار چدن سفید پرکروم یک موضوع کلیدی در زمینه مهندسی مواد و تولید قطعات مقاوم به سایش است. چدنهای سفید پرکروم (High Chromium White Cast Iron) به دلیل ویژگیهای خاص خود در برابر سایش بسیار مقاوم هستند و در صنعتهای مختلف از جمله صنایع معدنی، فولادسازی، و تولید ماشینآلات سنگین استفاده میشوند. یکی از عوامل اصلی که بر ویژگیهای مکانیکی این آلیاژها تأثیر میگذارد، عملیات حرارتی است که به منظور بهبود سختی و ریزساختار آنها انجام میشود.
سختی چدن سفید پرکروم یا بعبارتی سختی چدن های کروم
سختی های کروم پس از ریختگری اولیه میتواند حدود HRC 47 (Hardened Rockwell C) باشد. اما با انجام عملیات حرارتی مناسب به روی چدن های کروم ، این مقدار میتواند به بیش از HRC 60 برسد. این افزایش در سختی به دلیل ایجاد ساختار مارتنزیتی است که از طریق عملیات کوئنچ و آستنیته کردن در دماهای بالا به دست میآید. عملیات حرارتی همچنین موجب بهبود توزیع کاربیدها در زمینه میشود که نتیجه آن، افزایش مقاومت به سایش و عمر طولانیتر قطعات است.
یکی از موارد جالب در عملیات حرارتی چدن پر کروم این می باشد که ، در فرآیند تمپر، انتظار داریم که سختی پس از مرحله تمپر کاهش یابد، زیرا تمپر باعث بازگشت برخی از فازهای مارتنزیتی میشود. با این حال، در چدنهای سفید پرکروم، کاهش سختی پس از تمپر به شدت محدود است. دلیل این امر تجزیه آستنیت باقیمانده و تشکیل کاربیدهای ثانویه است که نه تنها سختی را کاهش نمیدهند بلکه آن را افزایش نیز میدهند. به عبارت دیگر، پس از تمپر، سختی نهایی چدن به مجموع دو اثر بستگی دارد: کاهش سختی ناشی از بازگشت مارتنزیت و افزایش سختی به دلیل تشکیل کاربیدهای ثانویه و استحاله آستنیت باقیمانده به مارتنزیت. این فرایند موجب میشود که چدنهای سفید پرکروم دارای ویژگیهای استحکام بالا و مقاومت به سایش عالی باقی بمانند.
این نکات نشاندهنده اهمیت عملیات حرارتی در بهبود خواص مکانیکی چدنهای کروم دار است. استفاده از روشهای صحیح مانند آستنیته کردن در دماهای بالا، کوئنچ در محیطهای خاص مانند هوا یا روغن، و سپس تمپر در دماهای کنترلشده، میتواند عملکرد این قطعات چدنی های کروم را در برابر سایش به شدت بهبود بخشد. برای افزایش اثربخشی این عملیات، ترکیب دقیق عناصر آلیاژی مانند کروم، کربن و دیگر عناصری مانند مولیبدن و وانادیوم ضروری است.
سختی نمونه ها در سیکل های مختلف | ||
سختي مغز | سختي سطح | شماره سيکل |
58 | 60 | 1 |
61.5 | 64 | 2 |
61 | 62.5 | 3 |
با انجام هر 3 سیکل عملیات حرارتی فوق که در بخش عملیات حرارتی به ان اشاره داشتیم، سختی تمام قطعات افزایش مییابد که این افزایش ناشی از ایجاد مارتنزیت و رسوب کاربیدهای ثانویه در زمینه است. که در ادامه، نتایج بهدستآمده از هر سیکل را شرح داده ایم:
- سیکل شماره 1 که شامل کوئنچ در هوای فشرده و تمپر است، کمترین سختی سطحی را دارا می باشد.
