- صفحه اصلی
- خدمات ریخته گری
- برشکاری و تمیز کاری در ریخته گری
پس از پایان بار ریزی و انجماد، قطعات باید سرد شوند. سرد شدن می تواند درون قالب و یا خارج از آن انجام گیرد. انتخاب نحوه سرد شدن قطعه به جنس فلز یا آلیاژ و مدول سطحی قطعه بستگی دارد. اگر لازم باشد قطعه در قالب سرد شود، باید به آن فرصت کافی جهت سرد شدن تا دمای مناسب داده شود، سپس تخلیه قالب انجام گیرد. سرعت سرد شدن بر روی ریزساختار مؤثر است، خواص مکانیکی قطعه تحت تأثیر ریزساختار و سرعت سرد شدن می باشد؛ در نتیجه تخلیه زود هنگام قالب سبب ایجاد خواص مکانیکی نامطلوب و بروز عیوب و یا کاهش عمر و کارکرد قطعه خواهد شد، که این امر در شرکت آوانگارد با برخورداری از کادر مجرب مهندسی و نیروی کار ماهر و با تجربه در خصوص تولید انواع فولادها و چدن های آلیاژی با برخورداری از امکانات بروز در صنعت ریخته گری از قبیل دستگاه شیک اوت Shake Out، چکش تخریب برقی و انواع هیلتی و پیکور، انواع دستگاه های فرز سنگبری، ميني فرز، سنگ رومیزی، فرز انگشتی، انواع سایز های سنگ ساب و برش، هوا برش (سوخت و اکسیژن)، شات بلاست (Shotblasting) و دیگر تجهیزات مرسوم در ریخته گری با توجه به متریال قطعه به بهترین نحو ممکن انجام می پذیرد.
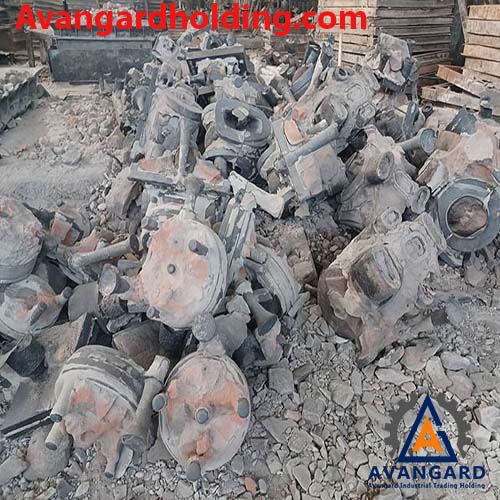
پس از ذوب ریزی و خالی کردن قطعه از قالب، مجموعه ای از عملیات بر روی قطعه انجام می گیرد، که به عملیات تکمیلی لقب دارد. عملیات تکمیلی، مجموعه ای از فرایندها با هدف رسیدن به خواصی از قبیل: بهبود کیفیت ظاهری، مقاومت در برابر خوردگی، مقاومت در برابر سایش، سختی، حذف پلیسه و دیگر معایب سطحی و… بر روی سطح قطعه انجام می گیرد.
عملیات تکمیل کاری شامل مراحل زیر است:
- ماسه زدایی؛ جداسازی ماسه قالب و ماهیچه از قطعه.
- جداسازی؛ جدا کردن اضافات شامل سیستم راهگاهی، تغذیه، پلیسه و …
- تمیزکاری (Trimming) و پرداخت نهایی: حذف گوشه، زوایا و نقاط تیز از روی قطعه.