- نمایان شدن ترک در سطح نمونه 2 پس از عملیات حرارتی نشان میدهد که سیکل عملیات حرارتی برای آن مناسب نبوده است.انتخاب روغن به عنوان محیط کوئنچ که زمینه مارتنزیتی سخت را به دنبال دارد، همراه با تنش انقباضی ناشی از افت دما و انبساطی که از استحاله مارتنزیتی نشات میگیرد، منجر به تمرکز تنش و تشکیل ترکهای ریز در قطعه میشود.
- پیشبینی میشود که نگهداری نمونه در دمای بالاتر از شروع تشکیل مارتنزیت در حمام نمک مذاب، باعث همدمایی سطح و مغز قطعه شده و پس از کوئنچ، کمترین اختلاف سطحی را مییابد. به همین دلیل، سیکل 3 به عنوان سیکل نهایی پذیرفته میشود.
کمترین سختی مربوط به قطعه در حالت ریختگری و معادل 47 HRC می باشد. با انجام سیکل عملیات حرارتی که در بالا ذکر شده، سختی تمام قطعات افزایش مییابد که این نوع افزایش ناشی از ایجاد مارتنزیت و رسوب کاربیدهای ثانویه در زمینه است. مطابق با سختیسنجی حجمی، کمترین اختلاف سختی در سطح و حجم با عملیات حرارتی مارتمپرینگ قابل دستیابی است. بهترین ساختار زمینه، مارتنزیتی است که توسط کاربیدها تحکیم میشود. کاربیدهای یوتکتیکی 3M7C با مورفولوژی میلهای و در برخی موارد تیغهای در این نمونهها مشاهده میشود.لازم بذکر است که روند رشد کاربیدهای 3M7C به صورت میلهای و تیغهای است، که محور طولی آنها موازی با جهت انتقال حرارت در قالب می باشد.
کاربرد چدن های سفید آلیاژی در معدن
چدنهای سفید آلیاژی، بهویژه انواع پرکروم (High Chromium Cast Irons)، به دلیل مقاومت بالای خود در برابر سایش و خوردگی، در صنعت معدن کاربرد گستردهای دارند. این آلیاژها با دارا بودن 12 تا 35 درصد کروم، ساختار مارتنزیتی ایجاد میکنند که سختی و دوام بالایی را فراهم میآورد.
در تجهیزات معدنی مانند دستگاههای سنگشکن، چکشهای ساختهشده از چدنهای پرکروم بهعنوان اجزای کلیدی در فرآیند خردایش مواد به کار میروند. این چکشها با استاندارد بینالمللی ASTM A532 تولید شده و در برابر شرایط سخت کاری مقاومت بالایی نشان میدهند.
همچنین، گلولههای چدنی آسیاب از نوع پرکروم در آسیابهای صنعتی برای خردایش مواد معدنی استفاده میشوند. این گلولهها با داشتن کاربیدهای کروم اولیه و ثانویه، سختی و مقاومت به سایش بالایی دارند و در صنایعی مانند سیمان و فولاد بهکار میروند.
استفاده از چدنهای سفید آلیاژی در تجهیزات معدنی، علاوه بر بهبود کارایی فرآیندها، منجر به کاهش هزینههای نگهداری و افزایش طول عمر قطعات میشود. این ویژگیها، چدنهای سفید آلیاژی را به گزینهای ایدهآل برای کاربردهای معدنی تبدیل کرده است.
چکش های سنگ شکن پر کروم
در دستگاههای سنگشکن، چکشها بهعنوان یکی از اجزای کلیدی، نقش مهمی در خردایش مواد دارند. چکشهای سنگ شکن پر کروم (High Chromium Cast Irons) یا چکش های کروم به دلیل ویژگیهای منحصربهفرد خود، مانند مقاومت بالا در برابر سایش و خوردگی، یکی از مهمترین قطعات ریختهگری مورد استفاده در صنایع معدنی و ساختمانی هستند. برای مثال برای دستگاه سنگ شکن کوبیت برای قطعه چکش کوبیت 120 و چکش کوبیت 180 ، و دیگر قطعات سنگ شکن کوبیت در کنار فولاد منگنزی و چدن نایهارد از چدنهای ضد سایش پر کروم ساخته میشوند که طبق استاندارد بینالمللی ASTM A532 تولید می گردند. این استاندارد تضمینکننده کیفیت بالا و عملکرد بهینه این قطعات در شرایط سخت کاری است.