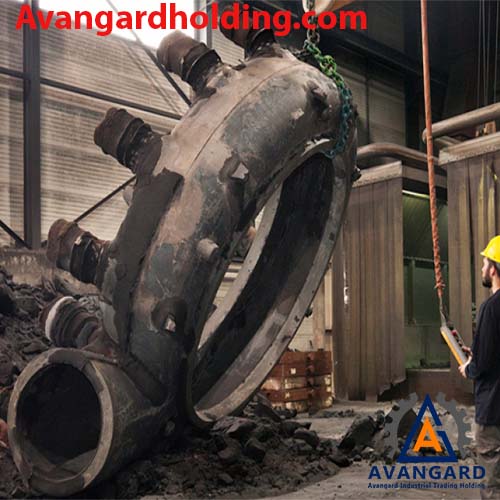
در ریخته گری آلیاژها با نقطه ذوب بالا (مانند فولاد و چدن) به دلیل دمای بالای بار ریزی، واکنش های مخرب و نامطلوبی بین اجزای مخلوط ماسه با مذاب رخ می دهد، که باعث چسبیده شدن ماسه به سطوح قطعه می شود. لذا باید پس از تخلیه قالب، سطوح قطعه تمیزکاری شود. میزان هزینه و زمان تمیزکاری به اندازه، میزان پیچیدگی قطعه و نوع فرایند تولید بستگی دارد.
روش های متفاوتی برای تخلیه و ماسه زدایی قالب وجود دارد:
روش استوانه چرخشی: در این روش از یک استوانه مشبک دوار استفاده می شود؛ در اثر چرخش آن ذرات ماسه از قطعه جدا و از سوراخ های موجود برروی بدنه استوانه خارج می شوند.
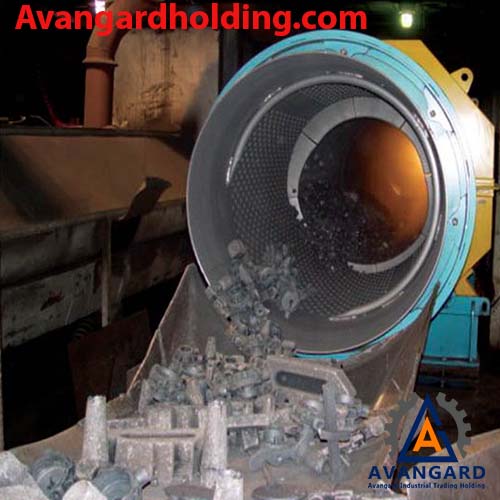
روش استوانه لرزشی: یک فرایند پیوسته است که برای قطعات ظریف و سرد کردن هنگام تخلیه مناسب است. این سیستم ها اتوماتیک هستند و وظایف تخلیه و ماسه زدایی را بشکل کامل و بدون دخالت دست انجام می دهند. سیستم های پنوماتیکی موجود در این ماشین سبب تخلیه قالب می شود. یکی از مزیت های این ماشین ها کم کردن میزان گرد و غبار تولیدی، زمان تخلیه قالب، بالا بردن سرعت عمل و بهبود کنترل مسائل زیست محیطی است.
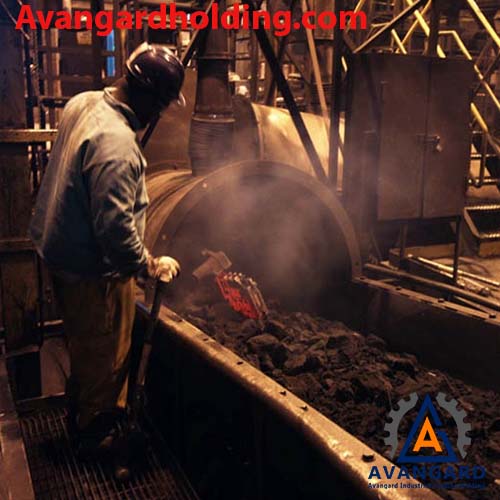
فرایند ارتعاشی: رایج ترین و قدیمی ترین روش تخلیه و ماسه زدایی که در اکثر کارخانجات ریخته گری استفاده می شود، استفاده از دستگاه شیک اوت Shake Out می باشد. این روش دارای دامنه ارتعاشات بسیار بالایی است. لذا ممکن است در حین ارتعاش، سیستم راهگاهی و تغذیه از قطعه جدا شوند. این روش برای تولید در حجم بالا بسیار مناسب است.
مطلب مرتبط: محصولات ریخته گری
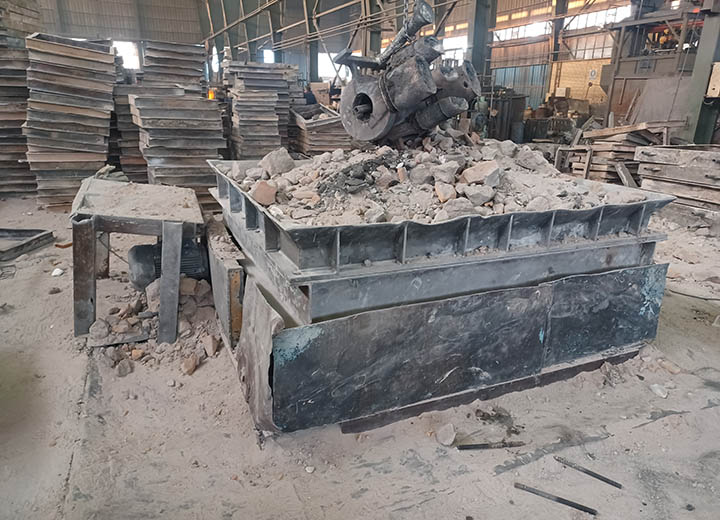
پس از تخلیه قالب و ماسه زدایی لازم است اضافات مانند: سیستم راهگاهی، تغذیه، پلیسه و… از قطعه جدا شوند. این اضافات باعث کم کردن بازده ریختگی و بازده کل می شوند. برای افزایش بهره اقتصادی باید در طراحی تغذیه و سیستم راهگاهی دقت کرد. امروزه با استفاده از محاسبات دقیق و نرم افزارهای شبیه ساز می توان میزان اتلافات و برگشتی ها را کاهش داد. نرم افزارهای شبیه ساز مختلفی در صنایع ریخته گری با اهداف مشخص به کار می روند. نرم افزار شبیه ساز محاسبات دقیقی جهت تعیین، تعداد، محل و ابعاد تغذیه، شکل، ابعاد و محل اتصال سیستم راهگاهی به قطعه ارائه می دهد؛ تا حداکثر راندمان به دست آید. معمولاً نتایج به دست آمده شبیه سازی شده تا 80 درصد صحت دارند.
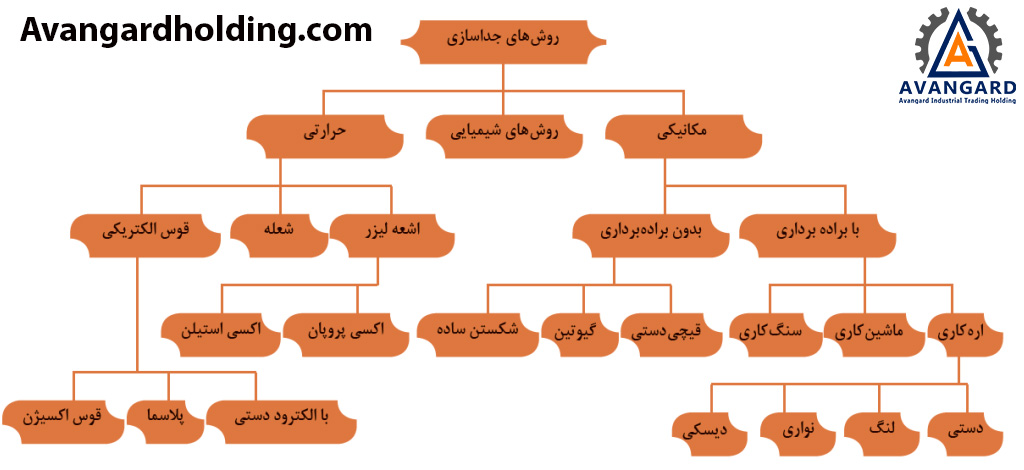
از این روش معمولا برای شکستن سیستم راهگاهی و تغذیه در قطعات ترد و شکننده استفاده می شود. گاهی اوقات در هنگام تخلیه، اضافات از قطعه جدا می شوند، که بایستی از ورود اضافات و پلیسه ها به درون مخلوط ماسه جلوگیری کرد.