چدنهای ضد سایش پر کروم با ترکیب شیمیایی خاص خود که شامل 12 تا 35 درصد کروم است، ساختاری مارتنزیتی ایجاد میکنند که سختی و مقاومت به سایش بالایی دارد. این آلیاژها، به دلیل خواص مکانیکی و شیمیایی خود، در محیطهای خورنده و دماهای بالا نیز عملکرد مطلوبی ارائه میدهند. استفاده از آلیاژ چدن های کروم در چکشهای سنگشکنهای کوبیت، و دیگر تجهیرات معادن اعم از سرند و سایر دستگاه های خردایش و دانه بندی علاوه بر بهبود فرآیند خردایش، موجب کاهش هزینههای نگهداری و افزایش طول عمر قطعات میشود.
این قطعات ریختهگری با طراحی دقیق و عملیات حرارتی پیشرفته، سختی مارتنزیتی و مقاومت به سایش فوقالعادهای را فراهم میکنند که باعث بهبود کارایی دستگاه و کاهش توقفات ناشی از تعویض قطعات میشود، و از این رو ریخته گری چکش های کروم در صنعت خردایش حائز اهمیت می باشد.
گلولههای چدنی آسیاب
گلولههای چدنی آسیاب، بهویژه انواع آلیاژی آن، در صنایع مختلفی مانند معدن، سیمان و فولاد برای خردایش مواد به دانهبندی مناسب استفاده میشوند. این فرآیند با چرخش آسیاب و برخورد گلولهها به مواد داخل آن انجام میگیرد؛ بنابراین، گلولهها باید دارای خواص مکانیکی مناسب و مقاومت به ضربه بالا باشند.
گلولههای چدن سفید کمآلیاژی
این نوع گلولهها از چدن سفید کمآلیاژی با محتوای کروم بین 0.5 تا 1.5 درصد ساخته میشوند. پس از عملیات حرارتی، ساختار میکروسکوپی آنها شامل فاز کاربید آهن (سمانتیت) و مارتنزیت است و سختی بین 58 تا 62 راکول سی دارند. این گلولهها عمدتاً در صنایع معدنی مانند معادن مس و سنگ آهن مورد استفاده قرار میگیرند.
گلولههای چدن سفید پرکروم
این گلولهها با محتوای بالای کروم، ساختاری متفاوت نسبت به گلولههای کمآلیاژی دارند. کاربیدهای کروم اولیه و ثانویه که پس از عملیات حرارتی در زمینهای از مارتنزیت تشکیل میشوند، سختی بیشتری نسبت به کاربید آهن دارند و از مقاومت به سایش، ضربهپذیری و چقرمگی بالایی برخوردارند. مصرف اصلی این گلولهها در صنایع سیمان است؛ در آسیابهای دو یا سه اتاقچهای، در اتاقچه اول از گلولههای سایز 60 تا 90 میلیمتر با سختی 58 تا 62 راکول سی و در اتاقچههای بعدی از گلولههای سایز 15 تا 60 میلیمتر با سختی 58 تا 64 راکول سی استفاده میشود. میزان سایش این گلولهها در صنایع سیمان بسیار پایین است و علاوه بر سیمان خاکستری، در تولید سیمان سفید نیز به کار میروند. نوع دیگری از این گلولهها با 28 تا 30 درصد کروم در آسیابهای واحد گندلهسازی مجتمعهای بزرگ فولادسازی استفاده میشود.
ریخته گری چدن سفید ضد سایش پرکروم: کیفیت برتر با خدمات تخصصی شرکت آوانگارد
ریخته گری چدن سفید ضد سایش پرکروم یکی از پیشرفتهترین فرآیندها در صنعت ریختهگری است که به دلیل مقاومت استثنایی در برابر سایش و خوردگی، در صنایع معدنی، فولاد و سیمان کاربرد گستردهای دارد. شرکت آوانگارد، با بهرهگیری از مهندسین با دو دهه تجربه فارغالتحصیل دانشگاههای برتر ایران و کانادا، در زمینه ریختگری چدن سفید ضد سایش پرکروم فعالیت میکند.