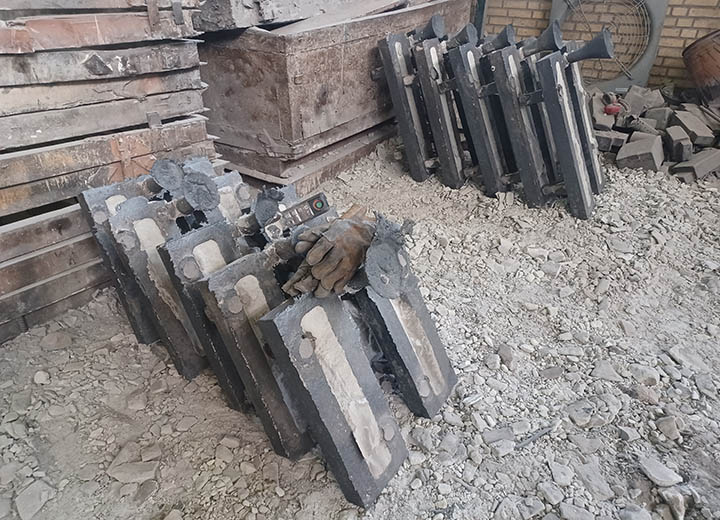
جداسازی با قوس الکتریکی یکی از مقرون به صرفه ترین روش های جداسازی قطعات ریختگی در صنایع بزرگ و متوسط که به عنوان جایگزین عملیات سنگ زنی محسوب می شود، می باشد. حرارت توسط قوس الکتریکی ایجاد شده بین الکترود گرافیتی و مس پوشش داده شده، تولید می شود. حذف زوائد با سرعت زیاد انجام می گیرد. بزرگترین عیب این روش تولید دود زیاد و صدا است.
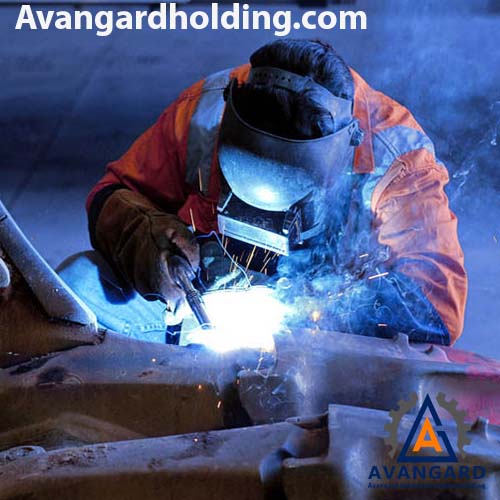
در این روش جداسازی می تواند با اره دستی، سنگ کاری و ماشین کاری انجام گیرد. در جداسازی با کمان اره باید متناسب با جنس قطعه، تیغه (جنس، شکل، اندازه تیغه) انتخاب شود. در جداسازی با چرخ ساینده (سنگ کاری) و سنگ فرز (ماشین کاری) با استفاده از سرعت بالای چرخ ساینده می توان اضافات را از قطعه جدا کرد. این روش برای از بین بردن زائده های بزرگ و یا کم کردن ضخامت سطوح استفاده می شود. دقت بالا و اقتصادی بودن این روش سبب فراگیر شدن آن شده است. یکی دیگر از ابزار جداسازی اره نواری است که از تيغه اي شبيه تيغه هاي معمولي ولي به شكل یک حلقه استفاده مي شود. تيغه نواري دور، دو محور دستگاه می چرخد و در اثر تماس با قطعه عمل براده برداري صورت مي گيرد.
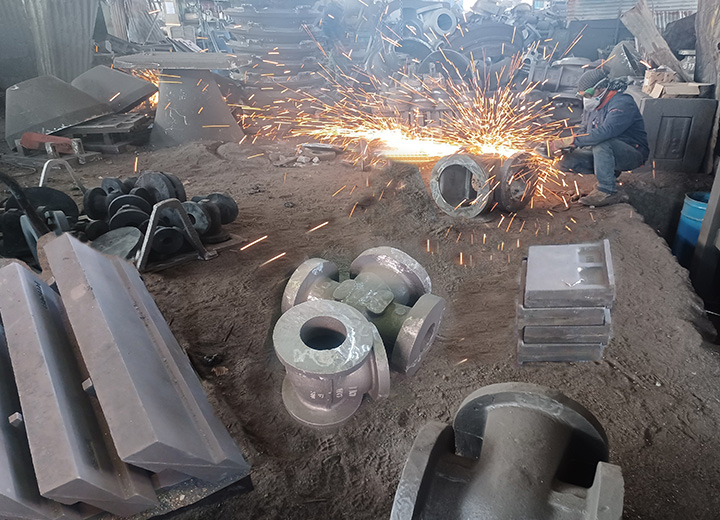
یکی دیگر از انواع ابزار در عملیات جداسازی استفاده از سنگ دستی است. از این روش برای جداسازی تمام فلزات و آلیاژها استفاده می شود. در این روش فرایند براده برداری بسیار ظریف توسط ذرات ساینده چسبیده شده به صفحه برش انجام می گیرد. در روش سنگ زنی(grinding) دقت و سرعت عمل بالاست. سنگ برش در عملیات سنگ زنی توسط ذرات سخت عملیات برش را انجام می دهند و در واقع هر کدام از ذرات ساینده به معنای یک ابزار برش است که انجام بخش خاصی از برش را بر عهده دارد.پس از جداسازی سیستم راهگاهی با استفاده از دستگاه سنگ، سنگ فرز، سنباده دستی، نوار سنباده و… اقدام به پلیسه زنی می شود. سنگ فرز در دو نوع برقی و پنوماتیکی و متناسب با دقت و ظرافت یا سایز در اندازه کوچک و یا بزرگ برای سنگ زنی پخها و سطوح زبر و خشن و برجسته و حذف پلیسه ها مورد استفاده قرار می گیرد.
مطلب مرتبط: قالبگیری و مونتاژ در ریخته گری
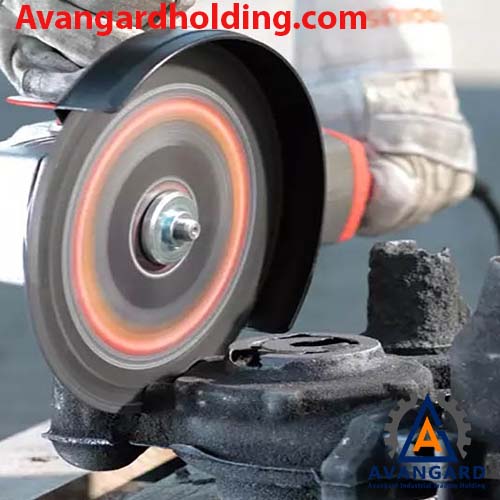
این روش با استفاده از یک گاز سوختنی مثل استیلن C2H2 و اکسیژن O2 به عنوان عامل سوختن و اکسیداسیون و بر اساس گداختن قطعه فلزی تا درجه حرارت 871 – 815 درجه سانتی گراد و اکسیداسیون صورت می گیرد. این فرایند به برش کاری فولادهای کربنی و کم آلیاژ محدود می شود، ولی فلزات فعال و یا با اکسید دیرگداز، به راحتی با شعله بریده نمی شوند.
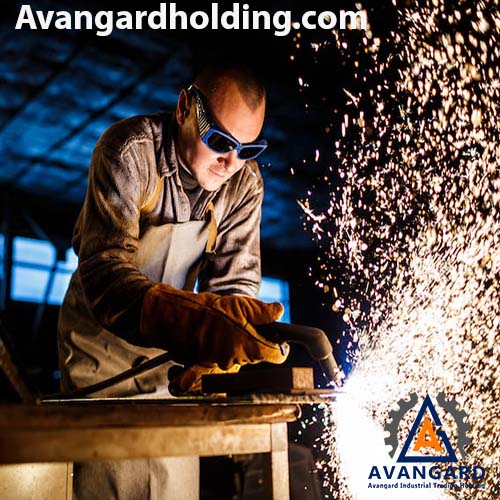
بخش تمیزکاری به منظور بالابردن کیفیت سطح قطعه انجام می گیرد. افزایش کیفیت سطح قطعه سبب افزایش مقاومت به خوردگی، خستگی و… می شود. در این مرحله حذف اثرات باقیمانده از اره کاری، پلیسه زنی و… انجام می گیرد.