این شرکت با استفاده از تجهیزات مدرن در کارخانه و کارگاههای پیشرفته خود، قطعاتی همچون چکشها و قطعات ضد سایش تجهیزات سنگشکن، خردایش و دانهبندی مواد در معادن، پوسته پمپ و پروانه پمپ و دیگر قطعات صنعتی را تولید میکند. ریخته گری چدن پرکروم در آوانگارد با رعایت استانداردهای جهانی و کنترل کیفیت دقیق انجام میشود تا محصولاتی با کیفیت بالا و قیمت رقابتی به مشتریان ارائه شود.
چدنهای سفید پرکروم که با روش ریخته گری چدن های کروم مورد بهره برداری قرار میگیرند، با داشتن 12 تا 35 درصد کروم و ساختاری مارتنزیتی، سختی و مقاومت به سایش بالایی دارند. این ویژگیها این آلیاژها را برای استفاده در تجهیزات سنگین و محیطهای کاری سخت ایدهآل کرده است.
خدمات آوانگارد در ریختگری چدن های کروم:
- تولید قطعات مقاوم و سفارشی با تکنولوژی پیشرفته.
- تضمین دوام و عملکرد قطعات با عملیات حرارتی پیشرفته پس از ریختگری چدن پرکروم.
- ارائه ریخته گری انواع چدن آلیاژی ضد سایش با کیفیت برتر.
چرا آوانگارد؟
شرکت آوانگارد با بهرهگیری از تیم مهندسی، فارغالتحصیلان دانشگاههای معتبر ایران و کانادا، با بیش از دو دهه تجربه در زمینه تولید و ریختهگری چدنهای سفید پرکرم ،با تولید قطعات تخصصی و ارائه خدمات با قیمت رقابتی، یکی از بهترین انتخابها برای خرید و فروش محصولات در تهران و سراسر ایران است.
می توانید پادکست (مقاله صوتی) مقاله را نیز گوش کنید، همچنین فایل پاور پوینت مقاله نیز قابل دانلود است.
برای سفارش و اطلاعات بیشتر در مورد ریخته گری انواع چدن سفید آلیاژی ضد سایش پر کرم و سایر خدمات آوانگارد، با تیم حرفهای آوانگارد در ارتباط باشید.
شرکت هلدینگ بازرگانی صنعتی آوانگارد
شماره تماس: 00989120228576
وب سایت: Avangardholding.com
مطالب مرتبط
فولاد کربنی چیست؟
نیکل چیست؟
تأمین شمش مس 99.999 ایزوتوپ با تضمین خلوص و کیفیت در هلدینگ آوانگارد
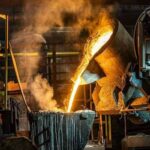
10 دیدگاه در “چدن های کروم چیست؟”
تیم متخصص و حرفه ای اوانگارد
درود وقت بخیر
سپاس از همراهی شما
چدن الیاژی های کروم همه گرید ها را ریخته گری می کنید؟
درود وقت بخیر
بله لطفا برای اطلاعات بیشتر با کارشناسان ما در بخش فروش تماس بگیرید.
چکش سنگ شکن از جنس چدن پرکروم که ضد سایش خوبی باشد موجود دارید؟
درود وقت بخیر
بله لطفا برای اطلاعات و راهنمایی دقیق تر با کارشناسان ما در بخش فروش تماس بگیرید.
ریختگری چدن های کروم کیلویی چنده
درود وقت بخیر
برای استعلام موجودی و قیمت چدن پر کروم با کارشناسان ما در بخش فروش تماس بگیرید.
برای اربیل عراق سفارش ریخته گری چکش کوبیت از جنس چدن های کروم دارم هر دست قیمتش چنده
درود وقت بخیر
لطفا برای اطلاعات بیشتر با واحد فروش تماس بگیرید