تميزكاري شيميایي :
در اين روش جهت تميزكاري سطح از مواد شيميایي استفاده مي نمايند كه به شرح زير مي باشد:
اسيدشویي(Pickling): از مواد شيميایي جهت تميز كردن سطح فلزات استفادـه مي نمايند. گاهی برای تمیزکاری سطح فلز از روش الکترولیز استفاده می شود؛ مانند آبكاري سطحي فولادهاي زنگ نزن.

شست و شو با حلال (Solvent cleaning): این روش از تمیزکاری به دو طريق انجام می گیرد:
الف) قطعه هایي كه سندبلاست شده و نبايد گرد و خاكي بر روي آن وجود داشته باشد با حلالي مانند الكل سفيد؛ شست وشو داده مي شوند.
ب) قطعاتي كه سندبلاست گرديده و بعد از آن آغشته به روغن مي باشند، مورد استفاده قرار می گیرند که با محلول مشخصی White Spirit مورد شست وشو قرار می گیرند.
تميزكاري مكانيكي:
- با تراش کاری و ماشین کاری (Machining) می توان ناصافی های ضخیم را از بین برد.
- با سنگ زنی سطوح قطعه را صاف و بدون مک می کنند.
- تمیزکاری دستی (Hand cleaning)(سنگ زنی دستی و سوهان کاری) که پلیسه ها یا اثرات تعمیری جوش را از بین می برند.
- تمیزکاری با سنباده با درجه های متفاوت که می توان سطح فلز را با آنها تمیز کرد.
- تمیزکاری به وسیله برس های سیمی
- تمیزکاری به وسیله برس های برقی
- ماسه زنی (ماسه پاشی یا سندبلاست)، اکسیدهای سطحی و ماسه چسبیده به سطح قطعه را تا 2 میلیمتر از بین می برد.
- ساچمه زنی (ساچمه پاشی یا شات بلاست) با ساچمه های چدنی یا فولادی با قطر های متفاوت براساس سایز و جنس قطعه
- تمیزکاری سطح قطعه با پاشش ذرات آب با فشار زیاد (Jet blast)
رایج ترین روش آماده سازی سطوح قطعه، ماسه زنی (Sand blast) و ساچمه زنی (Shot blast) است.
ماسه زنی یکی از طریقه های تمیزکاری سطوح قطعات است که در آن با استفاده از فشار زیاد هوا، مواد ساینده را با سرعت زیاد بر روی سطح قطعه می پاشند. این روش مشابه سنباده زدن با ورق های سنباده است با این تفاوت که مشکلاتی از قبیل ایجاد گوشه یا برآمدگی در سطح پایانی به وجود نخواهد آمد. بدلیل اثابت شدید ذرات ماسه بر روی سطح قطعات تمامی برجستگی ها، ناخالصی های سطحی شامل ماسه های باقیمانده، زنگ و… از روی سطح قطعه پاکسازی می شود. این روش متداول ترین روش تمیزکاری قطعات در صنعت است که به طور گسترده در صنایع مختلف مورد استفاده قرار می گیرد.
ویژگی های ماسه زنی:
- سطح قطعه صاف و براق می گردد.
- در صورت نیاز می توان سطح قطعه خشن، مات و زبر گردد.
- درجه زبری بوجود آمده بر روی سطح قطعه به جنس و اندازه مواد ساینده و دستگاه بستگی دارد.
روش کار ماسه زنی
در اين فرآیند دستگاه توليد هواي فشرده (كمپرسور) هوا را با شيلنگ به مخزن ماسه وصل مي کنند. ماسه از مخزن به صورت كنترل شده در مسير هواي فشرده قرار مي گيرد و از نازل خروجي با فشار خارج مي شود. درصورتی که نازل خروجی دستگاه به طرف سطح فلزي گرفته شود سبب پاکسازی و تميز و زبر شدن سطح مي شود. قبل از شروع ماسه زنی سطح فلز بايد بازرسي شده و آلودگی هاي روغني با تينر تميز شوند.
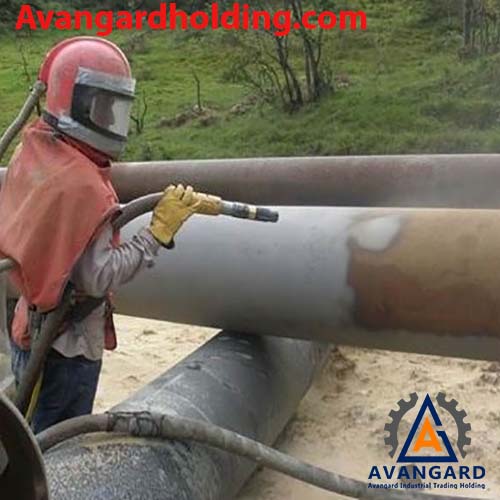
در این روش، سطح فلز توسط پرتاب ساچمه های فلزی تمیزکاری می شود. انرژی لازم برای پرتاب ساچمه ها از یک توربین تحت نیروی گریز از مرکز به وجود می آید و قطعه در یک اتاقک مورد بارش ساچمه ها قرار می گیرد. فلسفه پیدایش این ماشین ها به منظور حذف نیروی انسانی، کاهش هزینه ها و معضلات زیست محیطی بوده است. از طرفی در هر مکانی قابل استفاده و سرو صدای کمتری ایجاد می کند. در این روش امکان جمع آوری ذرات فلزی وجود دارد. محدودیت های بهداشتی این روش نسبت به ماسه زنی کمتر است و دیگر نیاز به فضای محصور و مراقبت های زیست محیطی شدید را ندارد و از سرعت عمل بیشتری نیز برخوردار است.
روش کار ساچمه زنی
در این دستگاه ها ساچمه های فولادی به وسیله توربین های دستگاه، توسط پره هاي پارو مانند که قابلیت تغییر داشته و خیلی سریع هستند، شتاب می گیرند. مواد ساینده در طول شعاع چرخشی پره ها حرکت کرده و با سرعت زیاد در جهت قابل تنظیم و تعیین شده برخورد می کنند. همین که ماده ساینده با سطح برخورد کرد آن را تمیز می کند، سپس ماده ساینده کمانه کرده و داخل اتاقکی می شود که مجدداً مورد مصرف قرار می گیرد، ماده ساینده قابل مصرف از گرد و غبار و مواد اضافی جدا شده و مجدد استفاده می شود. ساچمه زنی عمدتاً در کارهای صنعتی و قطعات با تیراژ بالا استفاده می شود.
با استفاده از ساچمه زنی یا شات بلاست (Shot blast) می توان ماسه چسبیده به قطعه و زنگ احتمالی قطعات را حذف و یا قبل از رنگ آمیزی و آبکاری برای بهبود چسبندگی رنگ به سطح قطعه اقدام به زبر کردن سطح قطعه کرد.
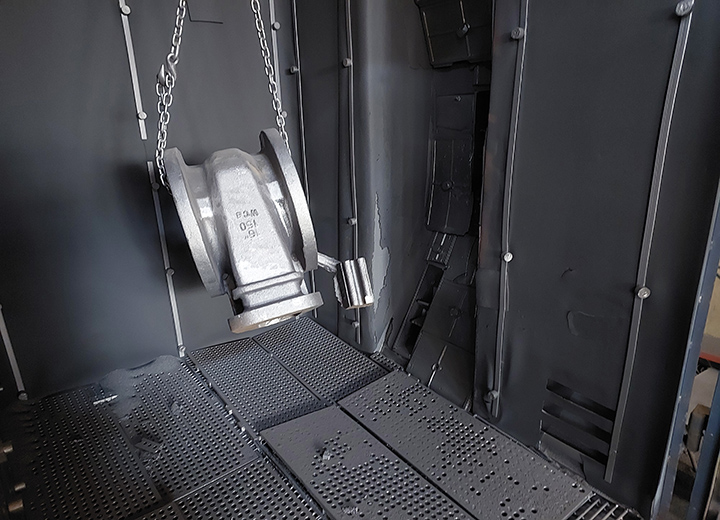